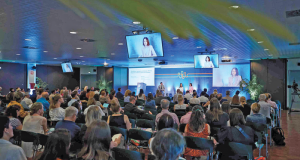
featured a panel presentation titled
“The Global Legislative Landscape: What to
expect for Fashion, Sport and Footwear.”
ITMA 2023 emphasized innovations and other drivers for a circular economy
By Dr. Karen K. Leonas
ITMA 2023, Transforming the World of Textiles, provided insight to current and future issues facing the global textile complex. There were opportunities to learn about new and innovative technologies being developed and implemented to address these issues. There was a notable focus on sustainability and circularity throughout all sectors of the supply chain including new fiber development, processing, yarn production, fabric production, finishing, cut-and-sew operations, and recycling.
In addition to numerous exhibitors showcasing their products, there were ITMA live sessions, Innovator Xchange panels and presentations, and ITMA Innovation Awards related to Sustainability and Circularity. During ITMA, Planet Textiles 2023, a two-day conference sponsored by the Sustainable Apparel Coalition (SAC), explored trends and the latest thinking on circularity, sustainability, and identified drivers that will shape the industry of the future. With more than 111,000 visitors and 1,700-plus exhibitors, ITMA provided opportunities to network with all those involved and gain insights on technologies and trends shaping the future of textile recycling.
Recycling & Environmental Sustainability In The Global Textile Complex
Reclaiming and reusing postindustrial waste has been a common practice throughout many textile industry sectors for decades. Postconsumer recycling is an emerging area of interest that has unique challenges requiring the development and use of innovative technologies to reach the goal. This article focuses on the drivers, challenges and solutions to post-consumer waste collection, separation, and recycling; and many such solutions were highlighted at ITMA 2023. There were numerous new technologies introduced, as well as innovative uses of existing technology that allow for the steps in textile recycling to be mechanized, automated and combined. Legislation, both in development and soon to be implemented, was reviewed, and noted as a driver in moving toward fiber-to-fiber recycling and circularity in the global textile value chain. It is also noted that numerous partnerships among companies in various sectors of the supply chain have been formed and are contributing to the transformation of the industry.
Textile production, from fibers to consumer products, often is resource intensive requiring large amounts of water, energy and chemicals depleting the world of natural resources. These processes can pollute the air, and water, and are known to produce greenhouse gas (GHG) emissions and impact the biodiversity of the environment. Recycling textile products at the end of life can reduce this depletion of natural resources, reduce pollution and help reduced the strain on the planet’s environment. In this article, recycling includes breaking the product down to the fiber level or its base molecules/monomers in support of the circular economy and closed-loop manufacturing is the interest and the focus. This level of recycling is completed using chemical or mechanical processes depending on the raw material being recycled and intended future use. Recycling will provide raw materials from which new products can be manufactured
There is an overabundance of post-consumer textile waste. Carolyn Chun noted that according to McKinsey, roughly 97 percent of all clothing eventually ends up in a landfill and within 12 months of its manufacturing date, 60 percent of clothing is in the landfill.1 Media pressure, consumer demand, regulations and technology are driving forces behind the move toward fiber-to-fiber circularity.
Textile Waste: Pre- & Post-Consumer
Waste can be categorized as pre- or post-consumer. Pre-consumer waste is from the manufacturer and never makes it to the consumer or retailer. It can also be classified as post-industrial waste. Cutting room floor scraps, rejects, trimmings, threading or end of process waste are examples of post-industrial waste. For years, companies have found ways to reuse or sell this waste diverting it from landfills and sometimes it is used in other products. An advantage of pre-consumer versus post-consumer waste when considering reuse and recycling is there is a better understanding of the raw materials in the waste stream.
