By Dipl. Ing. Kurt van Wersch, Senior Consultant, A. Monforts Textilmaschinen GmbH
Rapidly changing fashion trends constantly make new demands on textile finishers with ever newer specifications, particularly for the finishing of denim.
Finished denim fabric in wide-open form is a further opportunity for the finishers for the future.
Definition Of Shrinkage, Sanforization
Textile producers and finishers understand shrinkage as any form of negative change in dimensions of textile products under the influence of water and/or heat.
The term sanforization is used to refer to pre-emption of shrinkage by suitable mechanical and/or hydrothermal finishing processes.
Shrinkage potential after different treatment processes:
Woven fabrics
- Greige fabric, depending on fabric weight up to 10 percent;
- Greige denim (after stretching) up to 18 percent;
- Washed denim fabric up to 10 percent;
- Bleached fabric approx. 5 percent;
- Dyed fabric approx. 5 to 8 percent; and
- Shrunk (sanforized) fabric less than +/- 1 percent.
Knitted fabrics
- Dyed fabric approx. 7 to 15 percent; and
- Shrunk (sanforized) fabric less than 5 percent.
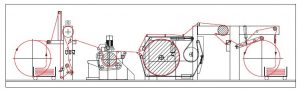
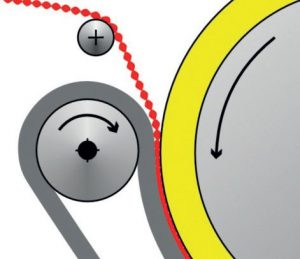
The heart of a shrinkage range is the rubber belt shrinkage unit, while felt calenders are used as dryers (See Figure 1). The principle of compressive shrinking (sanforizing) is shown in Figure 2.
- The fabric is dampened with water and steam;
- Pressing rubber belt 1 against the cylinder 2 causes an elastic elongation of the rubber belt (pressure zone);
- The extent of elongation is determined by pressure roll 3;
- The fabric is fed into the pressure zone;
- After the pressure zone, the rubber cloth relaxes again and goes back into its original form, taking the fabric with it; and
- Consequence: Shortening of the warp threads and hence compression of the weft threads. Shrinkage has taken place and is stabilized by tension-free drying
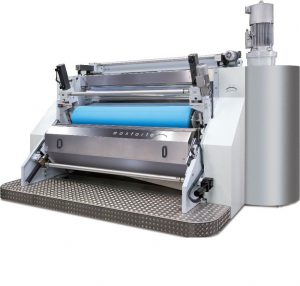
Figure 3 shows an original rubber belt shrinkage range
Fundamentals Of Denim Finishing
Greige denim fabric is characterised by one special feature. Although sanforized denim twill fabric no longer shrinks, it does have the characteristic that the finished legs of jeans tend to twist during washing. This means that treatment to prevent the twisting is also necessary here. Denim greige fabric is therefore subjected to the following four classic step treatment process on special denim finishing ranges.
- Singeing — twice on the blue side;
- Stretching — longitudinally to set the desired fabric width;
- Weft straightening — pulling the weft threads to prevent twisting; and
- Compressive shrinkage.
Today, however, only a fraction of the denim production is processed directly from greige fabric. Denim open-wide fabric can be washed, desized, mercerized or over-dyed before shrinking.
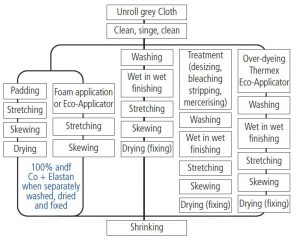
Figure 4 shows the treatment possibilities and processes. All the treatments always finish with the shrinkage process. Before the shrinkage process, a washing test should be performed prior to each fabric batch to be shrunk in order to determine the shrinkage potential. The fabric shrinkage in warp and weft direction and the degree of skewing are measured. The washing shrinkage in warp direction and the degree of skewing provide indicative values for the setting of the denim shrinkage range.
Classic Denim Ranges With Stretcher And Weft Straightener
Monforts denim ranges are tailored to the customer’s needs and are in operation with many leading denim producers. Sophisticated denim concepts are offered, from individual machines through to full-scale finishing ranges
The classic configurations include:
- Padder-stretcher-cylinder dryer-shrinkage range version; and
- Energy-saving foam applicator-stretcher-shrinkage range version, whereby
- today the foam applicator can be replaced by the Matex ECO Applicator. This also eliminates the need for a foam mixer.
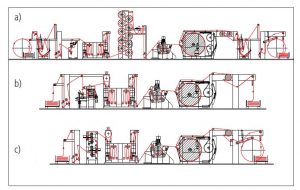
Figure 5 shows the principles of the three range variants.
