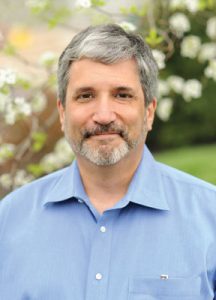
In the wake of DuPont Biomaterials’ rebranding to Covation Biomaterials, CEO Dr. Mike Saltzberg talks about its Sorona® polymer and the opportunity to expand the reach of its bio-based products as part of the Huafon Group.
TW Special Report
Commercialized in 2000, Sorona® polymer from Covation Biomaterials (CovationBio™) is not new but is now more relevant than ever as a demand for high-performance, sustainable textiles and circular production grows. CovationBio, formerly known as DuPont Biomaterials, took one of the first industry steps into this space when it launched Sorona for apparel and carpet end-uses in 2006. Sorona polymer features 37 percent renewable plant-based ingredients, which reduces the use of fossil fuels, and significantly improves environmental impact versus petro-based incumbent materials.
Bio-PDO™, the key ingredient for Sorona polymer, is produced from corn sugar, which is fermented in a process similar to beer brewing to create a bio-based 1,3-propanediol (Bio-PDO). When terephthalic acid is added to the Bio-PDO monomer, triexta — the generic name for a subclass of polytrimethylene terephthalate (PTT) polymers — is born. Sorona is CovationBio’s brand name for this polymer, which features attractive attributes such as exceptional drape, incredible hand feel, and built-in stain- and wrinkle-resistance, according to the company.
CovationBio reports that compared to nylon 6, Sorona consumes 30 percent less energy and results in 50 percent less greenhouse gas emissions.
CovationBio strives to enable a more circular economy — one in which affordable and high-performing biomaterials are accessible to everyone.
Textile World recently had the opportunity to speak with Dr. Mike Saltzberg, CEO of CovationBio, about Sorona’s origins, advantages, and future in a textile industry increasingly focused on sustainability.
TW: Sorona fiber was introduced in 2000, more than 20 years ago. What drove CovationBio to develop a fiber based on renewable plant-based ingredients?
Saltzberg: We were aware of the performance benefits of the Sorona PTT polymer based on research conducted in the 1950s and 1960s. However, the key monomer required to make Sorona — propanediol (PDO) — was not commercially available using petrol-based processes. Through groundbreaking innovation in biotechnology, we developed a plant-based fermentation route to manufacture PDO in an economically viable way that allowed us to commercialize Sorona. This Bio-PDO process also offers enormous environmental benefits versus a traditional petrochemical process.
TW: Sorona is partially plant-based. Are there other features of the fiber that make it more sustainable than traditional textile fibers?
Saltzberg: Sorona enables garments with exceptionally durable stretch and recovery, which means they retain their shape and have longer bagging resistance. This means end-consumers can hold on to their clothes longer, reducing the number of garments that consumers purchase over time and that end up as waste. Sorona also empowers a superior resistance to fading and pilling, which reduces micropolymer pollution caused by laundry. Finally, Sorona is mechanically recyclable in traditional polyester (PET) waste streams.
TW: What other properties make Sorona unique?
Saltzberg: Sorona exhibits many exciting performance attributes including exceptional softness, drape, quick-dry capability and even lightweight, breathable warmth when used in insulation. These attributes result in Sorona being used across a wide range of applications such as faux fur, puffer jackets, leggings and even cosmetic brushes. When spun in a bicomponent format together with PET, fibers are created with superior stretch and stretch recovery as compared with other elastomeric fibers like spandex.
TW: How is your team working to reduce global reliance on petroleum? Are there other fibers in development with a higher percentage of sustainable components?
Saltzberg: CovationBio supplies to industries that historically have relied on the production of petro-based man-made polymers for fashion, home textiles and industrial packaging. Now as part of the Huafon Group, a highly successful materials company, we are uniquely positioned to expand the reach of our current bio-based products and accelerate the introduction of new offerings and technologies to the market.