Post-consumer waste includes items that have been used by the consumer, disposed of, and diverted from the landfill. Post-consumer waste contains mixed material that is difficult to recycle. Although not truly post-consumer, 30 percent of garments produced are not sold and are commonly landfilled or burned, which also are potential raw materials for fiber-to-fiber recycling.2
Fiber-To-Fiber Recycling Of Post-Consumer Textile Waste
Numerous challenges have been identified regarding textile and apparel recycling in general and specifically related to post-consumer waste. Some critical challenges for effective fiber-to-fiber recycling include garment disassembly and fiber identification. As apparel and other textile products are commonly made of multiple components from various materials, a frequently identified challenge is the use of mixed materials within the products. These can include various fasteners and embellishments as well as various fabrics of different fibers within the garment. In many cases, the fabrics are made from unknown fiber blends, which is problematic in the recycling process. Remembering that the different materials are recycled differently, the presence of mixed materials has previously limited effective fiber-to-fiber recycling.
When post-consumer waste is collected, the first step is sorting. Sorting is most commonly a manual process and there are numerous criteria — sometimes up to 60 sorting categories are used. Initially, those products of “high value,” identified as designer goods vintage items, are removed for high-end resale. Then items suitable for resale through thrift shops are identified and removed. The remaining products may be identified as suitable to sell to rag dealers, and fiber content is of importance in determining how functional they will be in this application.3
To move the remaining goods to recycling so the fibers and/or raw materials can be reused, resulting in effective closed loop manufacturing, it is important to accurately identify the raw materials. This is critical in determining appropriate recycling techniques — chemical or mechanical — and potential end-uses.
Fiber Content
In 2021, polyester had a market share of 54 percent of total fiber global fiber production, followed by cotton and other natural cellulosic fibers with about a 28 percent market share, man-made cellulosics about 6.4 percent and nylon accounting for approximately 5-percent market share.4/sup> In the clothing industry, more than 68 percent of the fibers used in apparel are synthetic fibers, primarily polyester,5 followed by cotton. Blends of cotton-polyester — such as 65/35 and 50/50 —are commonly used in apparel products.
The majority of products contain multiple fibers that have been intimately blended and therefore it is difficult to separate the fibers. Historically, determining the materials within the product was cumbersome and has been achieved using a specially trained workforce that can identify fiber content by touch or others who examine the labels for this information. Next, the products need to be disassembled to remove non-textile components as this would interfere with the recycling process. As these processes are completed manually, they are time consuming and create a bottleneck in the recycling process.
Fiber Content Determination
Technology was presented at ITMA 2023 that aids in the identification of fibers using near infrared (NIR) spectroscopy. NIR uses the unique signature based on the chemical composition of the fiber for sorting that may be completed incredibly quickly. Several companies at ITMA were promoting this technology including Belgium-based Valvan N.V. — a provider of high-tech sorting and baling systems — and Austria-based Andritz AG, among other companies. These two companies also have combined various technologies, partnering with others, to provide sorting and recycling systems.
Valvan has developed a library of fiber signatures and when the NIR signature from the fiber is compared with those in the library, the fiber is identified in milliseconds. The identification system, Fibersort™, uses artificial intelligence (AI) to predict the concentration of fibers. Fibersort can also separate by colors using an RGB camera. The quick identification allows this technology to aid in fast automatic sorting of the product. Valvan has stated that there is 99 percent accuracy on single fiber materials and 95 percent accuracy on blends.
Andritz recently announced a partnership with Pellenc ST and Nouvelles Fibres Textiles, both based in France, to establish the first combined industrial scale automatic textile sorting line in France. Technologies in Pellenc ST’s Mistrial machines use NIR, visible spectrometry, induction, and X-rays with NIR suitable for fiber identification.
Product Disassembly & Separation Of Fibrous/Non-Fibrous Components
Products must be disassembled by removing fasteners — such as buttons, snaps or zippers — and embellishments — including leather patches, studs and sequins — before moving to fiber recycling. The garment pieces are cut and innovative technology capable of identifying and removing the non-fibrous materials from the waste stream was demonstrated at ITMA. The technology pulls any garment components containing non-fibrous materials such button or zippers and removes them from the product stream while only fabric pieces move forward to the next step, which is shredding.