For example, a denim fabric comes from the weaving shop with a greige width of 157 centimeters (cm) and is later to have a finished width of 151 cm. In order to achieve this value, the fabric is stretched with high force — for a 14.5 oz/yd² article, up to 4000 Newtons (N) and sometimes even more — so that its width is reduced.
At the same time, the rolls in the stretcher are inclined in order to create the weft skewing. In greige fabric, the weft skewing can be as much as 8 percent —approximately 12 cm.
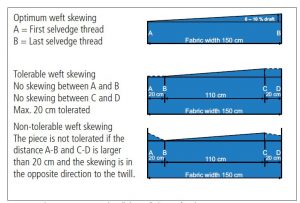
Figure 6 explains the weft skewing, shows optimum values and what is tolerable and not tolerable. Two stretcher types are used in classic denim finishing ranges — simplex stretcher and duplex stretcher. The simplex stretcher is still frequently used today by Monforts competitors (See Figure 7).
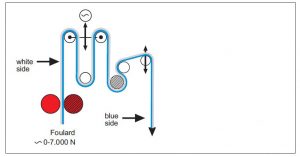
A disadvantage of these stretchers is that stretching tension is built up between the padder and the tension roller of the stretcher, placing extreme loads on the rubber coating of the padder rolls. Monforts therefore changed over to the duplex stretcher from any early stage.
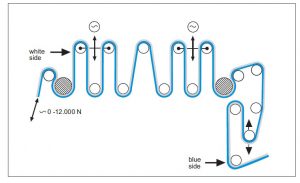
This stretcher has two independent holding points separate from the other range components. The force required for stretching and skewing is built up between the draw roller pair and the tension roller pair of the stretcher (See Figure 8).
This range type with foam applicator and steaming drum was the first step towards saving drying energy by eliminating the cylinder dryer.
Modern Denim Ranges With Stretcher And Weft Straightener
Innovative further developments of the Monforts denim ranges have led to new ecological and economical denim finishing ranges being successfully marketed today.
Figure 9 shows the Eco version of a present-day denim finishing range.

Several ecological and economical features are implemented in this range concept, including:
- An Eco-Applicator that is employed as liquor application unit. The Eco-Applicator is a minimum application unit that applies the finishing liquor in a controlled manner to both sides of the fabric. The minimum moisture is sufficient for stretching and skewing the fabric.
- The ThermoStretch stretcher is used as stretcher and weft straightener for drying, stretching, skewing and thread counting, aided by a structure detector with SD1 camera technology. The camera measures and controls the fabric width and the skewing. As an option, the weft threads are also counted by the SD 1 camera (See Figure 10).
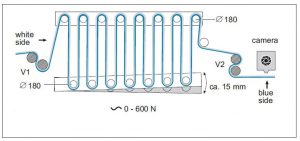
This range configuration allows speeds of 35 to 40 meters per minute (m/min) to be achieved with a 14.5 ounce per square yard (oz/yd²) unwashed article. Lower denim weight classes and washed open-wide fabric can naturally be run correspondingly faster. Figure 11 shows the Eco version as a high-speed machine or double rubber.
This version that has been proven for years comprises two rubber calenders and two felt calenders and thus achieves a production speed of 70 to 80 m/min with a 14.5 oz/yd² denim. Here again, lower denim weight classes and washed open-wide fabric can naturally be run correspondingly faster.
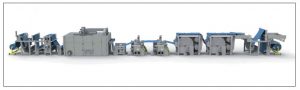
Description of the ThermoStretch Stretcher And Weft Straightener
The ThermoStretch stretcher is a modified hotflue with reinforced and adjustable rolls with a diameter of 180 millimeters (mm). The stretcher can be heated and the fabric moisture at the exit is regulated to suit the shrinkage process.
Figure 10 shows schematically the function of the stretcher and weft straightener.
With their differently controlled speeds V1 and V2, the two tension rolls determine the longitudinal tension in the fabric, and hence the reduction in width, monitored and controlled by the Pleva SD 1 camera. The camera also measures the weft thread position, and monitors and controls the skew by skewing on side of the roll package in the ThermoStretch stretcher.
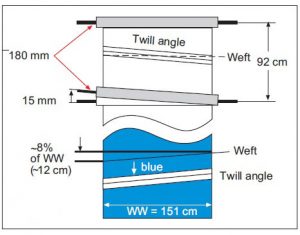
As the ThermoStretch has a large number of guide rolls and can also be heated, as shown in figure 12, the damp fabric can be stretched with a longitudinal tension of 200-300 N, instead of 4000 N as in the past.
