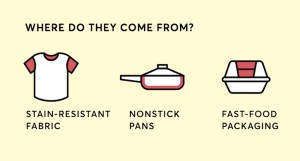
(Courtesy of Consumer Reports)
Despite the textile industry’s limited use of PFAS materials, future regulation may impact producers of performance fabrics.
By Hardy Sullivan
Given the wide array of end uses for per- and polyfluoroalkyl substances (PFAS), producers of performance fabrics, including personal protective equipment (PPE) gowns with superior blood repellency, workwear with oily stain release properties, and high-use upholstery needing resistance to oily foods and stains, might think the press’ portrayal of the textile industry misses the mark. Why focus on fabric but ignore phones?
As an end-user of PFAS materials, textiles make up only a tiny fraction of PFAS consumption. And as a percentage by weight of fabric, a little goes a long way. Yet stain-resistant fabric gets top billing as a PFAS source in consumer-facing news articles. In turn, some state regulators have targeted PFAS-containing carpet and upholstery, detracting attention from primary pollution sources — non-polymeric PFAS processing aids and PFAS-containing firefighting foam.
But textile producers have a story to tell, too. These products are safe for the consumer and require only a small amount of short-chain PFAS to impart performance, saving the environment from detrimental effects of a fast fashion, disposable goods mentality. And there are significant differences between PFAS substances; thus, one-size-fits-all regulation is unfair and not science-based.
Who will prevail in the battle for the narrative? Will other consumer products get noticed?
PFAS In The Media
A May 2021 Consumer Reports article, “How Safe is Our Drinking Water?,”1 states PFAS were detected in the drinking water of 117 out of 120 households. Two of the samples exceeded the federal advisory level of 70 parts per trillion (ppt), and 46 samples exceeded Consumer Reports’ recommended 10 ppt limit for total PFAS.
Though the Consumer Reports article states manufacturers use PFAS to make “hundreds of other common products,” a visual representation of PFAS sources published by the publication (see Figure 1) shows only three sources — stain resistant fabric, non-stick pans and fast-food packaging. A picture, is indeed, worth a thousand words — or at least hundreds in this case.
There are numerous other examples of the industry’s unwanted high profile. A recent New York Times article titled “These Everyday Toxins May Be Hurting Pregnant Women and Their Babies”2 featured the subhead “PFAS, industrial chemicals used to waterproof jackets and grease-proof fast-food containers, may disrupt pregnancy with lasting effects.” And in a podcast interview, the European Chemical Agency’s Executive Director3 cited cookware, clothing and carpet as common end-uses for PFAS.
Whoever said “There’s no such thing as bad press” wasn’t producing PFAS-containing fabric.
Response To Negative Press
The years of bad press led some companies to, publicly or privately, discontinue the use of PFAS compounds in their fiber-based products. In 2019, Home Depot announced the phase-out of PFAS in carpet.4 That same year, Gap Inc. announced it would phase out all PFC-based finishes by 2023,5 where PFC has been used to mean fluorochemicals. Even fast-fashion company H&M proudly touts its long-standing commitment to PFAS-free clothing, accessories and shoes.6 Healthcare organization Kaiser Permanente also prohibits the purchase of upholstery with fluorochemicals.7
Which Industries Utilize PFAS?