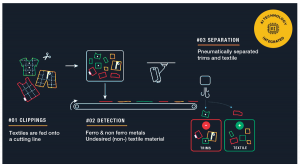
Both Valvan and Andritz demonstrated technology at ITMA that effectively separated non-textile components from the base fabrics that are found in post-consumer textile waste. Both companies have combined new technology to develop systems that have the potential to transform the textile waste industry and help the move towards a circular economy. Valvan’s technology first determines the fiber content before clipping the garment into smaller pieces and then feeding them into the Trim-clean™, a highly effective system for removing zippers, buttons, labels and other non-textile raw materials (See Figure 1). The undesirable components are pneumatically separated from the textile. This increases the purity of the feedstock resulting in both quality and reliable feedstock for fiber-to-fiber recycling. Valvan creates solutions for all steps in the recycling process including supply systems, bailing systems and sorting.
Andritz also demonstrated technology that successfully separates non-textile components from the fabrics. Like Valvan, the Andritz system covers several segments in the textile industry from sorting, shredding and mechanical recycling. The equipment shreds the fabric while simultaneously removing heavy and metal parts including buttons zippers, rivets and other embellishments commonly found in apparel. Andritz is moving forward into both chemical and mechanical recycling through collaborations with international partners.
Fiber Separation & Regeneration
Technology that can instantly identify fiber content in the sorting process and then remove non-textile components from post-consumer textile waste has been described. However, until recently, it has not been possible to separate fibers in multifiber blended fabrics and therefore fiber-to-fiber recycling has been limited to those products of a single fiber. As the push for recycling continues, technology to separate garments containing blends of fibers is critical. Through various panels, presentations and various networking events, companies pioneering fiber separation from mixed textile materials were present at ITMA.
Representatives from Circ, Ambercycle Inc., and Renewcell shared information about their technology that successfully separates the different fibers in fabric blends and the production of new fibers from the recycled raw materials.
Circ, Danville, Va., has flexible technology that is capable of separating synthetic fibers from cellulosic content; capturing the majority of the raw materials so it can be remade into high-quality fibers to be used in future clothing. The company initially focused on biofuel production, but now is applying a technical solution to blended textile fabrics. In an interview with Elle magazine, Peter Majeranowski, Circ CEO, stated: “A key step in a fully circular fashion system is creating technology to break down textile waste and create new fibers from it [and then] creating garments that are using fibers made from recycled textile waste.”6 Circ uses a hydrothermal processing technology to treat and separate the fibers.
Aksay Sethi and Moby Ahmed founded Los Angeles-based Ambercycle in 2015 as they developed a breakthrough technology using a biological recycling process that enables the molecular separation of different fibers, such as cotton and polyester. This process, known as Ambercycling, produces regenerated materials from post-consumer waste that has been separated and purified at the molecular level. In their process, a whole T-shirt goes into a reactor, and using their patented process, polyester is recovered and reformed into a yarn. These newly regenerated materials can then be made into fabrics for new garments. This not only reduces garments from going into landfills but also reduces the need to use new resources. Ambercycle introduced Cycora® which has been designed to serve as a direct replacement for polyester used in apparel. Cycora is a closed-loop circular yarn created using regenerated textile waste. Ambercycle also collaborated with Avery Dennison to create a unique, scannable QR code label, which allows for full traceability, transparency, and authenticity.
Renewcell was formed in Sweden in 2017 and its technology trans-forms cellulose waste into pulp and allows for the efficient reuse of chemicals. Renewcell’s goal is to recycle more than 1.4 billion T-shirts every year by 2030. The process still has limitations when recycling blends, however Renewcell’s technology can recycle clothes that are made of cotton and up to 5 percent non-cotton material like polyester.
Legislation Driving Textile Recycling
There are numerous drivers moving industry and consumers to a circular economy. Increased awareness of the environmental impact of the global textile complex through scientific reporting, social awareness, and ease of access to information is one of these drivers. Another driver is legislation related to textile waste, both pre- and post-consumer waste, and in some cases the implementation of Extended Producer Responsibilities.