The skewing of the rolls is adjusted in millimeters — rather than in centimeters as in the past — resulting in crease-free running of the fabric. The warm and damp stretching process requires far less force, making it gentler on the fabric and resulting in a better fabric appearance. Furthermore, the residual moisture in the fabric is measured and controlled so that it arrives at the actual shrinkage process with a controlled and constant moisture content.
The benefits of these innovations are:
- Greatly reduced stretching forces;
- Extremely low load on the fabric during the stretching process;
- Skewing of the rolls in millimeters rather than in centimeters;
- No creasing of the fabric during the passage;
- Skewing takes place in a large number of small individual steps;
- Higher production speeds on Eco Applicator ranges;
- More precise residual moisture measurement and control upline of the rubber calender;
- Wider range of possibilities for fabric treatment; and
- Remarkable differences in the fabric quality by comparison with competitors’ products thanks to innovations and modern technologies.
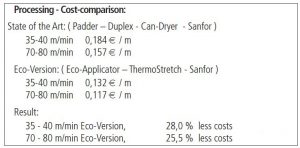
Cost Savings From The Use Of Eco Versions
It is interesting to compare the state-of-the-art denim ranges with the new Eco versions. If we consider the costs for denim finishing in euros per running meter, we observe the following: The Eco versions are always less costly, as shown in figure 13. These cost calculations are based on prices in Germany and represent only a trend. Country-specific deviations are possible.
As can be seen, the Eco range with one rubber calender and one felt calender is more economical by 28 percent during the production of a 14.5 oz/yd² article, and the costs per meter of finished fabric on the Eco range with two rubber calenders and two felt calenders are 25.5-percent lower.
The Eco versions offer the user the following benefits:
- More controllable process;
- Better fabric quality;
- Less steam energy;
- Less electrical energy;
- Lower water consumption
- Fewer chemicals used; and
- Lower costs per running meter.
Finishing Of Elastic Denim Fabric
Elastic denim fabric has already established itself in the denim industry with growing market shares. Many premium denim brands employ modern stretch denim. These articles today have a more natural appearance and are no longer as glossy.
These articles require a few treatment steps more than for normal classic denim finishing. The finishing process is therefore slightly more costly, but the prices that can be achieved are also somewhat better than for the classic denim fabric.
Apart from elastic texturized polyester — xpand from Trevira, for example — with approximately 20 percent stretch, yarns of elastane fibres with approximately 40 percent stretch are frequently used to maintain the form stability and to improve the wearing comfort. Of the elastane fibers Dorlastan®, Lycra®, Linel®, Glospun®, Roicka® and Teplon®, may be used in denim.
From its molecular structure, elastane is a fiber with a polyurethane hard segment and a polyether or polyester soft segment, whereby the soft segment is responsible for the properties of the fiber. As a large number of these fiber types are encountered, it is essential to observe the information provided by the respective fiber producers with respect to controlled shrinkage and proper fiber fixing.
The producer should be consulted on the deviation ranges of the elastane fibers to be used in order to create optimum conditions for finishing. When selecting the finishing parameters — pH value, treatment time and mechanical influence — care must be taken from the point of view of the elastane fibers that the intended finished product data of the article are not impaired. For denim articles, cotton blends with different percentages of elastane are used.
The Behavior Of Weft-Elastic Denim Fabric
A classic denim fabric without elastane content normally has a greige width of 157 to 159 cm. The washing tests on such articles show on average a shrinkage of -15 percent in the warp direction and -6 percent in the weft direction.
The weft-elastic denim fabric with elastane content may have a greige width of 180 cm and also shrinks during the washing test on average by -15 percent in the warp direction, but by -34 percent in the weft direction.
This means that the fabric still had a width of approximately 119 cm after washing. And that with a desired finished width of 151 cm. The weft-elastic denim fabric therefore always has to be stabilized.
The fabric is heat-set in order to achieve:
- A desired stretch;
- A desired weight per square meter;
- A desired finished width;
- A desired improvement in the dimensional stability; and
- To avoid cold creep shrinkage.
Fixing ranges at 180 to 200°C lie in the order of 15 to 60 second dwell time. The fiber manufacturer’s recommendations have to be observed here. Within this range, the fabric reacts under optimum conditions. The times cited in this article are empirical values from the respective finishers.
The Discontinuous Finishing Method For Weft-Elastic Denim Fabric
After singeing, the weft-elastic denim greige cloth with a 180 cm fabric width undergoes hot washing on a washing machine where the fabric is washed and the majority of the size is removed. The fabric is then predried, padded — liquor application — and then dried and fixed on a tenter with a drying and fixing temperature of 190°C, tentering width 152 cm. The third finishing step is the compressive shrinkage process.