We will continue to build on our decades-long legacy and successful suite of products currently available in the market, including scalable, commercial offerings like Sorona and Susterra®, which are sourced from renewable feedstocks. Susterra is exciting as it provides a 100 percent plant-based, high-performance building block that reduces the need for petroleum-based components while enhancing end-product attributes.
Its applications range from footwear and outdoor apparel to coatings, inks and functional fluids.
We also have an exciting pipeline of innovations and materials in development and are working closely with our customers and stakeholders to deliver new products. This includes new materials that will enable high performance fibers that also have higher renewable and/or recycled content.
TW: In apparel, Sorona has found a myriad of applications. Talk about some of the innovative uses and how the fiber contributes to a more sustainable apparel industry.
Saltzberg: Sorona polymer can be spun into bicomponent stretch fibers, homofilament for shape memory fabrics, staple for use in insulation and spun yarns — in combination with natural fibers like cotton or wool — and other types of fibers. These fiber types can be incorporated into a wide variety of fabric qualities. We launched our Common Thread fabric certification program in 2020 to drive better trust and transparency throughout our supply chain.
Beyond the performance attributes for the five sub-brand fabric types — which include Agile, Aura, Luxe, Profile and Revive — our mills and brands using certified fabrics have access and permission to use our logos, proper brand colors and marketing language to discuss the bio-based components of the polymer included in the fabrics.
We are also seeing an increase in the use of Sorona for footwear. Using Sorona in footwear allows for movement, stretch and longer-lasting performance.
TW: Explain how Sorona is a suitable substitute for spandex? What are the environmental advantages of Sorona over spandex fibers?
Saltzberg: As mentioned earlier, when spun in a bicomponent format, Sorona-based fibers are created which “self-crimp,” meaning that they behave like tiny springs with a mechanical stretch and recovery effect. Traditional spandex gets its stretch from the elastomeric nature of the material itself, similar to a rubber band. This different stretch mechanism gives Sorona bicomponent fibers superior stretch recovery and durability to spandex. Sorona Agile is our sub-brand for spandex replacement for use in many, but not all, applications. Sorona Agile fabrics have better stretch and recovery than traditional spandex-based fabrics, while delivering superior recyclability and durability.
TW: How does Sorona differ from traditional carpet fibers? What sets the fiber apart?
Saltzberg: From a performance perspective, Sorona offers unparalleled softness, crush resistance and built-in stain resistance that is not available from other fiber types. Compared to nylon 6, Sorona production consumes 30 percent less energy and results in 50 percent less greenhouse gas emissions. In the carpet industry, Sorona carpets are generally regarded as the best option available on the market for consumers.
TW: How does CovationBio’s Sorona fiber impact the concept of circularity?
Saltzberg: Like other biomaterials, Sorona reduces society’s reliance on fossil feedstocks by providing an alternative source of high-performance chemicals and materials. Another important aspect of the circular economy is reducing consumers’ overall consumption and thus their waste production. As mentioned previously, part of this is enabling customers to reduce the amount of clothing they are buying and sending to a landfill. Sorona empowers garments with attributes that make it longer lasting and looking newer for longer.
It is, however, important to note that Sorona is not a biodegradable polymer but is mechanically recyclable in a traditional PET waste stream.
TW: What is the impact of the Common Thread Fabric Certification Program?
Saltzberg: In March of 2020, CovationBio launched its Common Thread Fabric Certification Program, a brand architecture and hangtag program designed to bring clarity and transparency for designers, apparel brands, and end customers. New fabric collections offered by mills are tested and certified through the program to assure the fabrics meet a certain level of biobased content and quality standards.
TW: How is the CovationBio team working to address the textile landfill issue?
Saltzberg: The number of textiles discarded and ending up in a landfill is directly connected to their durability. By extending the useful life and improving the performance of garments, particularly stretch garments, Sorona is reducing the amount of clothing wearers need to purchase.
For example, stretch fabrics and garments such as leggings made with Sorona-based fibers maintain their stretch performance and comfort through many more wash cycles than similar fabrics made with fossil-based spandex, helping customers and brands produce less textile waste.
July/August 2022