The family-owned textile dyeing machinery company continues to innovate to meet today’s dyeing industry challenges.
TW Special Report
Thies GmbH & Co. KG is a family-owned and -run custom textile dyeing machinery company established in 1892. Currently, the fifth generation — siblings Verena, Christiane and Alexander Thies — manage the export-oriented business. Thies’ production facility in Coesfeld, Germany, produces its dyeing machines using components made by subsidiary companies based in Poland and Slovenia. “With a qualitatively and quantitatively strong team of young and experienced employees, we strive to develop innovative and sustainable solutions for practical use,” said Verena Thies. The company also promises a customer partnership with investment security and strong service. “We have built up a comprehensive network of dedicated service technicians, salespeople and agencies over the past six decades,” Thies added. “Hence, customers are optimally looked after locally, in their time zone and language.”
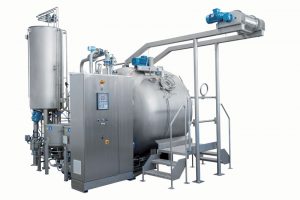
Modern Machines, Intelligent Controls
Thies strives to build dyeing machines that consume extremely low amounts of water and energy and feature efficient control technologies. It’s state-of-the-art iMaster series embodies these concepts in a modern dyeing machine. Chemical consumption, primarily measured in grams per liter (g/L) is largely dependent on the water consumption. In 1980, the complete dyeing cycle — including washing, dyeing and rinsing — required approximately 105 liters of water per kilogram of fabric. Today, the Thies iMaster series can achieve on average 28 L/kg on medium shades, which represents a reduction of 73 percent.
Sustainable Technologies
Sustainability is the driver for change. With this in mind, Thies has developed a new machine series — the Signature Series.
According to the company, the Signature Series not only achieves a further reduction in water consumption, but also lowers dye consumption and significantly reduces the amount of total dissolved solids (TDS) when processing cotton fabrics. Solids production as well as their treatment in wastewater treatment systems is very complex and ties up many resources.
Thies emphasizes that when talking about sustainability goals, the entire finishing process must be considered. “Fabric preparation — consisting of scouring and/or bleaching — and after-treatment processes often are not considered and sustainability efforts are limited to one process part — the dyeing,” Verena Thies noted.
Digital measurement and analyses of dyeing processes are key to process optimization, according to Thies. The company offers several tools for this purpose that optimize the recipes and dye curves. DyeControl, for example, is an automated system for more water-efficient dyeing and rinsing. This is achieved by individually adapting the required amount of water during the wet finishing process. Rinsing, washing and dye baths are measured and analyzed online. The visual representation of the process curves enables both a control of the turbidity and a determination of the dye extract from the liquor.
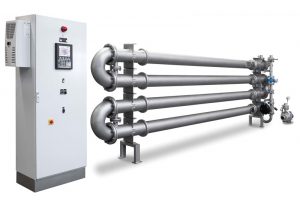
Heat Recovery Systems
According to Hardy Sullivan, sales, Thies Corp., Rock Hill, S.C., heat recovery systems are often not used in U.S. dye houses or they are undersized based on the needs of the plant. This is because they weren’t promoted initially when dye houses were purchasing equipment. However, today this is a technology included from the beginning when investing in new dye house equipment.
The Thies heat recovery system uses hot wastewater to heat up cold, fresh water needed for dyeing processes. According to the company, the level of benefit increases depending on the temperature difference, ∆t, between the hot wastewater and cold water. For example, a machine with a dyeing capacity of 500 kg dyeing three batches of cotton per day can save up to 80 percent of the steam needed with the consistent use of a heat recovery system. This results in a significant reduction in production costs as well as carbon dioxide emissions.
“It’s easy for dye houses without heat recovery systems to add one,” Sullivan said. “The Thies system is scalable for increased production. The closest installations of Thies heat recovery systems are in Central America, but several North American companies are showing interest, in part because of the savings in carbon dioxide emissions.”
Automation
The demand for automated machinery continues to grow. The advantages of automation are diverse — productivity rates can be increased and stabilized by the reduction of unproductive waiting times; automation increases occupational safety and the attractiveness of the work itself; and automation also may be used to counteract an ever-increasing shortage of skilled workers.
In yarn dyeing, bobbins are placed on the spindles of the bobbin carrier, which in the case of a 500 kg yarn carrier and a package weight of 1 kg, means 500 yarn bobbins must be loaded and unloaded. Thies offers robotics that can take on this time-consuming and physically demanding work, as well as locking/releasing the locking devices. The robotics can be programmed to avoid waiting times for the machines, and the bobbins and locking devices are damaged less frequently as a result of the automatic unloading. The prepared carriers can also be automatically loaded and unloaded into a horizontal yarn dyeing machine.
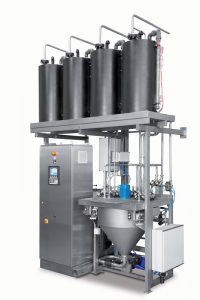
Thies also offers Multi Product Supply (MPS) systems for automated dye and chemical storage, weighing and dispensing. The system comprises MPS-L for liquids; MPS-D for dissolving dyes; MPS-S for solids; the gravimetric MPS-G; and at the highest level, the MPS-Colourmatic, which controls the entire path of the dyes from the warehouse to the dyeing system including storage, weighing, dissolving and provision in an automatic cycle.
According to the company, some of the advantages of the MPS systems include:
- Reduced occupational safety hazards for employees who less frequently or no longer come into contact with dyes and chemicals;
- No danger of spills, thus preventing plant damage;
- Automatically managed stock levels and auto-generated order proposals if stock falls below a predetermined level; and
- Increased productivity and reproduction rates.
Thies MPS system is a modular concept that can be implemented in small or large dye houses. The system can also be implemented gradually, making the investment economical. The systems also create a more transparent dyeing process, according to Thies. All additions are documented, and incorrect measurements and product mix-ups are prevented thus maximizing reproducibility. Down time also is avoided because the systems can prepare the dyes, chemicals and auxiliaries in advance. The synchronized system and production sequence ensures each product is available in the right quantity at the right time at the right machine.
The delivery precision of Thies’ liquid dispensing system is automatically checked, monitored and optimized. Therefore, recurring calibration is not necessary. The measurement of the supplied chemical quantities is performed volumetrically with the help of a magnetic-inductive measuring system. With integrated small quantity measurement, small amounts as little as 5 millimeters can be precisely supplied.
Sullivan reports that a relatively new manufacturer, American Merchant, Bristol, Va., has recently adopted Thies’ dye dissolver and chemical dispensing equipment. The terry towel manufacturer operates under the philosophy of supporting local farmers and workers by producing all-American made towels. American Merchant took over an abandoned factory space and invested a significant amount to bring in all new looms and other machinery including the Thies equipment. Its brand, American Choice Textiles, provides products direct to the consumer, and the company also supplies high-quality bath linens to retailers of all sizes.
Today And Tomorrow
It is clear that this established firm is dedicated to developing innovative and sustainable solutions for practical use. That being said, a company with five generations of institutional knowledge reaching back to 1892 definitely takes its craft seriously. But it’s the blend of history and ability to focus on the future that makes a difference — automation, sustainable technologies and modern machines featuring intelligent controls — that is Thies’ story today.
November/December 2021