A better question to ask is what manufacturing industries do not utilize PFAS. All PFAS chemistries include strong carbon to fluorine bonds. As early as the 1940s, companies started capitalizing on fluorine’s unique properties, such as its relatively compact atomic structure and high electronegativity, or affinity for electrons. Carbon-fluorine bonds enable chemical resistance, stability in hot and cold temperatures, low surface energy, low friction, low rigidity, variable permeability, and dielectric insulation. Numerous industries developed an array of uses, some of which, given fluorine’s special place on the periodic table, may not be possible by other means. Figure 2 contains descriptions of end-uses by industry according to the American Chemistry Council.8
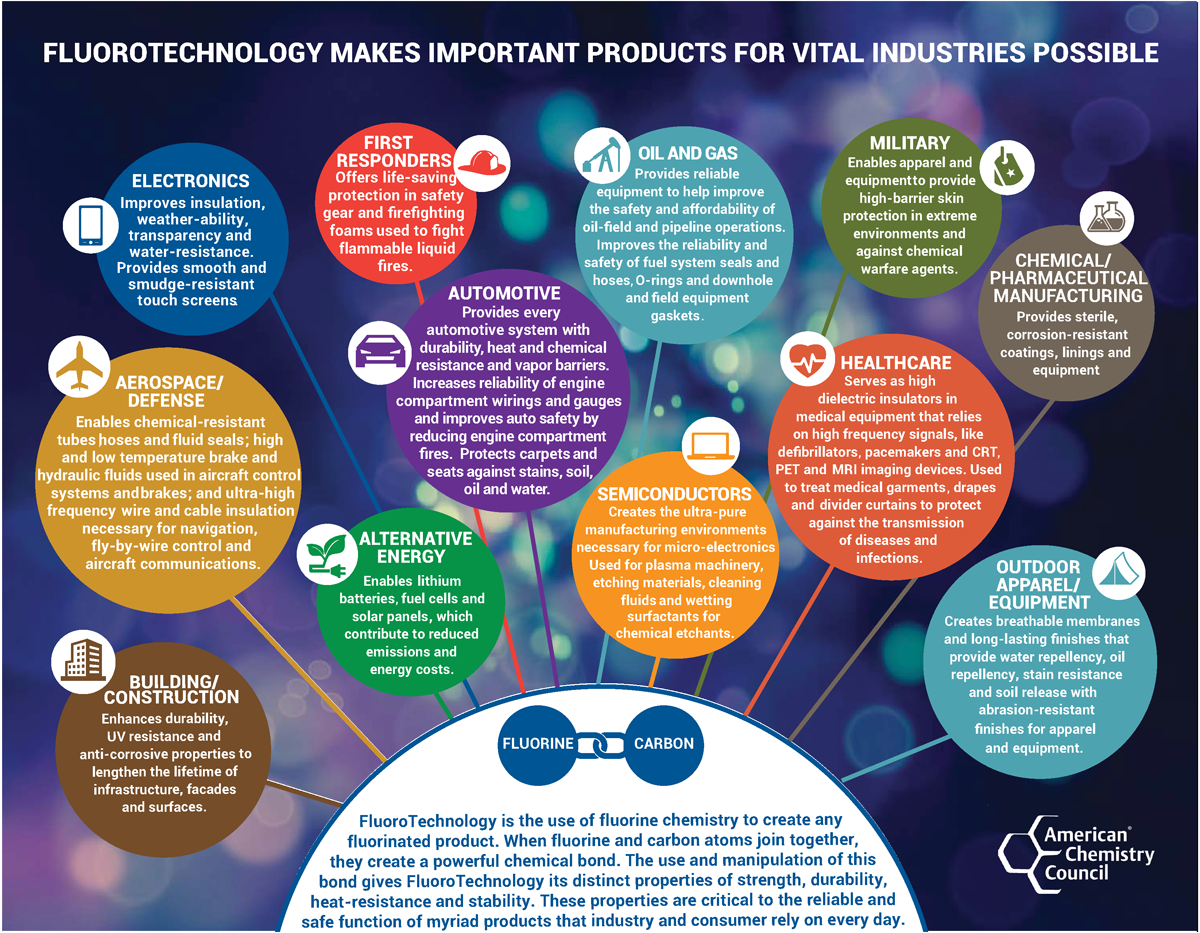
How Does PFAS Consumption In Textiles Compare To Other industries?
Putting PFAS consumption in perspective is a central issue that has gone unaddressed in press coverage. Some consumer end-uses have been reported, but PFAS consumption by industry has been absent. Everyday consumer goods containing PFAS chemistries include smart phones and tablet touchscreens, smart watch bands, dental floss, bicycle chain lubricant, and eyeglass lenses, to name a few. There are hundreds more.
