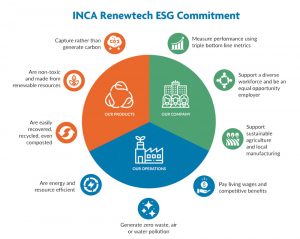
INCA Renewtech is using knowledge in plant genomics, hemp cultivation, fiber processing and composites manufacturing to develop new types of natural fiber composites.
By Camille Saltman
Powerful market forces are leading industry to adopt more environmentally friendly, domestically sourced materials in their products. These forces include government regulations to reduce plastics pollution, sequester carbon and achieve higher lifecycle performance. They also include investor focus on environmental, social and governance (ESG) initiatives. These metrics are now being used to measure investment risk and deter-mine the value of corporations. Equally important is growing consumer demand for less toxic, more sustainable products. Consumer purchasing repre-sents 70 percent of the U.S. economy and as customers change their buying patterns major brands are transitioning to recyclable products.
Price Affecting Adoption
These powerful market trends have led to significant innovations in biobased polymer chemistry and natural fiber reinforced materials. Today, many of the same products that are synthesized from hydrocarbon molecules derived from oil and natural gas can be produced from carbohydrates derived from agriculturally grown plants. This includes plastics, textiles, fertilizers, building materials, furniture, papermaking, packaging, and industrial fillers used in paints, plastics and adhesives, pharmaceuticals, nutraceuticals, and cosmetics.
The potential benefits of biobased materials are very promising. Petroleum-based products are energy intensive to refine, generate harmful byproducts in the process, and often are difficult to recover and recycle at the end of their useful lifecycles. Plant-based products sequester carbon, generate no toxic byproducts, and are much more easily recovered, recycled, or even composted. How-ever, there are two significant barriers to their wide scale adoption — price and performance.
Many biopolymers including poly-hydroxyalkanoate (PHA) and poly-lactic acid (PLA) are more expensive than petroleum-derived incumbents such as polypropylene (PP) and polyethylene. This is mainly because of scale. New materials have to compete with enormous, vertically integrated petrochemical companies that have invested billions of dollars in manufacturing infrastructure. Price is impeding the formation of the major industrial product development partnerships necessary to develop high performance solutions. Until more sustainable, biobased materials can compete on price, biomaterials will remain niche products.
Hemp Biomass For Industrial Use
Canada-based INCA Renewable Technologies (INCA Renewtech) is attempting to solve this pain point in the marketplace. Instead of procuring natural fiber from overseas, as competitors do, INCA is purchasing hemp biomass from Canadian farmers growing hemp seed for plant-based protein. The company will process this renewable resource into a set of proprietary high value products for major industrial customers.
Just as the petroleum industry leverages its expertise in exploration, extraction, and chemicals manufacturing to maximize financial return on every barrel of oil, INCA will leverage the company’s expertise in agronomics, fiber processing, composites innovation and manufacturing to maximize return on every bale of hemp.
Vertical Integration
To achieve this vertical integration INCA will build two factories — one in Alberta, Canada, within a 150-mile radius of hemp cultivation; and a second in Indiana within 150 miles of customers in the automotive, recreational vehicle (RV) and consumer products industries.
Hemp has been legally cultivated in the Canadian Prairies for more than 20 years where it is primarily grown for plant-based protein. The remaining stalks contain some of the strongest natural fiber on earth. If properly refined and manufactured, hemp fiber can function as a direct replacement for glass fiber in composites.
Whole hemp bales will be decorticated, a process that mechanically separates the long outer bast fiber from the short inner core, called hurd. The bast fiber will be further refined to create the ultra-clean material required for its products. In Alberta, the hurd will be used to manufacture INCA BioBalsa™, a product designed as a direct replacement for the balsa wood used in boats and wind turbine blades. The refined bast fiber will be sent via rail to the company’s second factory in Bristol. There it will be manufactured into three additional products — INCA BioPanels™ for the RV industry; INCA Prepregs™ for the automotive industry; and INCA BioPlastics™ for the consumer products industry.
