Digital printing developments in various dye classes present challenges to adoption by traditional textile printers.
TW Special Report
From its introduction in the early 1990s, the promise of digital textile printing was enticing, but slow to develop. Initially, digital printing became a sample and development tool for designers in a preproduction environment. The technology was expensive, but found a niche in commercial printing for banners and signage.
Development Of Digital Printing
Printing speeds for early jet technologies were relatively slow compared to traditional printing methods and this hampered adoption by the textile industry. But printhead development brought speed into the equation; dyes, inks and substrates improved; and the color gamut available to the printer increased. Scanning technology and computational power also expanded capabilities.
Easing The Transition
For some textile printers, the transition from traditional to digital printing involves only minor changes to established processes, and offers great savings in the engraving and storage of traditional screens and other pre-print necessities and design constraints.
A traditional reactive printer adopting digital reactive printing will face fewer challenges than those printers trying to adopt a new dye class with significant processing changes.
Conventional And Digital Mix
Data provided by long time printing technology supplier Austria-based Zimmer Austria points to a 97 to 3 percent traditional to digital printing product mix, with 45 percent of the traditional printing achieved using pigments and 57 percent of the digital printing performed using a sublimation — transfer paper — process. Conventional printers also produce 27 percent of their output using reactive dyes, while digital printers use 36 percent reactive.
This presents an interesting contrast into the penetration of digital printing into the traditional market and the challenge for traditional pigment printers to adopt new dye class processing technologies.
Conventional Dyestuff Selection Criteria
When adopting digital printing for textiles, dye selection has not really changed regardless of the system. The addition of pre- and post- fabric coating options in digital printing can enhance the digitally printed fabric’s appearance and performance, which is a bonus for digital processes.
Reactive, pigment, vat, acid, and disperse dye classes, or inks, all retain the performance achieved through the years of traditional printing development.
Printheads and processes, including dye circulation, have evolved. For instance, reactive and acid dyes don’t require circulation in the digital print process, while pre-metalized dyes benefit from dye circulation. Disperse, pigment and vat dyes must be circulated.
These developments have reached a point where digital printing can meet the needs of the printer’s final product performance and where each dye class performs at its best.
Where Pigments Shine
There are many reasons why pigment printing holds a 45-percent share of the conventional printing market. Pigment printing is versatile in that it has few substrate constraints so one printing and processing system can print on many different fabrics — unlike for many of the other dye classes. It is also a fairly uncomplicated printing system, whether a conventional or digital printing platform is used. “What you see is what you get,” unlike the mysteries of other dye classes as they go through sometimes complex finishing processes to reveal the final color.
There also is the benefit of little wastewater, no solvents and low energy consumption combined with low initial investment and ability to achieve low print costs when using pigments.
End Uses
According to Zimmer, pigment-printed fabrics are suitable for applications in:
- home textiles;
- bed-Linen;
- upholstery;
- cushions;
- window fashions;
- outdoor fabrics; and
- print on panels.
Although there are many digital printing technology developers and suppliers in the evolving textile space, Zimmer Austria stands out with the development of its Colaris technology.
As a printing systems manufacturer, the company builds on more than 140 years in the textile printing industry and 45 years in digital printing with a deep knowledge of the complete textile and print process.
Zimmer’s Digital Path
In 1986, Zimmer offered the CHROMOJET 16 dpi for carpet printing, and introduced the high resolution 76 dpi printer for carpet in 2006 and towel printing in 2007.
In 2009, Zimmer developed the CHROMOJET 76 dpi with process color printing.
The following year, COLARIS entered the market targeting applications in home textiles, fashion, and flags and banners. The Colaris technology introductions continued with new products for narrow fabrics, digital carpet printing and more.
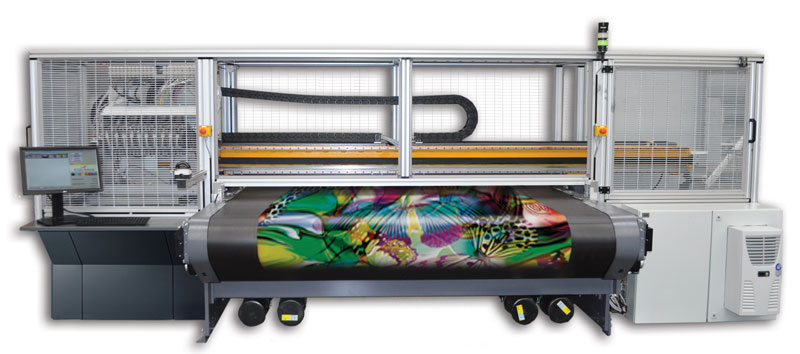
Digital Printhead Solution
The Colaris digital printing technology utilizes the Fujifilm Dimatix StarFire™ industrial printhead. Originally developed for the ceramics industry, the head features 1,024 nozzles per head, the RediJet™ ink circulation system and an integrated heating system. The printhead’s modular design makes it repairable with the changing of individual components. In order to add value and extend the system’s useful life, Zimmer opened the Colaris Printhead Reconditioning Center offering a repair service for a nominal fee.
Interestingly, Zimmer’s technology features an “open ink system,” which allows the printing company to choose its ink or dye supplier. Zimmer does test inks and dyes for performance in its printheads and system and can make recommendations to Colaris users.
Colaris Pigment Printers
The StarFire industrial printhead currently is the centerpiece of a family of seven Colaris pigment printers. The models range from print widths of 74 millimeters (mm) up to 3,400 mm, and feature square meter per hour (sqm/h) performance at 400 X 800 dpi from 140 up to 1,060 sqm/h. The Colaris family features six-color machines with a maximum 2 to 16 heads per color, depending on the model.
A Digital Future
As the promise of digital textile printing technology seemingly rounds the corner from a sample and development tool for designers in a preproduction environment to a full blown production process offering speed, quality and efficiency — digital print adoption by traditional printers is looked upon with optimism.
Solutions for conventional pigment printers to adopt digital solutions utilizing familiar finishing processes are available. Certainly costs matter and will the process transition savings — like screen engraving, rotary screen storage and management, repeat design constraints, and a smaller manufacturing footprint offset the costs of digital inks and maintenance? Those analyses are underway in many places and a digital future may happen sooner than expected.
November/December 2021