A recent paper, “An overview of the uses of per- and polyfluoroalkyl substances (PFAS)”9 published by the Royal Society of Chemistry, attempted to not only identify PFAS end-uses but also characterize consumption by industry. Though the data comes from some of the Nordic countries, it provides useful insight for the United States. The take-away? While the regulation of PFAS-containing textiles might make some state regulators feel good that something is being done, the impact on the safety of drinking water will be very limited. Figure 3 shows that textiles, despite all of the attention they receive, don’t break the top 10 in terms of end-use consumption.
All of the end-uses with a dark gray background are industrial end-uses.
It is also worth noting the distinction that is drawn between polymeric and non-polymeric substances. More on this distinction later.
How Complex Is This Topic?
Fluorocarbon’s unique properties led to the creation of more than 5,000 PFAS compounds. The multitude of chemistries makes PFAS ripe for confusion. The array of designer cocktails is so large that a panel of stakeholders came together in 2011 just to establish PFAS naming guidelines.10 If it takes 29 pages to describe how to name chemistries within a class of chemicals then, chances are, there are significant differences between the chemistries.
Should PFAS Chemicals Be Treated As A Single Class?
Some groups argue all PFAS chemicals should be regulated as a single class.11 It is true that the carbon-fluorine bond is a strong one, making all PFAS materials environmentally persistent; thus, the term “forever chemicals”. It is important to distinguish, however, between environmental persistence, toxicity, and bioaccumulation. After all, sand on a beach is persistent.
While all PFAS materials are environmentally persistent, an important distinction within the PFAS class is they exist in different states — including solids, liquids, and gases. The state of matter greatly impacts mobility through air, water and soil. The liquid state, for example, of PFAS-containing firefighting foam contributes greatly to its ability to contaminate soil, as opposed to PFAS solids found on textiles.
Additionally, there are, literally, sizeable differences between polymeric and non-polymeric PFAS substances, referred to here as PFAS polymers and PFAS non-polymers (see Figure 4). A PFAS non-polymer consists of a single molecule; whereas, polymers can consist of thousands of repeating molecular units. The relatively small size of PFAS non-polymers makes them more mobile — easy to spread in air and waterways — and more bio-available — with increased potential to build up in blood and body tissues where they might do harm.
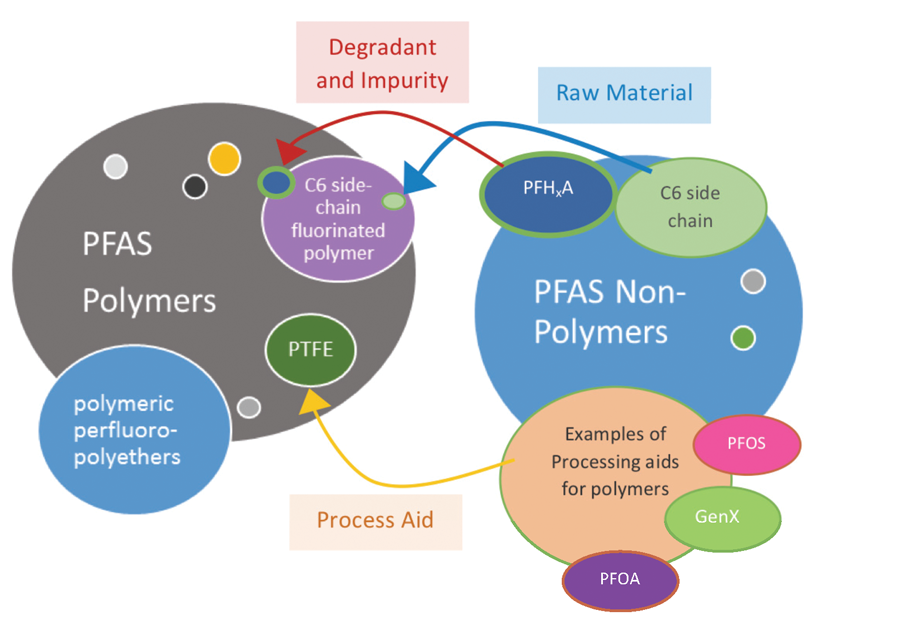
It is not as simple as PFAS polymers are good and PFAS non-polymers are bad, however, because there are varying levels of toxicity between the PFAS non-polymers. Adding to the complexity, there is an interdependence between some PFAS polymers and PFAS non-polymers.