Domestically sourcing and processing hemp lowers raw material and logistics costs and reduces sup-ply chain challenges, versus importing expensive jute, flax or kenaf from Southeast Asia, as other bio-composite manufacturers do.
A Brief History Of Hemp
Hemp, or Cannabis sativa L., was one of the first crops cultivated by man. Recorded use dates back more than 8,000 years. Hemp cultivation began in what is now China and spread quickly across Asia, Europe, Africa and later South America. It was such a strategic crop that in 1533 King Henry VIII fined English farmers if they did not raise hemp. Britannia could not have ruled the waves without hemp rope and canvas. Until the late 1800s, most of the paper in the world was produced from hemp pulp.
Hemp was originally introduced to North America in 1606 where it was grown for papermaking, cordage, lamp fuel and clothing. However, at the turn of the 20th century powerful forces set out to delegitimize the cultivar. It was seen as a direct competitor by the pulp and paper industry, and by Dupont, which invented nylon as a petroleum-based substitute for hemp textiles. Backed by powerful industry lobbyists, hemp was included in the 1938 Opium and Narcotic Drug Act in Canada, and the 1937 Marijuana Tax Act in the United States which essentially killed the hemp industry.
Hemp is experiencing a major rebirth in North America and around the world. In 1998, it became legal to grow hemp in Canada for commercial production. Canada’s Industrial Hemp Regulations, part of the Cannabis Act 2018, allows for whole plant utilization of the crop. In 2020, there were approximately 53,000 acres of hemp being cultivated and this is expected to expand dramatically as the market for plant-based protein and fiber grows for the following reasons:
- Hemp matures in as little as 90 days and can be grown with low water and chemical inputs;
- As a rotational crop it breaks disease cycles and has a long tap root that aerates the soil;
- It yields four times the biomass of a forest in one season, compared to 25 years of tree growth, and;
- Every portion of the plant can be commercialized, creating multiple revenue streams.
Segments Seeking Advanced Biocomposite Solutions: Recreational Vehicles
Since the 1970s, the recreational vehicle industry has been dependent upon rainforest hardwood plywood from Southeast Asia to construct side walls and roofing systems. Hard-wood plywood’s strength, light weight and smooth surface make it a product in high demand not only for RVs but also transport trailers, furniture, decorative paneling and even Hollywood movie sets. In 2021, the RV industry alone used 620 million board feet of lauan plywood. Unfortunately, the popularity of this material has led to devastation of primordial rain forests throughout Indonesia, Malaysia, Borneo and the Philippines. Plywood prices have sky-rocketed, quality has fallen, and manufacturers are actively seeking alternatives.
To construct an RV, sheets of ply-wood are seamed together like stick frame housing. Exterior wall panels are laminated with aluminum or fiberglass, and interior walls with paper or vinyl. Urethane foam insulation is sandwiched between the inner and outer walls. However, plywood off-gasses formaldehyde, absorbs moisture, and burns easily. After just a few years, seams telegraph through the exterior walls of the vehicles.
Oriented strand board (OSB) is much heavier than plywood and it too absorbs water and off-gasses formaldehyde. Fiberglass reinforced plastic panels are more expensive and labor intensive, and delaminate, warp, and offer poor insulative properties.
INCA has developed a revolutionary panel product made from a blend of hemp fiber and a proprietary thermoset resin system. The company has signed an exclusive sales agreement with Elkhart, Ind.-based Genesis Products Inc., which designs, engineers, and manufactures a range of products for the RV, construction, transportation, and furniture markets. Genesis has facilitated a product development agreement with Winnebago for the company’s entire panel production capacity.
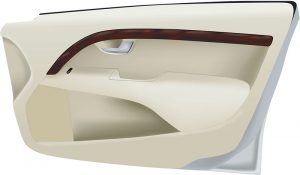
Automotive
The automotive industry utilizes resin infused panels, called prepregs, to mold 3D interior trim components such as door panels, seat backs, headliners and package trays. Prepregs can incorporate glass, natural fiber or even carbon fiber to reinforce the thermal melt polymer matrix. Prepregs can come in the form of flat panels or nonwovens such as those produced by Indiana-based companies FlexForm Technologies in Elkhart, and Carver Non-Woven Technologies in Fremont. The automobile industry was an early adopter of these prepreg materials because of their lower cost and high strength-to-weight ratio, which results in better fuel mileage and improved customer safety.
