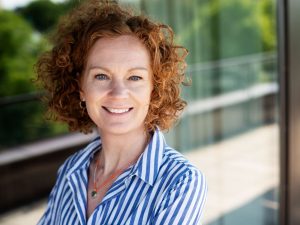
STOCKHOLM, Sweden — September 20, 2023 — Key members of TMAS – the Swedish Textile Machinery Association – will be taking part in the forthcoming ITMA Asia + CITME exhibition taking place from November 19-23 2023 at the National Exhibition and Convention Centre in Shanghai, China, with back-up from TMAS representatives, local support staff and agents.
“There is no escaping the fact that China remains the Number One textile manufacturing centre worldwide,” said TMAS Secretary General Therese Premler-Andersson. “We are very optimistic about the appetite for investment now, because China’s recovery from the pandemic has been so prolonged. Despite talk of losing market share in garment production to neighbours including Vietnam and India, China has a number of advantages — a massive domestic market and a highly developed infrastructure and supply chain network. Factories in China cover every possible product needed in the garment industry — from zips to buttons, to textiles and threads. There is a wealth of domestic producers and we still see big potential for further growth.”
Weaving
In the area of weaving, for example, 93 percent of the 114,000 new looms delivered in 2022 went to Asia, according to the latest figures from the International Textile Manufacturers Federation (ITMF), with China the top destination, followed by India.
As a result, TMAS members like Vandewiele Sweden AB (Hall 3, stand D01 in Shanghai) and Eltex (Hall 3, stand A01) have a huge market to address that has been established over many decades.
Vandewiele Sweden AB benefits from all of the synergies and accumulated know-how of the market-leading Vandewiele Group, supplying weft yarn feeding and tension control units for weaving looms to the majority of weaving machine manufacturers. It also retrofits its latest technologies to working mills to enable instant benefits in terms of productivity and control.
Yarn and sewing thread monitoring
With nearly 70 years of expertise in yarn sensor technology, Eltex of Sweden AB has consistently been at the forefront of new product development. Catering to the high-tech transformation of China’s textile manufacturing industry, Eltex has rolled out a suite of intelligent solutions built on a proven robust quality framework. Its EYE and EyETM systems are capable of accurately and efficiently monitoring the movement and tension of more than 1,000 yarns simultaneously. These systems are suitable for various applications and fibre types, including warping, winding, multiaxial weaving and new material applications.
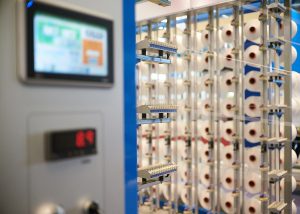
In addition, Eltex sewing tension monitors, such as the ETM422, have been increasingly well-received by customers. This high-precision device can monitor the tension of sewing threads in real time, effectively improving the quality and safety of sewn products. Particularly in China’s rapidly growing automotive manufacturing sector, the ETM422 has seen widespread use to meet the industry’s escalating demands for product safety and quality.
All of these devices and systems are smart, digitalized and capable of seamless integration with higher-level factory systems, enhancing intelligent manufacturing capabilities.
Dyeing and finishing
“Digitalisation, automation and AI have become the key enablers for sustainable gains across the entire textile industry and so much has been achieved in the past few years, especially in terms of automation,” says Premler-Andersson. “One area in which TMAS members are really making a difference right now, is in replacing water and energy-intensive technologies for the dyeing and finishing processes with new digital technologies.”
The TexCoat G4 non-contact spray technology for textile finishing and remoistening, for example, will be showcased in Shanghai by Baldwin at stand C22 in Hall 5. It not only reduces water, chemicals and energy consumption, but also provides the flexibility to adapt to a customer’s requirements in terms of single and double-sided finishing applications. The TexCoat G4 can reduce water consumption by as much as 50% compared to traditional padding application processes.
“We have already seen government policies encouraging factories to reduce their water usage and waste using tax incentives and grants and we expect more to come,” Premler-Andersson observes in conclusion. “This will take time, and China’s market in particular has been geared for many years to large volume production, but Swedish machinery innovators are there to support what is an inevitable transition. We are looking forward to fruitful discussions at ITMA Asia + CITME.”
Posted: September 20, 2023
Source: TMAS – The Swedish Textile Machinery Association