The fabric to be shrunk is sprayed with water, passed over a steaming drum, skewed on a weft straightener and then fed to the rubber calender with a defined rubber
blanket pressure before finally being dried on the felt calender. Instead of the spray system, the Matex ECO-Applicator can also be used for a selective moisture application.
The fabric width before the rubber calender is 150 cm; the fabric width after the felt calender is also 150 cm.
The washed shrinkage values after treatment showed a residual shrinkage in the warp direction of -1 percent and residual shrinkage in the weft direction of -1.5 percent, thus falling within the range of the international standards required by Levis, Lee, Wrangler, Maverick, Mustang and General, for example.
These respectable residual shrinkage values are achieved in three separate finishing steps as shown in Figure 14.
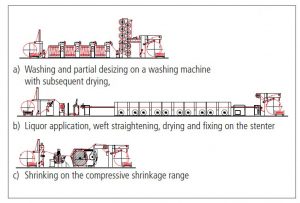
The Fully Continuous Finishing Method For Weft-Elastic Denim Fabric
When planning new denim finishing ranges, the wish is frequently expressed to be able to finish non-elastic and weft-elastic denim fabrics on the same range.
For non-elastic denim fabric, washing compartments have been part of the denim range for many years. For weft-elastic denim fabrics, however, not only the washing process but also the fixing process to stabilize the fabric is required.

Figure 15 shows a range configuration for normal denim articles with the possibility of continuous finishing of large production quantities of weft-elastic denim fabric. After unrolling, cleaning and singeing (1) the fabric is washed (2), squeezed and padded again (3) where a suction bar can increase the moisture difference for the second padder passage. The Matex ECO-Applicator can also be used instead of a second padder. While non-elastic denim fabric, stretched and skewed (4) is fed from the cylinder drier (5) with controlled residual moisture to the width control via the tenter (6) and then to the rubber and felt calender (7), the elastic denim fabric has to be heat-set on the tenter.
After the fixing process, the over-dried fabric is cooled and moistened again (8) so that the fabric again has the moisture necessary for shrinking. The delivery combination (9) with scray and Sochor winder ensures strain-free winding of the shrunk, weft-elastic fabric.
Compared with the discontinuous method, the investment cost for the fully continuous method are slightly higher, but this is the least expensive method in the costs per meter.
The following points favour the use of the fully continuous method for the finishing of weft-elastic denim fabrics:
- Higher utilization of the range;
- Higher production speed;
- Lower space requirement; and
- Lower personnel costs.
The Fully Continuous Finishing Method For Classic And Elastic Denim Fabrics
The most modern, most ecological and most economical denim range version is shown in Figure 16.

This range allows fabric webs of 100-percent cotton and of cotton blends with elastane to be finished. Different setting parameters are selected, depending on the quality.
After unrolling, the grey fabric is cleaned and singed. In the following washing compartments, the fabric is partly desized and the first shrinkage in the length and width of the fabric web takes place. Other processes can also be integrated, depending on the number of washing compartments. A high-performance squeezing unit optimally dewaters the fabric web for a wet-in-wet process. Minimal amounts of finishing liquor are applied with the ECO-Applicator. A concentration check of the finishing liquor, as is necessary with the wet-in-wet process with two padders, can be eliminated here. When using the ECO-Applicator, the finishing liquor is not diluted.
The fabric is then predried in the cylinder drier unit. Residual drying, stretching and skewing are performed on the ThermoStretch stretcher and weft straightener. The fabric is thereby carefully stretched in stages by passing it over rollers while skewing and stretching in small steps. The process takes place in a defined temperature and moisture climate and achieves better fabric appearances.
Compared with the conventional denim stretching technique this means: Significantly lower stretching forces, less fabric tension, better ‘look and feel’, Higher production speed and simpler residual moisture control.
The fabric width, skew and number of filling threads is monitored by a special camera and the measured values are converted into corresponding control pulses for the range control.
The following tenter with upline Matex ECO-Applicator and a coating range is then used either for finishing, drying of the coating or surface stabilization (fixing), depending on the article. The machine settings depend on the process to be employed. The fabric arrives at the range for the compressive shrinking process with a controlled residual moisture content or with moisture application using the Matex ECO-Applicator. Two rubber calenders and two felt calenders ensure a high production speed with gentle use of the rubber blanket and effective energy consumption.
Two rubber calenders and two felt calenders are required to produce denim of 14.5 oz/yd² with 1 to 2-percent residual shrinkage at speeds of at least 70 m/min.
Low-tension guidance of the fabric during rolling is important for the end of the process.
January 18, 2018
Article courtesy of Germany-based A. Monforts Textilmaschinen GmbH