By Ray Spurgeon
The apparel industry has recently endured troubling product recalls after needles were found in children’s clothing. In one case, more than 17,000 items of popular baby clothes were recalled after a needle was left inside a onesie. In another incident, a manufacturer put out an urgent recall of 12,000 pieces of children’s clothing after parents found a sewing needle attached to a garment. These types of metal contamination recall events occur all too often and can threaten an apparel company’s reputation and future.
Despite careful attention and sound manufacturing practices, looming and sewing needles can find their way into finished consumer apparel products. While the industry has utilized metal detectors for quite some time, there are new approaches to positioning the equipment in different locations throughout the process to better safeguard against metal contamination.
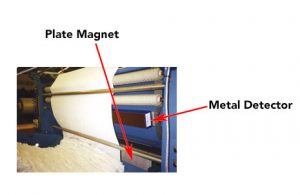
Eriez® has served the textile industry for more than 25 years, supplying metal detectors and magnetic separators. This equipment is primarily used on the non-woven web off looms, as shown in Figure 1. Before the introduction of metal detectors, manufacturers mounted wide plate magnets below or above the web to “pull out” the highly magnetic needles.
Manufacturers discovered this solution was unreliable as the needles were frequently dragged off the magnet by the moving web and wedged back into the nonwoven web. This started the trend toward installing metal detectors. Upon detection, metal detectors signal an audible and visual alarm to prompt operators to shut down the line and remove the metal. Although this approach continues to be a solid first line of defense for needle detection and removal, it does little to ensure needles do not make their way into the finished packaged product.
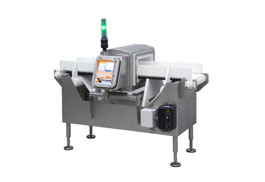
Finished Packaged Metal Detection: Taking Needle Inspection to the Next Level
Recognizing the limitations of needle detection and removal using magnets on nonwoven webs, big box stores are now directing apparel manufacturers to add metal detectors on their finished package lines using a belt system (See Figure 2). The metal detector system conveys the packages through the aperture and signals an alarm or actuates a reject device when metal is detected. In most applications, these systems will detect broken needles down to the millimeter size level. However, each needle’s unique orientation affects detectability, making it important to understand the implications this presents.
What is the Impact of the Needle’s Orientation?
Most metal detector manufactures quantify a metal detector’s sensitivity in spherical sizes. Simply stated, a sphere has no orientation due to its shape. Conversely, a needle has many constituents, including its diameter, length, scarf size, tip, eyelet and more. These factors make it difficult to quantify detection thresholds. Therefore, we will dig deeper into needle orientation using a simple illustration.
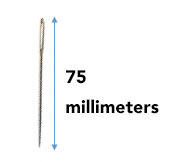
Figure 3 shows a 1-millimeter diameter x 75-millimeter long needle in what a human eye sees as a “favorable” orientation; that is to say there is a lot of visible surface area. Similarly, when a needle passes through a detector in a favorable orientation (lots of surface area), the detector easily “sees” it. The signal strength — known as amplitude in metal detector terms– is at its greatest in this orientation, making it easily detectable.
Conversely, Figure 4 illustrates the same needle, but from the end view (1 millimeter). Using the human eye analogy, the needle is in an unfavorable orientation, as there is very limited surface area. Accordingly, it is more difficult for the metal detector to detect in this unfavorable orientation.
Figure 4: A needle in its worst orientation can have a spherical equivalent of 1 millimeter or less.
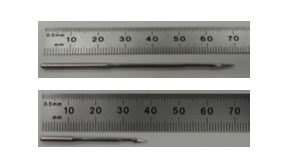
Equating Sphere Size to Needle Detection
As mentioned, a needle’s orientation and size have a profound impact on its detectability (also known as amplitude). This makes it problematic to quantify sensitivities since there are infinite geometric ways it could pass through a metal detector. For that reason, Eriez test lab technicians incrementally cut the needles down (See Figure 5) to first determine the smallest detectable needle in its best orientation. Afterwards each needle is passed through the detector in its worst orientation and amplitude is measured. Finally, a certified sphere is passed through the detector to determine the spherical size that duplicates the needle’s amplitude. This information is communicated in a material test report.
Sizing and Specifying a Metal Detector to Get the Best Possible Needle Detection
Since a metal detector’s sensitivity is linear to its opening (See Figure 6), smaller apertures equate to better detection. That said, there are a couple of axioms when sizing the equipment. Typically, we will take the package height and width and add 3-4 inches. Accordingly, assuming a package of socks measures 4-inches high x 10-inches wide, a 14-inch wide x 8-inch high aperture would be recommended. Empirically we know the best achievable sensitivity would be in the range of 1.2 millimeter ferrous sphere, which in this application equates to a 1 millimeter diameter x 1.2 millimeter long broken needle.
Figure 6: A metal detector’s aperture height and width determine needle detectability.
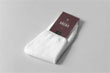
The size of the detectable needle may be unacceptable to an end user in some cases, making an alternative necessary. In the previous example, a bundle of packaged socks was scanned in a 14-inch x 8-inch aperture. If a single pack (See Figure 7) was selected, a much smaller aperture could be used, which would allow for significantly smaller needle tip detection. This is the balance that needs to be considered when selecting a metal detector to meet an end user’s detection requirements.
In summary, needles will inevitably find their way into finished apparel. Employing metal detection on finished packages is essential for avoiding recalls which can damage a manufacturer’s reputation and significantly decrease their revenue
Commonly Asked Questions about Installing Metal Detector Conveyor Systems
Question: How much space does a conveyor system require?
Answer: The system size is dependent upon the aperture dimension and whether a reject device is needed. More often than not, it requires 5-7 feet.
Question: Can I install a metal detector on my existing conveyor?
Answer: The short answer is yes, but this is not recommended as metal detector conveyors require very specific design criteria such as continuous weld elements to prevent make and breaks on electrical eddy current loops, anti-static slider bed material, isolations on fasteners using shoulder washers and proper metal free zones, to name just a few.
Question: What sort of preventive maintenance is required?
Answer: Eriez metal detectors require no periodic maintenance or tuning. All critical circuits are continually scanned. If a problem occurs, a warning alarm is initiated.
Question: How much do these systems cost?
Answer: Depending on the size and sophistication of the unit, you can expect to pay $20,000 to $30,000.
Editor’s Note: Ray Spurgeon is Metal Detection product manager at Erie-Pa.-based Eriez®.
August 16, 2018