As visualized in Figure 4, PFAS non-polymers, play one or more of the following roles:
- process aids essential for production of PFAS polymers that do not necessarily end up in PFAS polymer;
- raw material inputs for making PFAS polymers that are incorporated in the PFAS polymer;
- impurities or unintentional byproducts contained within the PFAS polymers; and/or
- degradants resulting from decomposition of PFAS polymers over long periods of time.
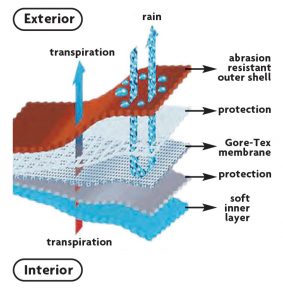
Which PFAS Chemicals Are Commonly Used In Textiles?
The primary PFAS chemicals used in textiles include polytetrafluoroethylene (PTFE) and short-chain fluorinated polymers known as C6 or C4 chemistries. Both materials are PFAS polymers. As shown in Figure 5,12 PTFE can serve as a waterproof breathable membrane, and the C6 reduces the surface energy of the uppermost layer, imparting water and oil repellency. Non-fluorinated chemistries are available as supplements or replacements to the PFAS-containing materials, but they tend to not perform as well.
Shown in Table 1 and Table 2 are non-comprehensive lists of textile-related PFAS materials.
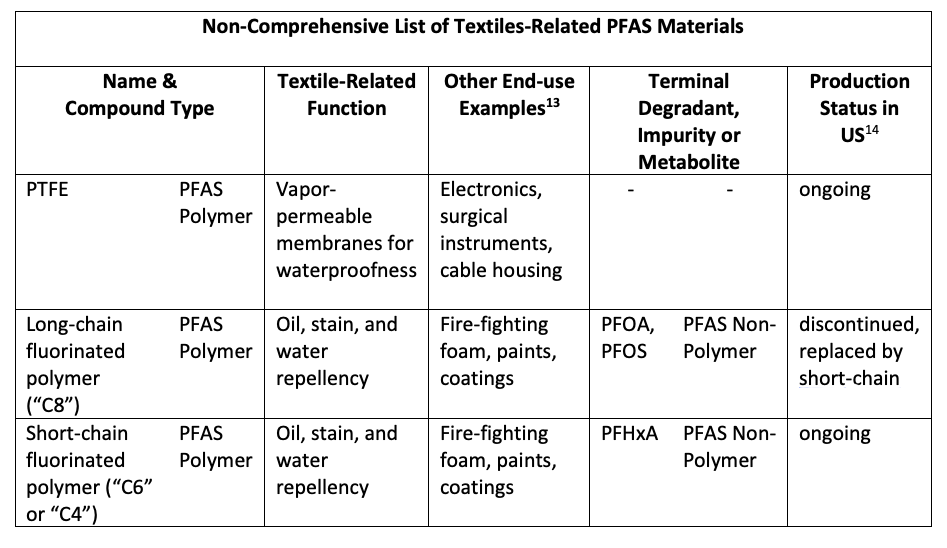
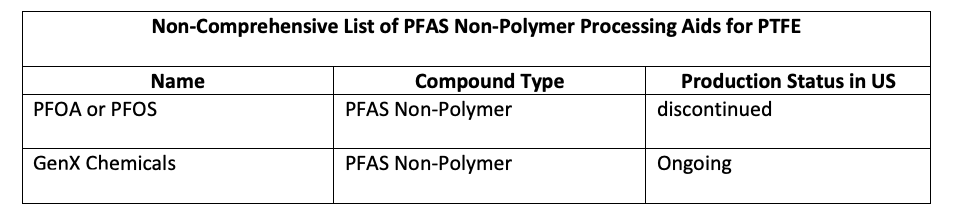
The U.S. Environmental Protection Agency (EPA) has been studying the environmental and human health profiles of PFAS chemistries since 2000. The products in production today meet the EPA’s current regulatory requirements and comply with the EPA’s PFOA [perfluorooctanoic acid] Stewardship Program. Human health and environmental impact studies are ongoing,15 and the EPA, of course, has the authority to change its requirements.