Specifically, the European Union’s Waste Directive Framework requires countries to separate all textile waste by 2025, and the Circular Economy Action Plan ensures that circular economy principles are applied to all textile manufacturing products. These actions have pushed forward the technologies discussed here and support their implementation so companies throughout the supply chain will be in compliance with such legislation.
The SAC-organized Planet Textiles conference that took place during ITMA 2023 highlighted upcoming legislation during a panel presentation titled “The Global Legislative Landscape: What to Expect for Fashion, Sport and Footwear.”
The panel was moderated by Baptiste Carriere-Pradal, co-founder and director of 2BPolicy, and featured speakers ESG, Simple Approach General Manager Ilishio Lovejoy and New Standard Institute Director Maxine Bédat. Current and future legislation is expected to impact all sectors of the value chain.
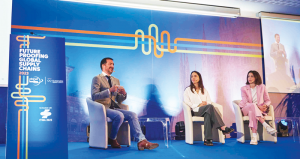
Carriere-Pradal began the session with an overview and noted that 10 years ago it was thought that consumers would be the drivers of a change to more environmentally and socially sustainable goods, and brands would change things to meet this demand by ensuring the choices they provide to consumers are made with a “fairly minimum impact.” However, Carriere-Pradal noted that is it now the citizens that are requiring change which has resulted in an increase in legislation addressing the way products are designed, sourced, manufactured, marketed and what happens at end of life. Chun1 noted that regulatory trends are also a factor influencing the landscape of sustainability within the global textile complex and regulation will factor into future innovation development and implementation. Many of the legislative acts mentioned during Planet Textiles relate to transparency and traceability of the product. Increased transparency will allow more accurate and easily accessible information regarding product raw material content and processing and will aid in the recyclability of post-consumer textile waste. Following are the pieces of legislation discussed and or mentioned during the Planet Textiles session. It is expected this legislation will drive the development and implementation of innovative technologies leading to a more sustainable industry.
The Fashion Sustainability and Social Accountability Act — also known as the New York Fashion Act — was a bill introduced in the New York Assembly in 2022. However, the bill did not move forward because of lack of support. A 2023 version of the bill was reintroduced, which stalled in the last session. The act has the four key elements of supply chain map-ping, due diligence, adverse impact disclosures and targeted impact reduction.7 During the Planet Textiles panel presentation Bédat noted that this bill includes due diligence language incorporating what has other-wise been voluntary. The approach is requiring the fashion seller and/or brand to set and achieve science-based targets. “The idea is not to put the information on the consumer and have the consumer do decide and decipher any labeling,” Bédat said. The brand will set the goals and decide how they will structure their business to meet these goals. There is language within the New York Fashion Act, of not only what the fashion seller/brand has to do, but also what information regulators must provide and make available to prevent lack of clarity about what is the responsibility of the supply chain and seller.
The aim of the Corporate Sustain-ability Due Diligence Directive (CSDDD) adopted by the European Commission in February 2022 is to “foster sustainable and responsible corporate behaviour throughout global supply chains …. requiring companies to identify, and where necessary, pre-vent, end or mitigate adverse impacts of their activities on …. the environment for example pollution and biodiversity loss,” as well as “anchor human rights and environmental consideration in companies’ operation and corporate governance.”
When referring to the CSDDD during the Planet Textiles panel, Carriere-Pradal stated, “…even if this obligation will be for the people putting the product on the market, it’ll have definitely ripple effect for every-body in the value chain, so there will be changes throughout the industry.”
