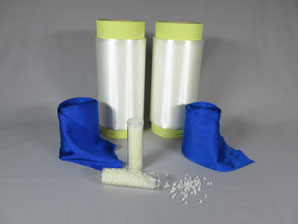
Source: DITF
A new class of textiles combines high flame retardancy with improved physical properties
TW Special Report
The burner flame approaches the tissue. But instead of suddenly flaring up, the textile sample only hesitantly begins to melt. First the tissue only contracts, then dark polymer drops fall off only later.
“What we see here in the combustion chamber is the result of a new type of flame retardant for polyamide textiles,” explained Dr. Georgios Mourgas. As a scientific staff member at the DITF Denkendorf, he is in charge of a project aimed at incorporating flame retardant compounds into polymer compounds in an entirely new way.
“Flame retardant phosphorus compounds are usually added to the polymers as additives,” said Dr. Mourgas. “However, large quantities of phosphorus compounds are required to achieve a good fire protection effect. And this usually occurs at the expense of the physical and physiological properties of the textiles.” Dr. Mourgas lets plastic granulate trickle through his hands. It consists of a polyamide that has been chemically modified in the DITF laboratories. In contrast to the usual method of adding phosphorus compounds to the polymer as an additive, these could be incorporated directly into the polymer chains in low concentrations. This occurs during polycondensation, i.e. the synthesis of the plastic in reactor vessels. This chemical process is usually designed to produce molecules with as long a chain as possible, i.e. polymers with a high molecular weight. This is a precondition for the subsequent ability to spin the polymer granulate into textile fibers.
New Process For Lower Phosphorus Content Levels
But that is also where the difficulty lies: When added in large quantities as an additive, these phosphorus compounds prevent the formation of long molecular chains and thus act as chain breakers. The resulting plastic cannot be processed into fibers at all or only with great difficulty, and the additive leaks from the fibers over time as a result of ageing and washing processes.
The process developed at the DITF is more elegant: Only small amounts of phosphorus compounds are required to achieve comparably good flame retardancy. The compounds are chemically coupled to the molecular chains and thus bonded to the polymer much more firmly than would be possible with additive admixtures. “We call these polyamides intrinsically flame retardant,” explained Dr. Mourgas. “This means that the flame retardant is built directly into the polyamide. This allows us to achieve a permanent, long-lasting flame retardant effect”.
By reducing the required flame retardants, the achievable molecular weight can be controlled much better during synthesis. The viscosities of the plastic melt can be precisely adjusted to guarantee the optimum ability to spin the polymer into fibers.
Good Skin Compatibility Of The Polyamides
Laboratory tests have already shown that the flame retardancy is just as good as that of polyamides to which additives were added. In addition, the chemical bonding of the flame retardants to the polymers prevents migration and leaching from the fibers due to ageing, as is observed with the use of additives. Not only does the flame retardancy remain completely intact, but the physiological skin tolerance is also improved: Intrinsically flame-retardant polyamides release virtually no phosphorus compounds. Skin compatibility tests rate this type of polyamide as good.
Finally, the good physical properties of intrinsically protected polyamides should also be mentioned: Dyeing tests with different dyestuffs confirmed good color absorption and light fastness of the textiles. Strength values and friction fastness are in no way inferior to those of commercially available polyamides.
“In their application, textiles made of our intrinsically flame-retardant polyamides show their advantages especially where high flame-retardant requirements are placed on the materials,” Dr. Mourgas describes the practical use of the new polymers. “This is especially the case in the home textile sector with carpets, upholstery and seat covers or curtains.” However, as is often the case with new developments, further fields of application may open up as soon as the product becomes available on the market.
Editor’s Note: This article is courtesy of Germany-based Deutsche Institute für Textil- und Faserforschung Denkendorf (German Institutes of Textile- and Fiber Research). For more information, please contact Dr. Georgios Mourgas, +49-0711-9340-396; georgios.mourgas@ditf.de.
December 14, 2018