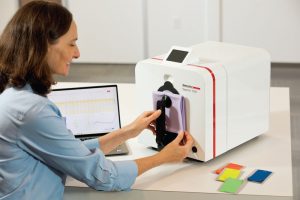
Matching florescent hues can be challenging, but digital strategies can help manage the process.
By Ken Butts
Designers and colorists know how difficult it can be to get fluorescent colors right. Yet it’s also undeniable that these colors have a very strong draw on consumers across multiple categories, including sportswear, swimwear, and more. So despite the difficulties they present, the payoff can be great.
But what makes fluorescent colors so hard to achieve?
Shedding Light On The Challenge
Most colors become darker as more dye or pigment is added to the fabric or other substrate. The results can be measured precisely using a spectrophotometer — a device that reports the amount of light reflected from the material across the visible spectrum. This measurement, known as a reflectance curve, effectively provides a “fingerprint” for the color and enables extremely predictable matching.
Fluorescents, conversely, work in the opposite way. As fluorescent dye is added, the fabric absorbs more ultraviolet (UV) light and reflects it as visible energy — making colors brighter and more intense.
Figure 1 shows the reflectance curves for several common fluorescent colors. All four numbers have values that exceed 100 percent. This means they’re reflecting more energy than was present in the visible portion of the light source when they were measured — which makes the samples look brighter than non-fluorescent colors.
“The hardest part about fluorescents is setting expectations with designers and merchandise partners in terms of what is feasible,” said Kristen Bell, manager of color development for Carhartt Inc. “Design loves them because of the lift they provide to the floor and they’re eye-catching for the consumer. But not all substrates can match to our standards.”
In simple terms, the math that underlies color science — and by extension, color matching software— cannot handle fluorescence. This makes computer recipe formulation impossible, and color approval more challenging — especially when colors need to match across two or more material types. In addition, computer monitors can’t accurately display or calibrate hyper-bright colors, further complicating digital workflows.
John Newton, head of color technology for Coloro, a global color standards provider, also pays close attention to the challenges of color fastness when dealing with fluorescents. “The property of these dyes just means that they fade a lot more quickly than standard dyestuffs,” he explained. “The other thing is that people love these colors in swimwear. Then you’ve not only got sunshine, you’ve got chlorine and salt — all enemies of dyestuffs.”
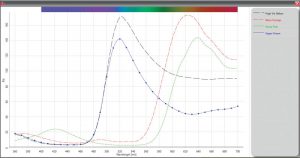
Can Fluorescent Colors Be Measured?
The simple answer is yes. But there are several considerations to bear in mind.
For a spectrophotometer to produce accurate data when measuring these colors, it’s critical to certify the UV capabilities of the instruments used. This should be done once a year to ensure repeatability and reproducibility of measurements.
Second, and perhaps even more importantly, the reflectance of fluorescent samples is affected by the UV energy output of the lamp used by a spectrophotometer. For example, in instruments with a xenon flash lamp, the amount of UV energy produced by the flash will vary over time. The UV content must therefore be calibrated using special UV standards to ensure the sample is exposed to a consistent amount of UV energy.
Variances between instruments that can affect the overall energy out-put, such as the age of the lamp or the condition of the sphere, also can result in very different measurements. This can be especially challenging if a supply chain has a mix of old and new instruments. The best repeatability can be achieved if instruments and their flash lamps are of similar in age and condition.
Another challenge when evaluating fluorescent colors is that some have very specific acceptability standards. Samples of “blaze” or hunter orange, for example, must be measured in accordance with ANSI or ASTM requirements. Although this may not be possible with a sphere instrument, the relative color difference can be evaluated an acceptable standard has already been established. In this way, a pass/fail program that measures production samples against a standard before submitting them for certified testing can effectively be created.
The Digital Advantage
Many textile companies are just beginning to realize that fluorescent samples can be measured in this way and are recognizing the potential benefits.
Without a digital process, a supplier who is up against a tight dead-line may go ahead and send a large fabric order to the cutting stage without verifying the exact color match. By the time any issues are discovered, a manufacturer may face the difficult choice of sending a product that doesn’t meet expectations to retailers or disposing of it. Either option risks a potential loss of revenue.
By providing a more accurate and objective way to measure fluorescent colors, digital measurement enables suppliers to evaluate their production against a digital standard. This saves time and costs by reducing the number of physical samples that need to be shipped back and forth — and makes it easier for customers to hold their suppliers accountable.
Dye houses also can leverage this technology to take a more proactive approach to educate their customers. Since design and product management teams have become accustomed to what color matching technology can do with non-fluorescent colors, they often don’t understand why a dyer can’t be expected to match any fluorescent color they choose.
A better approach is for dyers and color standards providers to educate their customers with a library of shades they know they can achieve— the more robust the better. Given a selection to choose from, designers and producers can have confidence from the start that their fluorescent selections are achievable, or what the limitations will be when multiple substrates are involved.
Coloro, for example, has used laboratory testing to vet 244 fluorescent colors in polyester and can digitally predict their performances in other common substrates, including nylon, nylon-spandex, polyester-spandex and cotton.
“Knowing what will and won’t work ahead of dyeing anything at all— even a lab dip — is key,” Newton explained. “Then you can get the palettes engineered just using data. That’s the great thing about feasibility intelligence: we can predict before we dye.”
Newton also advises manufacturers to check with their supply chains as quickly as possible to make sure their vendors can source the necessary dyestuffs. “Not all fluorescent dyes are stocked in every region of the world,” he cautioned.
Toward A More Positive Experience
Digital color control has brought about positive experiences with traditional non-fluorescent materials. Achieving similar benefits with fluorescents is largely a matter of paying attention to a few extra details, from the age and condition of instruments to a better understanding of achievable shades.
Strategies like these enable manufacturers to continue taking advantage of the same digital instruments used for traditional colors. Ultimately, everyone will gain from the overall improvement in the quality of sample submissions, ongoing production and customer experiences. At the same time, producers gain the efficiency and sustainability benefits of reducing waste and shipping fewer materials.
Editor’s Note: Ken Butts is a Global Key Account Team manager with Lawrenceville, N.J.-based Datacolor.
July/August 2023