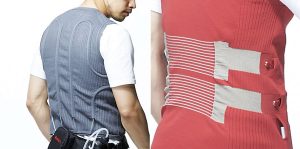
Upgrades, automation and technology integration were just some of the advances in the knitting arena at ITMA 2019.
By Dr. Andre West, Technical Editor
ITMA 2019 was not as groundbreaking for knitting equipment as past years where there were new machines at every booth. This ITMA, however, was more focused on upgrades, add-ons, partnerships, technology integration, automation, sustainability and digital 3D integration. So even though it was not a show full of groundbreaking machine developments, ITMA 2019 was full of ideas and positivity on how the knitting industry is moving forward and how collaborations are formed. This article looks at different knitting machine configurations, which from the author’s perspective are worth reflecting on; flat knitting, circular knitting for body-mapped garments, knitted shoes and warp knitting, with an emphasis on this year’s ITMA innovations presented by each company and is not in any way a recommendation or a comparative study.
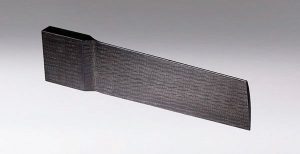
Flat Knitting
Japan-based Shima Seiki Mfg. Ltd. unveiled its “KNITify the World — Smart Solutions in Textiles” theme during ITMA, which illustrated the flexibility of Shima Seiki products to cater to various industry sectors in addition to the traditional customer base in the apparel industry. Its approach was to propose knitting as an alternative manufacturing solution for non-fashion related industries.
Knits have inherent stretch and compression characteristics, which can be utilized in a variety of industries. New knitting techniques, such as inlay, are made possible with special loop pressers featured on Shima Seiki’s updated N.SVR-SP series machine adding further value to knitting and has gained particular attention for its ability to produce hybrid knit-weave fabrics that allow insertion of technical yarns — including carbon fiber, monofilament and even metallic conductive yarns — previously considered incompatible with knit constructions.
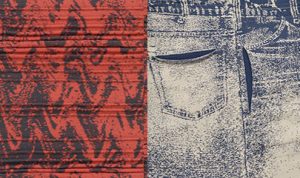
One of the other add-ons paired with Shima Seiki machines is a Yarn Unwinding Device for spools of technical yarn to ease yarn feeding for such difficult-to-handle materials. This technology makes it possible for knitted technology to enter markets that previously were off limits, such as sport accessories, shoes, and wearable and industrial applications for medical automotive and aeronautical industries. In addition, the new I-Plating option can alternate yarn colors in any pattern, producing jacquard-like designs using a plain jersey stitch. This I-Plating technique can be performed within the same course and for individual needles.
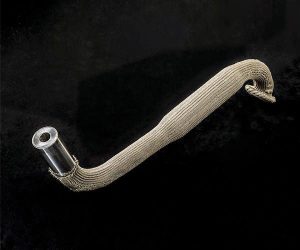
Shima Seiki WHOLEGARMENT® knitting machines moved forward slightly with some add-ons for shaped knitting, expanding that potential to three dimensions. WholeGarment knitting is capable of producing knitted items in their entirety on the machine and allows 3D preforms and tubing to be produced without sewing. Elimination of sewing allows for faster turnaround and high potential for on-demand knitting. The seam-free nature also ensures continuity of the fabric, allowing functional yarns such as those made from conductive fibers to wrap around the entire body without interruption for applications in smart garments and wearable technology. Three-dimensional knitting provides fit, comfort, lightness, and mobility — the key factors that make seam-free so attractive. Three WholeGarment machines were on display, including the new MACH2VS machine making its debut at ITMA, which is a two-bed half gauge machine.
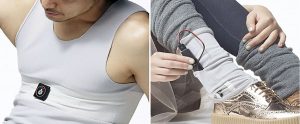
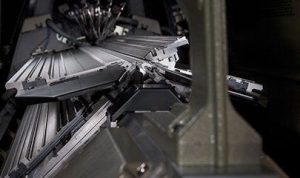
The benefits of WholeGarment knitting was further showcased in its ultimate form in the MADE2FIT area of the Shima Seiki booth, where the company was demonstrating mass-customization. The concept begins by scanning a body using a smartphone app, then sending that data to a server that automatically adjusts preloaded data categories including size, length, sleeve length and color, and then knits the garment on the MACH2XS103 WholeGarment knitting machine.
