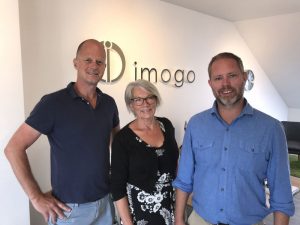
LIMHAMN, Sweden — February 8, 2021 — Swedish commission dyeing company 7H Färgeri is looking to propel itself to the forefront of sustainable fabric production with the installation of the first industrial scale imogo Dye-Max spray dyeing line.
Currently under construction, the line will be delivered in the first week of March to the 7H plant close to the Swedish city of Borås. It will have a full working width of 1.8 meters with an operating speed of up to 50 meters for the reactive dyeing of cellulosic fiber-based fabrics. In addition, it will be capable of carrying out the application of a wide range of fabric pre-treatments and finishing processes, providing the company with unbeatable flexibility in production.
A proven Mini-Max laboratory unit for predetermining application volumes and color matching will also be delivered as part of the contract.
With the potential to slash the use of fresh water, wastewater, energy and chemicals by as much as 90 percent compared to conventional jet dyeing systems, the DyeMax has gained considerable attention since the concept was outlined and a prototype machine constructed in 2019.
Pilot scale trials have subsequently been carried out with many well-known international textile companies and their brand partners.
The application unit of the Dye-Max consists of a closed chamber containing a series of spray cassettes with precision nozzles for accurate and consistent coverage, in combination with the patented imogo Pro Speed valve that controls the volume to be applied.
Control and precision
“We are achieving an extremely low liquor ratio of around 0.5-1 liters per kilo of fabric and we fully control the pickup, applying precisely what is required to the specific fabric,” said imogo founding partner Per Stenflo. “Compared to traditional padders there is no contamination of the dyebath or dilution of the dye liquor to worry about.
Fast changeovers with virtually no waste together with a high production speed enable a high productivity and unmatched production flexibility. The system is also equipped with an exhaust system and droplet separator to ensure that the environment around the unit is safe and free from particles.
The imogo Mini-Max meanwhile frees up valuable production time by avoiding wasteful pre-runs. The user simply sets the recipe with the Mini-Max and transfers the parameters to the Dye-Max recipe database for the system to be fully production ready.
7H Färgeri was founded in 1935 and has established itself as the Nordic region’s most complete dyeing and processing plant, specializing in technical and functional textiles for the automotive and soft furnishings sectors, as well as functional and protective clothing.
The family-owned business is now run by brothers Johan and Peter Engelmann.
“We are pleased to be pioneering a sustainable first for the dyeing industry,” said Johan Engelmann. “Our goal is to offer the market products and services with the highest quality in the most climate-smart and sustainable way, and imogo’s spray technology will give us the opportunity to offer innovative new services and products to both existing and new customers. It will be a very exciting journey.”
World Congress on Textile Coating
On February 12, Per Stenflo will make a presentation entitled “Transforming Textile Dyeing” during the online World Congress on Textile Coating which is held over four days, between February 11 and 19.
Posted February 8, 2021
Source: imogo AB