Fluoropolymers, including PTFE, the predominant type,16 are not water soluble and are not concerns for toxicity.17 Keep in mind, however, that PFAS non-polymers are required as processing aids — GenX, for example — for some fluoropolymers. While PFOA and perfluorooctanesulfonic acid (PFOS) are no longer produced in the United States, GenX is one of the replacements for PFOA and PFOS. The EPA reported GenX chemicals are less toxic than PFOA and PFOS,18 but water pollution of these non-polymer processing aids remains a concern.19
The ultimate breakdown product of short-chain fluorinated polymer continues to be studied. C6 consists of side-chains (fluorotelomers) attached to a backbone polymer, usually an acrylic or urethane. The ultimate breakdown product for C6 is perfluorohexanoic acid (PFHxA). A 2019 review of the literature indicates PFHxA is less hazardous to human health than PFOA,20 an important benchmark for the EPA.
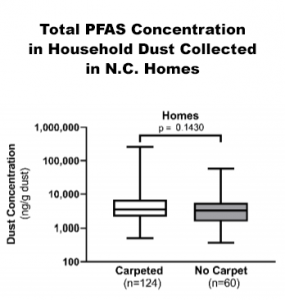
Does Carpet Cause PFAS Pollution?
Researchers are using sophisticated analytical techniques to measure PFAS levels in waterways, homes, retail stores and fire-fighting stations.
The latest scientific evidence appears to refute regulators’ emphasis on carpet. A 2020 study published by the American Chemical Society in its Environmental Science & Technology journal measured PFAS levels in dust taken from 184 homes in North Carolina.
While earlier studies draw different conclusions,21 this journal article reported there was no significant difference in PFAS levels in dust collected at homes with and without carpet.22 Additionally, no significant differences were found based on age or square footage of the houses. The article also reported a decline in PFAS content in dust samples collected over the past 20 years. Using data from earlier studies, some state regulators are targeting PFAS-treated carpeting as a non-essential end-use.
What Are The Sources Of PFAS Pollution?
According to the EPA,23 PFAS contamination is “typically localized and associated with a specific facility … an industrial facility where PFAS were produced or used to manufacture other products, or locations where firefighting foam was used such as oil refineries, airfields or other training facilities for firefighters.”
Why Is Textiles One Of The Frequently Implicated End-Uses?
The public can more easily relate to consumer goods — frying pans and raingear — than low-friction pipelines lined with PFAS materials, for example. But additional factors played a role in textiles becoming a media-spotlighted user of PFAS. Imprecise naming and guilt-by-contamination linked two well-known PFAS materials — PFOA and PFOS — to PFAS-treated Textiles.
Chemists have well-established shortcuts for naming chemical structures, but such shortcuts can lose their original meaning when used in the public domain. Such was the case in the early 2000s when the EPA referred to PFOA as C8, which was the same generic name used in the textile industry to identify the long-chain fluorinated polymers. C6 and C4 are now commonly used to describe today’s short-chain fluorinated polymers. Whether it’s C8, C6 or C4, these are just shorthand terms that do not fully explain the chemical compounds; rather, they simply indicate the number of carbon atoms linked in a series. In the case of fluorinated polymers — fluorotelomers attached to polymeric backbones — used in textiles, this nomenclature only refers to the length of the side-chain functional group; the identity of the backbone polymer is omitted entirely.
