Lubricants can be a powerful resource when it comes to energy savings in textile manufacturing operations.
By Max Jaworski
In an economic climate where manufacturers are eager to reduce their carbon footprint and cut costs, increasing sustainability has become a central focus. The textile industry is no exception. In fact, textile manufacturers are up against a unique set of challenges when it comes to efficiency including high energy consumption, constant machine stress, and the need for reliable, long-term performance.
While traditional methods like upgrading equipment, eliminating hazardous raw materials, and recycling scrap materials can be effective ways to save energy, these options tend to be complex, expensive and time-consuming. There is another, much simpler — and cost-effective — route to saving energy in textile operations: lubricants.
Rather than looking at machine component factors such as hardness of gears, bearing selection, materials and geometry, lubricants may be the best place to start when seeking ways to increase efficiency. The right gear oil, hydraulic oil, or compressor oil can revolutionize textile production, leading to benefits such as lower wear rates, reduced operating temperatures, and, most importantly, increased energy efficiency.
Challenges In Textile Machinery
It’s no secret that textile manufacturing environments are particularly rigorous on machine components. Machines operate under extreme stress because of:
- Continuous operation — textile machines often run 24/7, making any downtime costly;
- High loads — machines must handle significant mechanical stress, leading to wear and tear;
- Varying operating conditions —variables like speed, vibration and contaminants cause each component to have its own set of challenges; and
- Temperature variations and humidity — heat buildup and high humidity can accelerate oil degradation and component wear, requiring lubricants to have superior water resistance and oxidation stability.
Maintenance is an arduous task and is thus carried out only at long intervals in many cases. Therefore, selecting the right lubricant is critical — both for the initial lubrication of a component and relubrication during operation. By investing in high-quality lubricants, manufacturers not only extend the lifespan of their equipment but also enjoy reduced maintenance and labor costs, longer oil change intervals, and increased overall profitability.
Where Are Lubricants Used In The Textile Industry?
Germany-based Klüber Lubrication — a business division of Freudenberg Chemical Specialities SE & Co. KG — sees lubricants as a fundamental design element of textile machines. Original Equipment Manufacturers (OEM’s) have to match the individual component requirements to ensure optimal performance is achieved as efficiently as possible.
Klüber’s specialty lubricants cover the entire production process in the textile industry, including:
- Spinning machines where the lubricants impart excellent corrosion protection for bearings, spinning turbines, opening rollers, spinning pumps and spinnerets;
- Knitting machines for long service life with minimum maintenance requirements for needles and sinkers, slide rails and guide bars;
- Weaving machines offering longer intervals between maintenance operations because of minimum-quantity lubrication for gears, gripper looms and chains;
- Finishing machines and tenter frames whereby the lubricants con-fer resistance to water and steam as well as acidic and alkaline solutions for steamers, rolling bearings, compensators and rollers; and
- Nonwoven machines where they offer high load carrying capacity and good pressure absorption for needlepunch, spunlace and spunbond operations.
Proven Efficiency Gains In Textile Production
Klüber Lubrication has studied how synthetic lubricants perform in textile manufacturing and found clear improvements over traditional oils including lower energy use, better equipment performance and faster return on investment.
Across sectors, manufacturers who switch to specialty synthetic lubricants may experience:
- An average of 2- to 5-percent energy savings;
- An average needle temperature reduction of 3.5°C; and
- An average payback period of less than a year.
In knitting machines, Klüber Lubrication customers have achieved:
- 4.8-percent energy savings;
- A seven-month payback period; and
- Carbon dioxide savings of 3.8 tons.
In weaving machines, Klüber Lubrication customers have achieved:
- $68,000 annual cost savings;
- 4-percent energy savings;
- A two-month payback period; and
- Carbon dioxide savings of 272 tons.

The Right Oil Makes All The Difference
In any textile operation, lubrication plays a vital role in production — and in efficiency. To make an operation run as efficiently as possible, manufacturers must select the right oil for applications such as gearboxes, hydraulic systems and air compressors. The right oil comes down to the base oil and additives. Essential requirements for textile lubricants are described by leading manufacturers in international standards and specifications. They include:
- Operating temperature range;
- Viscosity;
- Aging behavior;
- Low-temperature behavior;
- Corrosion protection on steel and nonferrous metal;
- Foam behavior;
- Elastomer compatibility;
- Compatibility with interior coat-ings; and
- Wear protection against fretting or micropitting.