The Corporate Sustainability Reporting Directive adopted by the European Parliament in November 2022, strengthens and expands sustainability reporting to move to a green and sustainable economy. This framework will be introduced in phases beginning in 2024. It includes reporting on environmental and social aspects and how related issues impact their business and how their operations affect people and the planet. Items related to environmental areas include science-based tar-gets, E.U. Taxonomy, and climate risk related reporting.8
On March 30, 2022, the proposal for a new Ecodesign for Sustainable Products Regulation (ESPR) was published by the European Commission, which will improve product circularity, energy performance and other environmental sustainability aspects. It allows performance and information requirements to be set for most categories of physical goods placed on the European Union market. The requirements cover a broad range including product durability, reusability, and reparability, recycled content, carbon, and environmental footprints, including Digital Product Passport. The ESPR proposal will apply to all products placed on the E.U. market whether they are produced inside or outside of the European Union.
Transformational Change Is Coming
ITMA 2023 provided the opportunity to learn about the trends impacting sustainability and circularity within the global textile complex. With increased media attention and consumer awareness on the environmental impacts of textile industry, technology, and legislation, there is a transformational change coming in the future. Innovations that allow the mechanization and automation of textile sorting, fiber identification, and the creation of new fibers from textile pre- and post-consumer waste are being developed and implemented as the textile industry moves to meet this change. Both start-ups and well-established companies are taking leadership roles through all sectors of the textile and apparel supply chain to meet the new criteria imposed on the industry. Increased collaboration among non-governmental organizations, industry and academia are tackling the complex issues facing the textile industry. New collaborations, innovative technologies, increased consumer awareness and legislation are driving this transformative change.
References:
- Chun, C. (2023, June 11) “The Recycling idea at Levi’s, Adidas, Zara to stop trillions in fast fashion from going to waste”, CNBC. Retrieved from https://www.cnbc.com/2023/06/11/a-recycled-idea-at-levis-adidas-to-stop-clothing-from-going-to-waste.html
- Rudenko, O. (2018, December 10) “The 2018 apparel industry overproduction report and infographic” ShareCloth.com Retrieved from https://medium.com/nataliya-makulova/the-2018-apparel-industry-overproduction-report-and-infographic-by-sharecloth-284cda8f1f9
- Englund, F., Wedin, H., Ribul, M., de la Motte, H., and Ostlund, A. (2017) “ Textile tagging to enable automated sorting and beyond-a report to facilitate on active dialogue within the circular textile industry”, Mistra Future Fashion report number 2018:1, RISE Research Institute of Sweden, 2017.
- Textile Exchange, (2022), Preferred Fiber & Materials Market Report. Retrieved from https://textileexchange.org/app/uploads/2022/10/Textile-Exchange_PFMR_2022.pdf
- Chen X, Memon HA, Wang Y, Marriam I, Tebyetekerwa M. (2021) Circular economy and sustainability of the clothing and textile industry. Mater Circ Econ. 2021;3(1):12. doi: 10.1007/s42824-021-00026-2. Epub 2021 Jul 6. PMCID: PMC8257395.
- Chong, D. A. (2023, May 5) “The future of fashion is circular- here’s how major fashion brands are adapting. Elle. Retrieved from https://circ.earth/the-future-of-fashion-is-circular-heres-how-major-fashion-brands-are-adapting/
- Lupo, A.V., Santos, A. M., Roque, R. E., Xu, F.A., and Lewis, E.B. (2023, July 17) “ New York’s fashion sustainability and social accountability act – Round 2 underway”, ArentFox Shiff, Retrieved from: https://www.afslaw.com/perspectives/alerts/new-yorks-fashion-sustainability-and-social-accountability-act-round-2-underway
- Crabbendam, N. (2022, December 15) “Corporate Sustainability Reporting Directive (CSRD) Explained”, Carbon Trust. Retrieved from https://www.carbontrust.com/news-and-insights/insights/corporate-sustainability-reporting-directive-csrd-explained
Editor’s Note: Dr. Karen K. Leonas is a professor of Textile Sciences in the Textile and Apparel, Technology and Management department at Raleigh, N.C-based North Carolina State University’s Wilson College of Textiles, as well as co-chair of the Wilson College Sustainability Committee.
September/October