Adding to the confusion, PFOS and PFOA, were both intentionally produced processing aids for PTFE and low-level impurities of long-chain fluorinated polymers. PFOA, though not a raw material, was a low-level impurity in the long-chain fluorinated polymer manufacutured by DuPont via telomerization. PFOS was the impurity present in 3M’s long-chain fluorinated polymer produced via electrofluorination.
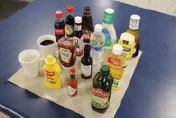
For Textiles, How Do Non-Fluorinated Repellents Compare To C6?
Shown in Figures 7a-7g is a comparison of the same polyester upholstery style with three levels of finish treatment — no treatment, non-fluorinated repellent, and C6 side-chain fluorinated repellent. Sixteen food and beverage stains were applied to the fabric, which was then photographed before cleaning, cleaned with a spot cleaner, dried, and re-photographed. As shown in the figures, untreated polyester will not repel most foodstuffs and beverages. Non-fluorinated finish provides some protection but, because its surface energy is higher than C6, it does not resist penetration of oils. The C6 finish, on the other hand, is fully able to repel a variety of food and beverages, allowing the fabric to be cleaned more easily, thoroughly, and quickly. In hospital rooms, restaurants, and homes, all of these features contribute to customer satisfaction. Such results can be achieved with fluorine making up only 0.1 percent of the fabric weight.24
Spot-cleanability of polyester upholstery25 — penetrated and residual stains — are labeled in the figures.
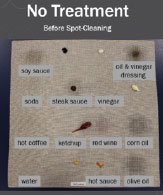
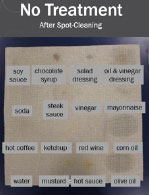
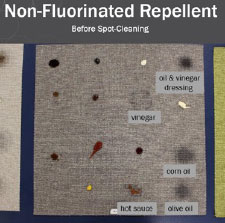
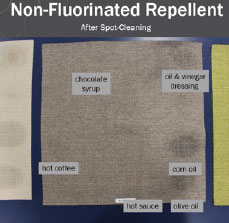
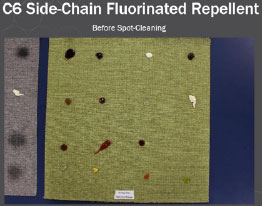
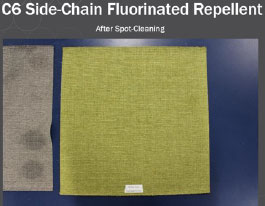
What Are The Consequences Of Removing C6 PFAS From Textiles?
Multiple surveys of U.S. designers by Interior Design magazine indicate strong demand among specifiers and end-users for surface cleanability. Cleanability is particularly important in the healthcare segment, topping the list of factors that influence fabric selection.
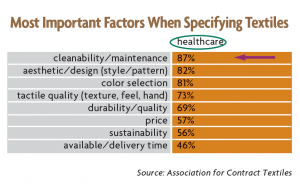
For markets where spot-cleanability is important, the absence of C6 could shorten the life of fabrics, leading to increased demand for replacements. While selling more fabric benefits producers, it is higher cost to end-users, and negatively impacts the environment because of higher use of non-renewable fuels for man-made fibers, coatings, production and transportation; increased use of pesticides for natural fibers; elevated emissions and effluent from manufacturing; increased landfill use; possibly higher microplastics pollution; and increased use of harsh solvent cleaners.
Some textile producers claim C6 finish extends the life of upholstery by years. By extending the life of commercial (non-residential) upholstery in the United States from 3 to 5 years, and not having to produce replacements as frequently, the National Council of Textile Organizations (NCTO) estimated 274k metric tons of greenhouse gas emissions is avoided, equivalent to emissions from 58 thousand passenger cars (see Figure 9). Similarly, other resources — such as water and landfills — would be proportionately impacted.