Automotive manufacturers heat these prepregs in hot presses, surface them with cover stock, and compression mold them into final 3D components. While nonwovens have proven to be of great value to the automotive industry, they depend upon expensive natural fiber such as jute or kenaf imported from South-east Asia. They also use a high percentage of polymer fiber, adding considerable cost.
On behalf of Toyota, INCA has developed a methodology to deposit a multi-layered mat of hemp and polymer fiber and consolidate the material on a twin steel belt press to produce thermoformable prepregs for the automotive industry. These prepregs will be stronger, improving side impact resistance, and lighter improving mileage. They can be easily recycled back into new products once vehicles have reached the end of their useful lifecycles.
Thermoplastics
Plastics are a multi-billion-dollar industry led by the world’s largest petrochemical companies. Thermoplastics such as PP, high density polyethylene (HDPE), and polyvinyl chloride (PVC) are used in packaging, furniture, flooring, roofing membranes, automobile interiors, medical devices, and countless other consumer products. Their relatively low cost, high moisture resistance, and ability to be heated and shaped using injection, compression or extrusion molding machines make plastics ubiquitous in the modern world. The top polymer producers include Dow Chemical, Lyondell Basell, Exxon Mobil, SABIC, INEOS, and BASF.
Most polymers are derived from petroleum or natural gas. Extraction and refinement of these raw materials generates millions of tons of carbon dioxide equivalents (CO2e). They often contain toxic chemicals that may bio-accumulate in humans and animals. As only 9 percent of plastic products are recycled, they cover the earth and pollute the oceans. Often thermoplastics are compounded with glass fibers to reinforce the polymer matrix and enhance structural properties. However, these materials increase the cost and weight of the resulting products. Glass fiber is extraordinarily energy-intensive to manufacture. It has high tensile strength, but low impact strength. Glass is also abrasive on processing equipment and difficult to recycle once products have reached the end of their useful life cycles.
Biobased polymers represent a small percentage of the millions of tons of plastics produced annually. However, the global bioplastics and biopolymers market is growing rapidly. Market drivers include industry and consumer demand for sustainable products, increasingly stringent regulatory mandates, and growing public concern regarding plastics pollution.
Europe has been the major hub for biobased innovation and currently produces 55 percent of all biopolymers, but capacity now is expanding rapidly in Asia and North America. Many of the companies leading the charge are agricultural bioscience companies, or petrochemical companies making the transition to plant-based chemistry.
Bainbridge, Ga.-based Danimer Scientific produces PHAs using oils derived from plant seeds such as canola and soy. The Netherlands-based Total Corbion operates a 75,000 ton-per-year PLA production facility in Thailand and has plans to build a second PLA factory in France. Plymouth, Minn.-based Nature-Works LLC, owned by Cargill and PTT Global Chemical, has a refinery in Minnesota capable of producing 300 million pounds of PLA per year from corn feedstock. While these polymers show great promise, they tend to be significantly more expensive than incumbent petroleum-based polymers and lower in structural performance.
INCA has developed a novel manufacturing methodology to replace glass fiber with natural hemp fiber as a reinforcement in polymeric composites. In INCA’s process, hemp fiber is refined to precise geometries and then blended with various polymers and additives under relatively low heat and pressure. This preserves the structural properties of the natural fiber as well as the polymer. Product benefits of INCA Bio-Plastics include cost and weight reduction, improved stiffness and impact strength, and lower wear on processing equipment. Unlike glass fiber, refined hemp fiber is more amenable to multiple recycling episodes without significant loss in structural properties.
INCA will formulate materials to meet customer specifications. For example, one company may want to utilize recovered PP to lower product costs and increase recycled content, while a second customer may specify a biobased polymer such as PLA or PHA to create 100-percent biobased products. These formulations will be brought together in the form of com-pounded “masterbatch” pellets, that can be shipped directly to manufacturers for use in their injection or compression molding operations with little or no modifications to their existing lines. Final products will be stronger, lighter and less expensive.