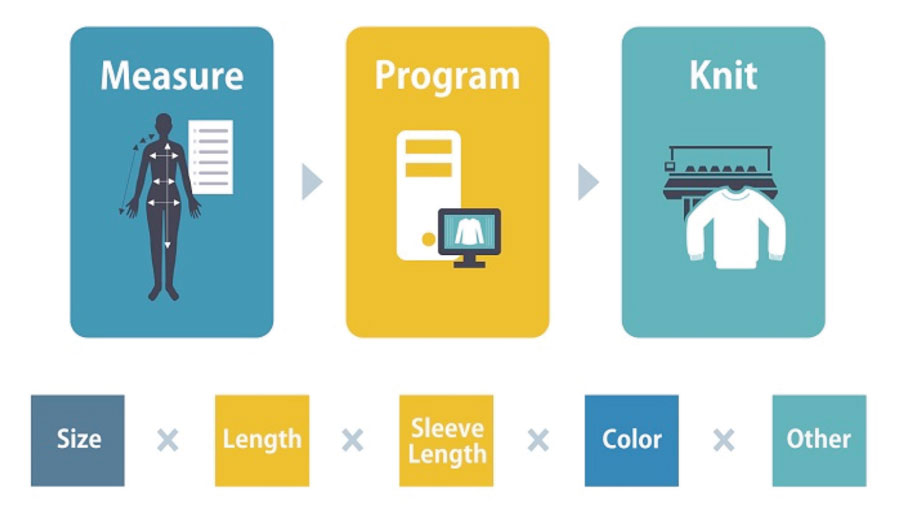
Yarnbank by Shima Seiki is a most exciting idea seen at ITMA. It is a first-of-its-kind free-of-charge website for searching and downloading digital yarn data that can be used for virtual sampling on the SDS-ONE APEX series 3D design system. Downloading yarn data reduces the need for scanning yarns manually and improves the accuracy of simulations and efficiency of product planning. Yarnbank allows the entire supply chain from yarn companies and apparel companies to knit manufacturers to connect digitally. Yarnbank also provides a brand-new channel for sales promotion for yarn companies. At ITMA, Shima Seiki displayed digital yarn collections from Yarns & Colors, iafil, Toyoboshi, Tollegno 1900, Hasegawa, UPW, Xinno, Recover, Regal, Xinao, and Novetex.
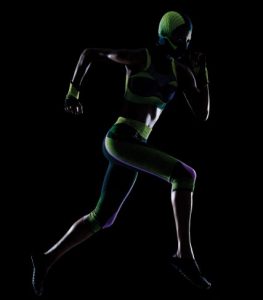
Germany-based H. Stoll AG & Co. KG introduced its new knitelligence machine generation at ITMA 2019, which is tailored to the specific needs of the digital world, facilitating work through process automation, more transparency, shorter response times, shorter production cycles and higher productivity.
Covering fabrics and upholstery material can be knitted with woven optics and structure effects. Transparent mesh structures provide breathability. Surfaces can be designed with arbitrary combinations of structures to integrate functional and design requirements in one knitting process.
The most futuristic of knitting and wearables was shown undercover. Stoll-knitrobotic visitors had the opportunity to take a picture of themselves or create a graphic within the Adobe® Photoshop® plugin STOLL-artwork® to interact with Stoll technology first-hand. As a key feature during the showcase, a plastic stripe was inserted within a fabric during the knitting process. Without manual intervention, the STOLL-knitrobotic® gripping arm removed this strip from a magazine integrated into the machine and inserted it precisely between the needle beds.