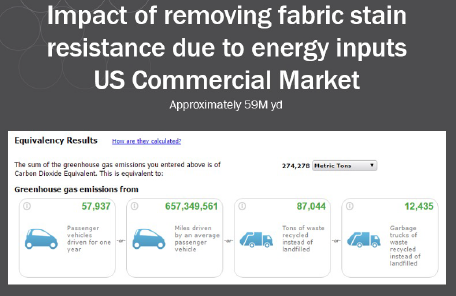
PFAS Regulation In The United States And Europe
A comprehensive list of actions being taken by the EPA is available on its website.26 Actions affecting drinking water include studying PFAS chemistries, monitoring sites, setting standards and identifying treatment options.
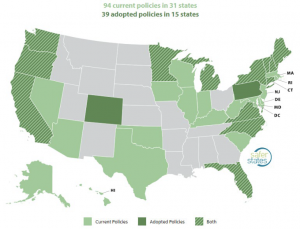
In addition, some U.S. states have proposed or enacted an array of disparate measures to prevent or constrain PFAS contamination. Safer States is an organization that tracks PFAS-related legislation and litigation.27 State-by-state legislation varies widely but includes testing water supplies for PFAS; funding for cleanups; bans for PFAS in food packaging; firefighting foam restrictions; and prohibition on the use of PFAS in consumer products, including carpet and textiles28 (See Figure 10).
The National Defense Authorization Act for Fiscal 202029 includes multiple PFAS provisions. Among others, it restricts the use of PFAS in firefighting foam; addresses clean-up of military bases polluted by firefighting foam; requires standards for monitoring PFAS; and adds some PFAS chemicals, including PFOA, PFOS and GenX chemicals, to the Toxic Release Inventory. The latter action requires applicable manufacturers to report their releases and disposals.
The FDA obtained agreements from short-chain fluorotelomer producers to phase out their PFAS products in food packaging by 2023.30 Viewed in combination with other end-uses under scrutiny, the loss of this market opportunity reduces the overall market attractiveness for short-chain fluorinated polymer producers that also supply textile finishers.
PFAS materials are also under pressure in Europe. Operating within the guidelines of the European Chemical Agency (ECHA), five Member States have proposed a ban or restriction on all PFAS materials.31 This process will take several years to unfold.
A more immediate threat to European textile producers is Germany’s proposal to restrict perfluorohexanoic acid (PFHxA) and products containing PFHxA.32 Small quantities of PFHxA are found in fabrics finished with C6; thus, C6 finish would be restricted. During the Call for Evidence, numerous comments from industry reinforced the lack of an alternative for oil repellency; the use of only minor quantities to achieve the desired property; and the wide array of non-textile end-uses that rely upon PFHxA directly or indirectly. While derogations may be allowed, such as for PPE fabrics, some textile applications are likely to be viewed as non-essential. Timing to implement restrictions is unclear.
Which PFAS end-uses are essential? Is that the right question?
The scope of PFAS regulation extends well beyond textiles. As regulators and consumer groups start to realize PFAS is essential to industries tied to national security — such as semiconductors and microchips — and renewable energy, including photovoltaics and rechargeable batteries, there has been a push, particularly in Europe and by U.S. states, to distinguish between essential and non-essential end-uses. Their goal is to eliminate non-essential end-uses.
An argument in favor of this approach is the end-use format — industrial versus consumer good — impacts product safety or risk. To be fair across industries, however, regulators would need to develop a consistent, quantifiable means for comparing risk — hazard and exposure — of hundreds of consumer products. Risk is considered a function of hazard and exposure where hazard is a material’s toxicity or corrosiveness, for example, and exposure is the extent to which the material can be ingested or come into contact with parts of the body that can be harmed.
The “What’s essential?” approach raises many questions. Who should decide whether smudge resistance of a touchscreen is more important than stain resistance of upholstery? If a grease containing PFAS is used to ensure a windmill operates more efficiently, can that grease be used to lubricate weaving loom gears? On a bicycle? What about the negative environmental implications of shortening a product’s useful life? How long would it take to formulate the criteria, answer these questions, and educate lawmakers?
