After some problems, not unlike many other textile machinery suppliers, the Italy-based weaving
machinery manufacturer itema S.p.A. has recovered. The owner of the famous brand names Sultex,
Vamatex and Somet has presented a new rapier machine, which already is enjoying some commercial
success around the globe.
Some weeks ago, itema held an open house to present its new R9500 rapier weaving machine. CEO
Carlo Rogora started his presentation by saying: “Today, itema is one brand and one name. In the
past two years, we did our homework. All the labels are now under one umbrella: ‘itema.'”
The company has been restructured, and the personnel count in Italy and Switzerland was
reduced from 1,200 people in 2009 to 825 in 2012. On top of that, Rogora mentioned, itema today is
absolutely free of debt. Frankly speaking, this is quite a remarkable feat for a textile machinery
company these days.
After the response to the ITMA Barcelona debut and the immediate market success of the
air-jet A9500 weaving machine, the concept of the R9500 was obvious: the company is taking
advantage of a Common Base Platform (CBP) and integrating the successful features of its rapier
machines. The R9500 is based on the A9500’s footprint and mechanical concept, and also makes
efficient use of comparable parts and solutions.
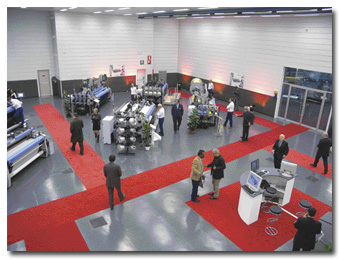
itema recently held an open house at its showroom in Colzate, Italy, to introduce the new R9500
rapier weaving machine.
Versatility
The versatile R9500 should enable weavers to enter new markets. Users have the flexibility to
select various options and features, which enables a broad application range. The machine’s
appearance is solid and robust: It can weave very heavy fabrics, but it is flexible and precise
enough to weave fine, fancy and technical yarns.
The SK Transfer System is designed to provide high speed and versatility, while the new Free
Positive Approach (FPA) weft transfer provides a race board without guiding elements for use with
man-made or delicate yarns.
The New Common Electronic Platform features a simple but comprehensive design and allows all
technical parameters to be easily controlled. More than 75 percent of all key components are said
to be Italian-made. More than 90 percent of all parts – including motors, electric devices and
interface – are used on both the rapier and the air-jet machine A9500, which lowers costs for
customers that have both technologies.
Sturdy Frame
The R9500’s heavy-duty frames provide a low vibration pattern even at high speeds. The solid
drives, positioned in main lateral frames, are said to be engineered for extensive control of
moving masses to consistently process heavy patterns or unbalanced styles with minimal cost and
maintenance. The redesigned sley and back rest modules represent key developments. The new sley
design promotes speed and versatility, while the new back rest module enables reduced warp tension
and a cleaner shed break. Maximum floor space utilization provides low power consumption and a
minimal noise profile.
Easy Style Change
The R9500’s design should reduce downtime for style changes by eliminating time-consuming
maintenance and settings. Quick beam release is standard, and DRC10 connections eliminate the need
for leveling. The number of machine covers has been reduced, allowing quick access for machine
cleaning and maintenance, resulting in reduced heat in the workshop.
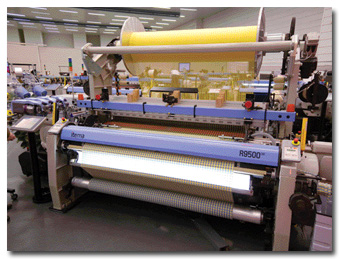
itema’s new R9500 rapier machine is based on the A9500 air-jet machine’s footprint and
mechanical concept.
Weft Insertion System
The machine’s new shed geometry is the result of the need to reduce the shed to maximize
speed and to use rapiers with diverse capabilities. Further features are the positioning of the
first frame closer to the reed. This allows a shortened stroke, which enables higher speeds and
longer life cycles for heddles and harness frames. Furthermore, the beating stroke has been
increased to ensure the highest beating force and the capacity to weave heavy fabrics.
Rapier Drive System
The Turbo Prop propeller drive system has been completely redesigned for the R9500. The drive
is still compact and has minimal moving parts, providing reliability and reducing maintenance. The
drive design also features a secured mechanism in the side frame to ensure stability and precision,
as well as new carriage and swinging sliders made using aeronautical-grade alloys. In addition, the
new Turbo Prop settings do not shift over time, eliminating the need for maintenance personnel to
continually reset and adjust them.
Additional Equipment
There is a wide range of options for selvage formation. Standard cutters, a melting device,
and mechanical and air tuckers can be installed. Electronic weft tensioning can be specified. The
tensioner can be programmed through the user interface, and it features a self-cleaning system to
prevent dust accumulation. The R9500 weft control system enables each weft to be processed
digitally by the NCP Processor. Sensitivity adjustments are determined according to each individual
position.
The R9500 is equipped with a new electronic platform in which the full-color touch screen is
the user interface. The software is intuitive and encourages dialogue with the weaver. By accessing
the touch screen, the weaver may select a functionality test for any device or application on the
machine, including circuit boards. The optional Intelligent Production Optimizing System (IPOS) is
designed to optimize machine productivity by monitoring machine speed and stop level.
The Vision
Rogora mentioned that itema is still the only supplier to provide all weft insertion systems
– air-jet, rapier and projectile technology. After some industrial trials in pilot mills, the R9500
is already having some success. The Quality, Reliability and Performance (QRP) certification with a
two-year guarantee reflects itema’s commitment to quality through the consistent application of
enhanced processes to design, develop and manufacture.
January/February 2013