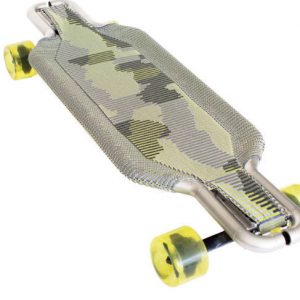
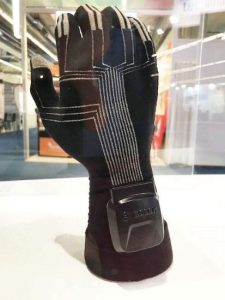
Another application on display was a knitted sensor glove developed in cooperation with Germany-based BOSCH GmbH. The glove was made using conductive yarns to provide sensory and control functions on all fingers. This design gives wearers the ability to interface with machines, control movement in augmented and virtual reality applications, and gain rehabilitative healthcare capabilities.
Italy-based Stoll Italia also presented a new app solution for knit-and-wear — developed in cooperation with Fision — which makes it possible to scan visitors and transfer their body measurements into Stoll’s M1plus® pattern software to develop a ready-to-knit, customized garment.
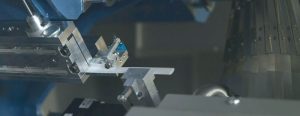
Stoll’s machine with all the features is the ADF 830-24 ki W knit&wear, which offers even greater flexibility in coloring and patterning and improved productivity. The key features include reverse plating, Ikat plating, selective plating and intarsia plating. In addition to weft insertion, which gives fabrics a woven like appearance, the ADF 830-24 ki W knit&wear also offers intarsia technique within the knit&wear range.
Textile Computing™ is a collaborative company between Ontario-based Myant Inc. and Stoll. The goal is to bring knitted sensors and actuators into everyday textiles, giving them the ability to sense and react to the human body. This continuous bidirectional interface to the human operating system will empower humanity to transform its capabilities and performance, help people proactively manage health and deliver treatment, and allow people to build better connections with themselves and people around them.
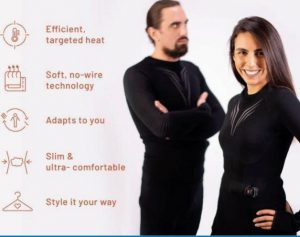
TT e-text is the newest cluster of technical textiles created by Stoll and Myant. TT e-tex represents the new industry of Textile Computing, textile products embedded with technologies that sense, activate, and adapt while generating and transmitting unique insights and personalized feedback. Textile Computing is the foundation that will ensure the company stays competitive throughout the Industry 4.0 future.
Taiwan-based Pailung Machinery Mill Co. Ltd. is known primarily for its circular knitting machinery but is also a manufacturer of flat machines. One of its latest flat machines is the specialized flat spacer machine ISP203. Spacer fabrics have played a revolutionary role in the fabric industry in recent years, and this machine is capable of creating sculpted spacer fabrics. The ISP203 can knit a single piece of spacer fabric with various thicknesses, offering an alternative fabric style for padded bras and other apparel.
Circular Knitting
Vanguard PaiLung — based in Monroe, N.C., and a division of Pailung Machinery Mill — is one of the largest circular knitting machine manufacturers in the world and the only remaining creator of large-diameter circular knitting machines in North America. The company specializes in body-size knitting with more than 10,000 machines installed at knitting companies around the world, especially in Central America. Managing the data and production from these machines is cumbersome, time consuming and prone to error. All new at ITMA 2019 was its MES — Manufacturing Execution System — a knit monitoring system (KMS) built to schedule, monitor and manage a knitting room. At the office or on the go, the KMS can be accessed from anywhere, giving complete control of the knitting plant no matter where the operator is located. The system even alerts an operator when parts need to be replaced.
Other new Vanguard Pailung developments include the KDFPS-HW Knitted 3-Layer High Pile machine and the KRTDC J6 Segue Jacquard machine.
As the name suggests, the KDFPS-HW knitted 3-layer high-pile technology simultaneously knits three layers on a single machine, completely avoiding the laborious process of producing the laminated 3-layer high pile, which reduces production time by 60 percent, according to the company. At the same time, Vanguard Pailung reports the KDFPS-HW solves the 2-layer high-pile loss issue, both accelerating production and improving fabric quality.
Equipped with state-of-the-art technology that releases yarn as needed, rather than all at once, the KRTDCJ6 can knit up to eight different types of yarn in varying colors, materials, and denier values, without thickening the knit. The Segue Jacquard knits vibrant patterns that last longer than printed designs and can create knits with embossed patterns.
