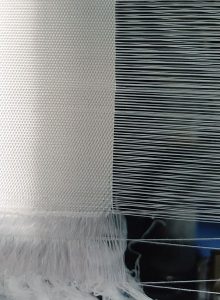
A recent NCSU Senior Design project paired a team of students with Patagonia to develop a new woven fabric for the fly fishing wader market.
By Jesse Noble
All students pursuing a degree in Textile Engineering or Textile Technology within the College of Textiles at North Carolina State University (NCSU) pass through the rigors of Senior Design before graduation. This is a year-long program structured as a two-semester course sequence that encompasses a project sponsored by an industrial company or government agency looking to improve a product, process or test method. This is a team project that typically includes three to four members with topics that range dramatically within the textile industry.
During the 2015-16 academic year, one team embarked on a journey to research, prototype and create a new woven layer for the fly fishing wader market sponsored by Patagonia Inc., Ventura, Calif. The team also developed a fabric testing method that better simulates field conditions for fly fishing waders. The project began with the following definition:
“Currently, fabrics used in submersion and wading products are not only stiff, dense and heavy, but they also have poor breathability, causing discomfort for the wearer. Throughout the lifetime of these types of products, they tend to fail due to the separation of layers, ultimately caused by bonds becoming weak between layers. Three other main areas of failure are the attachment of booties, seams failing and the occurrence of punctures. The primary goal of this project is to create a test method for fabrics that will determine whether the fabric will stay waterproof through use. The development of a prototype fabric will follow benchmarking current innovative technology as well as Patagonia’s given resources. Supplementary goals include testing how durable the fabric is to surface wear, puncture resistance, interlayer adhesion, and, if used, the fabrics resistance to hydrolysis of any coating or adhesives on the fabric. This prototype fabric will be developed with Patagonia’s mission statement of ‘Build the best product, cause no unnecessary harm, and use business to inspire and implement solutions to the environmental crisis’ in mind.”
Getting Started
The first thing the team had to understand was how a puncture happens in a fabric. To start, the students researched similar products that stop punctures such as dog bite sleeves and bulletproof vests. As the team gained knowledge of these products, they understood the mechanisms responsible for resisting a puncture. The students also began to notice a common layering approach in the construction to prevent punctures. As such, they were hesitant to use the traditional five-layer construction found in a typical wader: knit fabric on the inner layer; waterproof membrane; woven layer; waterproof membrane; and a final woven layer on the outer surface. The team began exploring how the effect of more layers or altogether new woven layer constructions could be used to provide improved puncture resistance without adding weight to the waders. At the same time, they also were conducting research on the test methods relevant to the project.
Ideation
The next phase of the project was ideation, where the team generated actual concepts for the solutions they envisioned during the research. This included combinations of out-of-the-box ideas as well as more practical ideas. As the scope began to narrow, the team explored new or creative ways to change the weave construction, yarn construction and fiber materials. The students also did not forget about the other phase of the project — to develop a more suitable puncture test method. Here the ideation focused on how a strategy for simulating a realistic wader puncture could be developed. By rating all of the ideas based on the criteria established early on in the project, the team was able to narrow its focus to a specific woven fabric construction and a new test method that could be used to accurately analyze puncture.
Prototyping
To develop the new woven fabric, the students worked extensively with the Springs Weaving Laboratory at NCSU’s College of Textiles run by the Zeis Textiles Extension program. Luckily the lab was right next door to the Senior Design lab and the team was able to work closely with the lab manager, William Barefoot, to create 20-inch by 72-inch samples of the woven construction for testing and proof of concept (See Figure 1).
In order to examine the design concept, the team defined a Design of Experiment for the woven fabric with construction and denier as the two variables. After the first round of prototyping was complete, the students were able to reflect and improve and foresee any implications with the sample weaving process and the construction design. In the second prototype, the team was able to weave exactly what it wanted, resulting in huge gains in the material properties with only a small addition of weight.
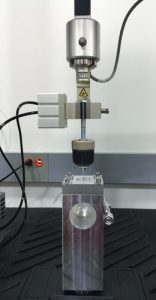
Testing
In parallel to the prototyping, the team constructed and modified the testing design. Using the machine shop in the College of Textiles, the students built a custom apparatus that enabled the fabric to be held in a consistent way while being punctured (See Figure 2). They further conducted a statistical analysis to validate this testing strategy. The biggest impact of this newly developed test method is that it enables textile engineers to observe how lighter fabrics with fewer layers, lower denier and a specific weave design will respond to multiple types of puncture.
After creating the new test method, the team tested each prototype for puncture resistance, tear strength and abrasion. After discussing the results with the sponsor and using information from research and field testing, the students believed the test method produced an appropriate evaluation of the fabric prototype’s durability out in the field.
Results
While the team cannot share the specific weave design of the fabric developed, they report they managed with the new design to demonstrate significant improvement in the puncture resistance. One design demonstrated that with only a 7-percent increase in weight, puncture resistance increased by more than 70 percent when compared to the heavyweight benchmark product. Another prototype design decreased the weight by nearly 6 percent compared to the heavyweight control, while increasing puncture resistance by more than 60 percent.
After reviewing the data along with the strengths and weaknesses of each prototype, the students suggested to Patagonia several paths forward in fabric design.
Overall, the team created two woven fabrics that, according to a literature review, had not previously been fabricated. Moreover, the strategic use of the engineering design process allowed the students to show how these designs outperform the current standard woven fabrics that are used in waders through only minimal additions to cost and/or weight. Finally, the team created a new test method to give textile engineers a better idea of how fabrics will behave in the field — or stream, as the case may be.
For more information on this project, please contact the Patagonia sponsor: Matt Dwyer, Matt.Dwyer@patagonia. com; and Ben Galphin, Ben.Galphin@ patagonia.com. For more information on the NCSU Senior Design Capstone Program, please contact the program directors: Jesse S. Jur, jsjur@ncsu.edu; and Russell E. Gorga, regorga@ncsu.edu.
Editor’s note: Jesse Noble is a 2016 North Carolina State University (NCSU) graduate in Textile Engineering and was a member of the team that created the new fly fishing wader fabric.
March/April 2017