Wind Turbine Blades
The balsa tree, Ochroma pyramidale, is a large, fast-growing species native from southern Mexico to southern Brazil. Although classified as a hardwood, balsa is exceptionally soft and lightweight because the trunk of the tree has large cells that store water. When cut and dried these empty cells retain their structure, giving the resulting lumber exceptionally low density and high compressive strength. As a result of these properties, balsa is widely used as a core material in automotive, aerospace and marine applications.
Recently, balsa has become one of the most sought-after materials in the construction of wind turbine blades where it is used to reduce blade weight and increase blade stiffness, particularly in the root section where the mechanical forces are most demanding. This is accomplished by placing shaped balsa in the core of the blade and encapsulating it with styrene-resonated glass fiber to form stressed skin panels. Blade skins are put into tension on one side and compression on the opposite side and held in opposition by the balsa core to resist collapse.
Historically, most balsa wood came from the rainforests of Ecuador, but the species has been largely clear cut, with devastating impacts on ecosystems and indigenous communities. Sixty percent of balsa wood is now plantation grown. However, without the many years required to grow mature trees large enough to produce solid lumber, the industry has adopted end-grain balsa — essentially slicing logs across the grain, milling rectangular pieces, and gluing them back together to form board stock. This has added considerable cost to the product, reduced consistency and lowered technical properties. As a result, many blade manufacturers are turning to high-density polyethylene terephthalate (PET) and PVC foams in the tips and mid-sections of the blades. Unfortunately, foams are expensive and lack the compressive strength to replace balsa in the root section of the blades.
INCA engineers have developed a novel methodology to transform refined hemp hurd into a balsa-like material with high, uniform compressive strength, and a density of 10 pounds per cubic foot, the ideal weight for turbine blades. Unlike balsa wood, it can be formulated to increase moisture resistance, and “tuned” to be compatible with specific resin systems. Unlike PET foams, it has the sheer strength required for installation in all sections of the turbine blade, including the root section. These characteristics provide significant advantages to engineers who are no longer forced to compensate for variations in the material properties of plantation-grown trees.
INCA has signed a strategic development agreement with Switzerland-based Gurit Services AG to develop and manufacture BioBalsa. Gurit develops and manufactures advanced composite solutions for the wind energy, aerospace and marine industries. Its portfolio of structural core materials, prepregs, adhesives, and engineering services is recognized worldwide. Gurit’s customers actively are seeking alternative core materials that can deliver the compressive and sheer strength of balsa as well as meet aggressive sustainability goals.
Lifecycle Analysis
INCA commissioned Canada-based GreenStep Solutions Inc., an independent research and certification organization, to undertake a Product Life Cycle Analysis of the company’s products versus conventional alternatives utilizing the Greenhouse Gas Protocol Product Life Cycle Accounting and Reporting Standard.
The company’s in-depth report considered the impacts of industrial hemp farming, product formulations, raw material extraction and processing, energy and water inputs, product manufacturing, and fuel consumption at each stage of the process including downstream transportation and distribution. Their findings demonstrate that:
- INCA BioPanels will reduce carbon emissions by 76 percent, waste production by 89 percent, and water consumption by 82 percent com-pared to lauan rainforest plywood. One square meter will sequester 4.27 kilograms (kg) of CO2e.
- INCA BioPlastics when com-pounded with recycled polypropylene will reduce carbon emissions by 91 percent, waste production by 64 percent and water consumption by 59 percent compared to glass fiber reinforced plastics (GRP). One cubic meter will absorb 517.96 kg of CO2e.
- INCA BioBalsa will have 164-percent less carbon impact than PET and 107- percent less than balsa wood. Production will result in 93-percent less waste than balsa and 99.56-per-cent less than PET. It also means 93-percent less water consumption during manufacturing than for PET. One cubic meter of BioBalsa will absorb 262.31 kg of CO2e.
INCA’s goal is to deliver the trifecta to its customers — price, performance and sustainability — in order to overcome the current barriers to wide scale industrial adoption of biomaterials.
Editor’s Note: Camille Saltman is chief marketing and sales officer, INCA Renewtech
July/August 2022