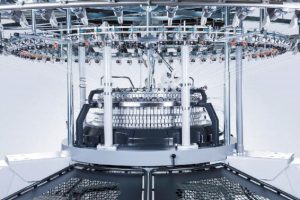
Germany-based Mayer & Cie. GmbH & Co. KG exhibited five machines, four of which focused on producing sport fabrics. The MJ 3.2 E is an electronic single jersey machine that specializes in mesh and body mapping structures. The new flagship machine is based on a 3-in-1 body mapping structured mesh — a net-like hole pattern — which is in demand in the sporting market segment and for athleisurewear and is currently a key growth driver for circular knits. A finer basic thread, usually a monofilament yarn, is responsible for the hole structure, while the thicker plating thread — cotton, for example — provides the requisite thick areas. Mesh structures require one-sided plating, and the basic thread is invisible in the finished fabric. Mesh can serve as both a fashion and a functional element, by ensuring ventilation of selected body areas for example. Body mapping takes the different perspiration areas of the human body into account, but double-sided plating creates the patterns. Furthermore, body mapping structures almost without exception require elastomeric plating.
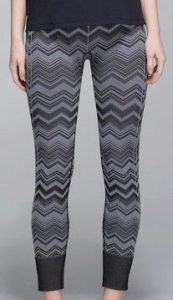
Italy-based Santoni S.p.A., an Italian leader in the production of sock and pantyhose machines and part of the Lonati Group, celebrated its 100th anniversary at the show. Santoni’s seamless technology, especially the TOP2 series of machines, are in a class of their own. There has been significant advancement in circular knitting and it has proven to be ideally suited for nylon yarns because of available variants such as filament fineness, luster and filament shape, together with their high stretch and recovery. Santoni’s technology is based on knitting tubular fabrics without seams and can apply different knit stitches to incorporate preshaped structures, which limits costs including labor, waste, fabric stocks, and energy — things associated with the alternative cut-and-sew manufacturing method. Santoni’s high-productivity eight feed single jersey electronic circular knitting machine with two needle-by-needle selections on each feed with 3 technical ways — configuration with 16 actuators — offers the possibility to knit floated plating design and inlaid elastic yarn. The patented Santoni system enables the knitting of 8 feed patterns with high definition and extremely sharp color. The machine allows the production of underwear, outwear, sportswear, swimwear and medical items.
In a corner of the Santoni booth at ITMA 2019, a SM8-TOP2V seamless machine was matched with Santoni’s new automatic finishing machine for boxers to create a unique Boxer Process Station. This cut-and-sew machine applies a gusset into each boxer with a four-needle sewing head, completing the whole process automatically and offering the finished boxer ready for the final packing stage.
Knitted Shoes
A little history of the knitted shoe industry is needed to better understand recent developments. Before the previous ITMA in Milan, Italy, in 2015, knit shoes was a fledging industry on the brink of exploding. The knitted portion is the upper of the shoe, which is manufactured using a highly technical knitting machine. The two major players in knitted footwear — brands Nike and Adidas — had fought over intellectual property since 2012. Shortly after Adidas unveiled its Primeknit, Nike filed a patent infringement claim. Nike failed to meet its burden of establishing patentability of the proposed substitute claims on February 11, 2016, according to a Foley & Larder LLP blog post.
This has all happened since the 2015 ITMA in Milan opening up the floodgates for development. The market for shoes with knitted uppers is projected to reach $3.19 billion by 2025 at 5.9 percent compounded annual growth rate (AMR).
Knit shoes were seen all over the knitting hall at ITMA 2019. In just three years, flat computerized machine, circular machine, warp knit machine, and the most newsworthy, the traditional sock machine manufacturers now have the technology to produce sock/shoe combinations turning the whole market on its head.