In the absence of quantifiable criteria and vast resources for comparing end-uses, the subjective assignment of non-essential does not bode well for textiles. In comparison to the negligible public awareness of PFAS in electronics, stain-resistant textiles is a high-profile category, employs relatively few people, uses small quantities of PFAS, has limited political reach, and generates relatively low turnover. Compared to makers of airplanes, automobiles, and smart watches, textiles looks highly exposed and even expendable.
Meanwhile, the “What’s essential?” approach omits the consideration for actual sources of contamination and their relative impacts. What is the value of picking winners and losers if it has little impact on the problem?
What Does The Future Hold For Textiles Made Using PFAS?
Select types of PFAS — PTFE and short-chain fluorinated polymers — allow textiles to achieve levels of performance that, so far, cannot be matched without those compounds. Superior breathability, cleanability, and stain resistance all result in higher consumer satisfaction, allowing the textile products to last longer.
Despite the textile industry’s role as a minor user of PFAS, negative press coverage has dented PFAS usage in textiles. Looking ahead, the path will be difficult to navigate. Challenges include the media spotlight, environmental persistence, confusion about the chemistries, customer perception, shrinking market attractiveness for fluorotelomer producers, ongoing safety studies and regulators’ desire to target low-hanging fruit. The cards are stacked against performance textile producers and finishers.
One thing is clear: Textile companies that haven’t already launched fabrics with a non-fluorinated finish need to have a backup plan ready to go.
As for other industries using PFAS, it seems unlikely that regulators would limit the electronics industry from making semiconductors and other products that affect our global economic competitiveness, national security, and renewable energy technologies. Some PFAS uses are too big to fail.
Bottom line: PFAS contamination of waterways needs to be addressed. The main focus should be on keeping PFAS out of drinking water, as opposed to keeping it out of durable performance fabrics.
References:
2 https://www.nytimes.com/2020/09/23/parenting/pregnancy/pfas-toxins-chemicals.html
3 https://www.youtube.com/watch?v=lndgsT9tRrk&t=80s
4 https://corporate.homedepot.com/newsroom/phasing-out-products-containing-pfas
6 https://hmgroup.com/news/phasing-out-pfas/
9 https://pubs.rsc.org/en/content/articlehtml/2020/em/d0em00291g
10 https://setac.onlinelibrary.wiley.com/doi/abs/10.1002/ieam.258
11 https://factor.niehs.nih.gov/2020/8/papers/pfas/index.htm
13 https://www.americanchemistry.com/PFAS/Fluorotechnology-Facts.html
16 https://ihsmarkit.com/products/fluoropolymers-chemical-economics-handbook.html
17 https://www.americanchemistry.com/PFAS/Fluorotechnology-Facts.html
19 https://cen.acs.org/environment/persistent-pollutants/hunt-GenX-chemicals-people/97/i14
21 https://www.sciencedirect.com/science/article/pii/S016041201630215X?via%3Dihub
22 https://pubs.acs.org/doi/pdf/10.1021/acs.est.0c04869
23 https://www.epa.gov/sites/production/files/2018-03/documents/pfasv15_2pg_0.pdf
24 https://www.crypton.com/crypton-eco-fabric/
25 National Council of Textile Organizations (NCTO)
26 https://www.epa.gov/pfas/epa-actions-address-pfas
27 https://www.saferstates.org/toxic-chemicals/pfas/
29 https://www.congress.gov/bill/116th-congress/house-bill/2500/text
30 https://chemicalwatch.com/140955/manufacturers-agree-to-phase-out-type-of-pfas-in-food-packaging
31 https://www.rivm.nl/en/pfas/pfas-restriction-proposal
32 https://echa.europa.eu/registry-of-restriction-intentions/-/dislist/details/0b0236e18323a25d
Editor’s Note: Hardy Sullivan is a sales representative for Thies Corp., a Germany-based producer of dyeing machines and dispensing systems. Prior to Thies, Sullivan developed performance fabrics and finishes for commercial, residential and automotive end-uses. He has an M.S. in Textile Technology from the Institute of Textile Technology, and a B.S. in Textile Management from North Carolina State University’s Wilson College of Textiles.
May/June 2021