When it comes to energy efficiency, not all oils are created equal. In fact, oils with a synthetic base have significantly longer lifespans than those with a mineral base. Polyalkylene glycols (PAGs), for example, absolutely shine as the most efficient and lowest-wear type of oils, particularly in high-sliding applications such as worm and hypoid gears. In these applications, PAGs offer a lower coefficient of friction within the gearbox, resulting in a reduction in power loss. While a standard mineral oil may require replacement every 5,000 hours, synthetic hydrocarbon oils such as polyalphaolefins (PAOs) — which offer stability, but are less resistant to thermal degradation and sliding friction than PAGs — can last approximately 15,000 hours, and PAGs can reach 25,000 hours at the same temperature. This translates to fewer oil changes, lower maintenance downtime, and increased production uptime.
Additionally, oxidation is one of the common factors leading to oil degradation, affecting its performance and requiring frequent replenishment. High-performance synthetic lubricants slow this process, maintaining oil integrity, which reduces the frequency of oil changes.
Proven Efficiency Gains In Gearboxes
When it comes to gears, the most significant energy savings are seen in gear types with inherently lower efficiencies, such as worm drives. For example, tests performed by Klüber Lubrication show that a worm gear running with a conventional mineral oil operates at around 60 percent efficiency. When switched to a synthetic PAO lubricant, efficiency increases to 70 percent; and with a PAG lubricant, it jumps to 78 percent.
For textile plants with hundreds of gear-driven machines, these efficiency gains compound, leading to substantial energy savings and lower operational costs. The up-front cost of a high-quality synthetic lubricant is quickly offset by long-term reductions in energy consumption and maintenance expenses.
Applications In Textile Machinery
To operate at peak efficiency, different types of textile machinery require their own specialized lubrication solution. For special applications, such as those in which very long service intervals are to be expected or where operating conditions are very unique, the team at Klüber Lubrication is always avail-able to help select the correct solution for a plant’s equipment. When selecting the right oil for a particular machine, parameters such as performance, speed, environmental influences, and special operating conditions need to be taken into consideration.
Based on this information, it is possible to select the oil type, wear protection, and viscosity that enable the oil to optimally perform its tasks, which include:
- Absorbing forces;
- Reducing friction;
- Minimizing wear;
- Dissipating heat; and
- Absorbing wear and contamination.
Even within the same operation, experts understand that each element of the equipment has a different need. That’s why the team of experts at Klüber Lubrication partner with OEMs to understand the unique needs of the machinery and provide lubricant recommendations, as well as technical support.
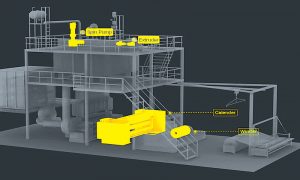
As an example, consider the spun-bond polymer extrusion system shown in Figure 1. Each part requires a different lubrication solution to perform its individual function and keep the system working efficiently as a whole.
By partnering with lubrication experts, a textile manufacturer can select the correct viscosity and additive package to optimize performance and reliability while reducing maintenance-related downtime. Don’t settle for the wrong lubricants when it’s simple to find the right ones with a reliable partner by your side.
Klüber Lubrication: Committed To Efficiency And Sustainability
To further its commitment to saving time, energy, and money, Klüber Lubrication has developed Klüber Energy Efficiency, an innovative pro-gram that verifies energy savings. This solution includes certified measurements, comprehensive analyses, and recommendations for the optimal lubricant solution.
Klüber Lubrication is also a globally recognized leader in specialty lubricants, earning an EcoVadis Gold rating for sustainability four years in a row, placing the company in the top 5 percent of sustainability-focused companies worldwide.
The EcoVadis Gold status reflects Klüber’s commitment to:
- Reducing environmental impact;
- Extending machine lifespan; and
- Lowering energy consumption.
By partnering with Klüber Lubrication, manufacturers not only enhance machine efficiency but also contribute to sustainable industrial practices.
The Smartest Investment For A Textile Plant
Switching to a high-quality synthetic gear oil is one of the simplest and most effective ways for textile manufacturers to reduce energy consumption.
The key benefits include:
- Lower operating temperatures, which result in reduced thermal degradation;
- Longer oil change intervals, which result in less downtime and maintenance;
- Reduced wear, which results in extended equipment life; and
- Increased energy efficiency, which results in substantial cost savings.
Access to expert lubricant recommendations tailored to your specific needs can unlock sustainability and revolutionize efficiency like never before.
Editor’s Note: Max Jaworski is an engineer – Textile Global Industry Team, Klüber Lubrication. He can be reached at max.jaworski@klueber.com.
2025 Quarterly Issue II