These shoes provide sock-like comfort and maintain a trendy, yet athletic, look. The shoe with a knitted upper has become increasingly popular among the younger generation owing to the high-level influence of sports. The knitted upper shoe requires little to no manual labor during manufacturing; the only labor required is to attach the knitted part to the shoe. This allows footwear manufacturers to move production closer to their larger markets, reducing or possibly eliminating the costs of shipping and tariffs. Circular-knitted shoe uppers for sports and leisure footwear have been an option since 2012 when they debuted at the Olympic Games. Since then, fabric shoe uppers have mostly been flat-knitted, with circular knitting and warp knitting running neck-and-neck a fair distance behind.
When the three techniques are compared, however, circular knitting leads the field for productivity. In addition, setup times are shorter, with the result that smaller batches can be manufactured profitably. Then there are the sock manufacturers that had the technology, but not the know-how, of how to turn a sock into a shoe upper.
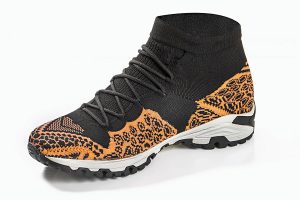
Cesare Colosio S.r.l. is a circular knitting machinery manufacturer based in Italy. In 2015, after 60 years of experience in intarsia knitting, the company developed the first circular intarsia machine ever patented for the production of knitted, seamless shoe uppers. The S1+, is a machine that has been acknowledged by the most important international shoe brands with more than 600 machines installed since 2016. According to Colosio, the S1+ machine is not only “100-percent sustainable,” allowing the elimination of waste of material throughout the whole manufacturing process, but it is also extremely versatile. The machine produces uppers for multiple applications, from technical and sports footwear, to casual and fashion shoes. Additionally, with an average production capacity per machine of four pairs of uppers per hour, manufacturers can minimize industrial costs and times. The S1+ can create seamless uppers made using different and independent yarns and, as a consequence, different and independent areas depending on the final result that the producer wants to achieve.
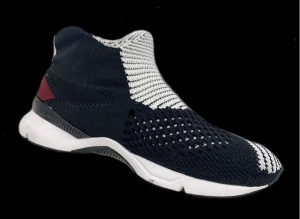
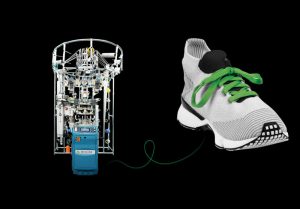
In a similar vein, is Santoni’s new, patented XT machine with ingenious intarsia technology for efficient production of shoe uppers. Single-cylinder intarsia electronic knitting machine with four reciprocating feeds and two selection points — three technical ways — per feed and per rotating sense for the production of intarsia products with breathable mesh areas with cushioning and/or transfer stitch areas knitted in sculpted terry.
The machine knitting head is equipped with cams, as well as a special-patented chain linking system, which allows only preselected needles to be driven to the stitch cam for knitting.
Santoni has applied for a series of new machine patents in order to be able to knit 4-feed high-definition colored logo patterns as well as 3D patterns on the same course as intarsia, sculpted terry and transfer stitch areas.
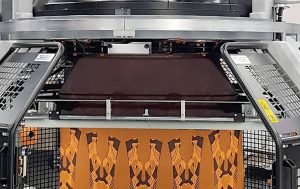
Nearly all the large circular knit companies now have large circular jacquard machines, such as Mayer & Cie.’s OVJA 1.1 EETT machine, to compete with the traditional Santoni Mec-Mor, which in various forms has been around for years but is now focused on shoe upper fabric production. These machines combine double jacquard selection on the cylinder and dial electronics and bidirectional transfer selection, and can knit an almost infinite variety of patterns, including hole structures according to the companies.
Spin Knit
Last but not least on the weft knitting sphere is the spin knit revolution, which allows knitting to happen directly from either roving or sliver instead of a yarn package. Mayer & Cie., Germany-based Terrot GmbH and Pailung Machinery Mill offered different variations of this technology at ITMA 2015. Although these machines were focal points at the booths, there does not seem to be much movement in the adoption direction.
However, one established machine with new features is Mayer & Cie’s Spinit 3.0 E. The machine now also processes polyester, is capable of a higher working speed and is linked to the Knitlink digital platform making the combined spinning and knitting machine a more attractive proposition. The 3-in-1 Spinit systems concept of combining three processes — spinning, knitting and cleaning — in one machine and thereby saving time, space and energy, has earned Mayer & Cie. several awards, most recently in 2017 when it was awarded the IKU Innovation Prize for the Climate and the Environment, awarded in alternate years by the Federal Environment Ministry (BMUB) and the Federation of German Industry (BDI). Visitors to ITMA 2019 observed the new “Enhanced Performance” Spinit 3.0 E.
Spin knit fabrics can now be designed with thick and thin yarns including Ikat designs allowing the machinery to offer design features rather than just cost savings. There may be hope for this technology if the sportswear brands see its potential.
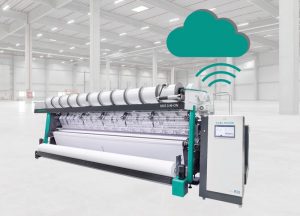
Warp Knitting
One of the major problems with warp knitting, is the number of mechanical changes that need to take place on the machine in order to run a new pattern. Germany-based Karl Mayer Textilmaschinenfabrik GmbH offers a new model that is changed on-line. Its HKS 3-M-ON is the first three-bar HKS model with electronic guide bar control, which allows for immediate pattern changes without any mechanical modification and no delay in production. The operator only needs to download the required information from a secured cloud to the machine and a new fabric design can be immediately produced. In times of rapidly changing market requirements, it is an asset to be able to react quickly to such demands and be able to access a library of designs, where making previously short runs was impossible.
Karl Mayer also introduced has a new generation of warp knit fabric technology. The double needle bar technology is opening a new chapter by offering, besides the usual 3D spacer fabrics, new 4D-KNIT.SOLUTIONS produced on its RDPJ 6/2 EL.
This ingenious bar arrangement and technical configuration, combined with Karl Mayer’s established high-quality piezo-jacquard technology, enables this double needle bar machine to open up a new dimension producing fabrics with diverse malleable patterning on both fabric sides. The 3D motifs can be completely variable in shape, positioning and height. Small and flat reliefs, or deep and bulky forms with cushioning, are possible. Further, the design can contain freely placed holes, for even more possibilities. The openings can be used for directed air flow or lighting effects.
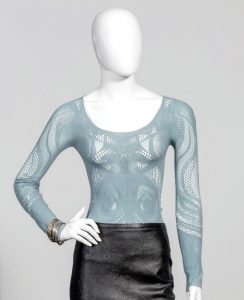
Knitted body mapping for warp knit is the future. Rascheltronic®, Karl Mayer’s RSJ line, is a series of high-speed jacquard raschel machines for producing jacquard-patterned, stretch and non-stretch fabrics. These high-speed jacquard raschel machines incorporate jacquard patterning that enables a virtually unlimited range of designs to be worked using an electronic guide bar. The computer controls permit rapid lapping changes and long-repeats on pre-made-up fabrics, and also enables functional zones to be incorporated in the fabric.
These machines are capturing the market. Innovative, warp-knitted, seamless components can be produced in a single sequence, without any seams, for the toes, fingers and even the head. They can be used in functional sportswear, underwear, hosiery and fashionable outerwear.
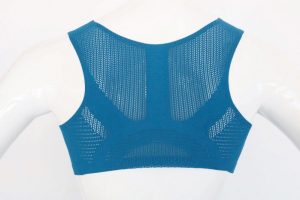
Fashion Is A Driver For The Future
The knitting industry has come a long way in the last four years with shoes and wearables leading the charge. Robotics and artificial intelligence are finally on the way and it is yet to be seen how these technologies will be integrated fully into a garment let alone the human body. However, expect there to be a lot more trial and error over the next four years as some of these companies try to navigate this integration. What seems apparent is that this technology integration is haphazard at best and just because the technology is there, it does not always make it to the marketplace. In the meantime, fashion is still going to lead the way, so whatever is new and exciting in an aesthetic sense may have a greater chance to move technology forward. The big iconic brands need to play their part to support the technology as long as the design and technology are twinned.
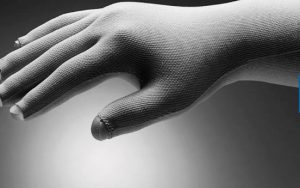
May/June 2020