T
oday, the manufacturers and users of processing machines for web-type materials are
confronted with ever-increasing demands, such as faster and more precise production processes,
improved product quality; and reduced personnel, waste and, above all, downtime. Web guiding
systems decisively fulfill these requirements.
Principle
Typically, web-type materials are fed from a reel to the machine, processed and then
rewound. During these stages, various position errors may occur. Web guiding systems are designed
to eliminate these negative process influences and assure permanent, precise web alignment and
winding. Depending on the type of material application and task, a wide variety of systems are
specially designed to improve quality and increase productivity.
In web guiding systems, a sensor detects the web position compared to a reference point.
This is usually the web edge, but it may be a printed line or a strong color contrast on the web.
The current actual web position value is compared with the set value by the controller, which then
sends the difference of these two values as a signal to the system-actuating element, which, in
turn, corrects web travel.
Detection Systems
With progressive technology, detection systems have come a long way from being simple
mechanical sensors to sophisticated digital infrared sensors, wide-band arrays, or charge-coupled
device (CCD) cameras. The right choice of sensor specific to the application is important to
guarantee optimal results.
Infrared sensors are in wide use, for example, in tenter infeed systems, highly accurate
edge guiding on printing lines, and center-positioning on laminating processes. These sensors
typically have a very narrow detection range and, therefore, provide highly accurate detection of
any type of edge. In principle, an optoelectronic, infrared edge sensor distinguishes itself by a
highly compact and stable construction with an integrated CCD chip. Due to the permanent adjustment
of the sensor to ambient conditions, practically all webs can be reliably scanned, including those
with very little light reflection.
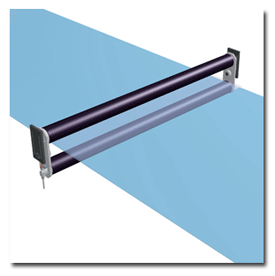
Figure 1: Wide band sensors can be used for edge detection, center guiding and width
monitoring.
Wide band sensors allow various-width materials to be processed without mechanical sensor
position changes
(See Figure 1). The sensor operates with infrared transmitters and receivers placed on
opposite faces of the web, and senses the edges using special scanning techniques. It is, however,
not as accurate as a stand-alone infrared edge detector and is primarily used for guiding
applications in which less precision can be tolerated. Detection accuracies can vary from 3 to 7
millimeters (mm), depending on the technology used. Wide band sensors can be used for edge
detection and center guiding, and, because of their construction, also as width monitors.
Correction Devices
There is a wide range of different correction devices available in combination with the
different detection systems to make a perfect fit to any process in the textile industry. Subject
to the application and the fabric type, the device may be a segmented roller guide, a steering
roller, a pivoting frame or a web guider.
The most economical guiders – the well-known two-roll edge guiders – have been around for
decades. The web edge is detected either mechanically by a sensor lever or without contact using
optoelectronics. The sensor signal controls a diaphragm cylinder or a lifting magnet that presses
the control roller against the counter pressure roller. The web edge is controlled by roller offset
and nip pressure. For more accurate edge guiding, a built-in broadband sensor with web edge
fluctuations up to +/- 80 mm is available due to the large scanning range – 120 mm – of the
infrared sensor system. For delicate webs, an additional electrical drive for the top roller
ensures that the friction torque on the rollers is compensated and stretching of the web is
avoided.
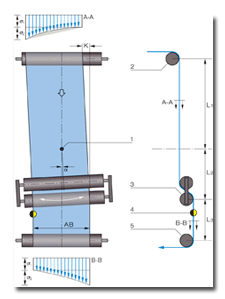
Figure 2: Steering roller assemblies perform two different movements in one correction
procedure.
A steering roller assembly consists of two or more rollers and performs two different
movements in one correction procedure
(See Figure 2). First, it tilts toward the web direction of travel to achieve a continuous
righting of the moving web. Second, it assumes a lateral offset vertical to the web direction of
travel to effect an immediate reparation. This rectifying action is achieved by a lever system as
shown in the sketch. The web must be friction-locked to the guide rollers.
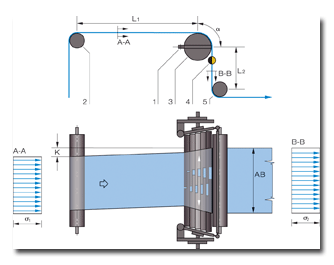
Figure 3: Segemented roller guides maintain uniform distribution of tension across woven,
knitted or nonwoven webs.
The segmented roller guider is the optimum web guiding system for all applications across
the entire textile-processing spectrum
(See Figure 3). It guides woven, knitted, and, to a certain extent, nonwoven fabrics in
dry, damp or dripping wet conditions, in steamers exposed to high temperature and finishing
chemicals. In the event of major corrections, the guider maintains a uniform distribution of
tension across the web, thus minimizing weft distortion. The web rests on the guiding slats along
its full width. The slats carry the web around the roll while moving laterally, providing a minimum
offset – thus eliminating the risk of a skewed web. The guide rollers can be designed with split
slats and perform web guiding and web spreading simultaneously. Scroll rollers or pneumatic
uncurlers can also be added for uncurling and additional spreading capability. A good degree of
friction between the segmented roller guiding slats and the fabric web is essential for an
efficient web guiding process. Many modern quality fabrics feature extremely sensitive surfaces
that may be slightly impaired by the contact areas of the guiding slats should these be too
aggressive. Various slat coverings offer the possibility to process these fabrics safely.
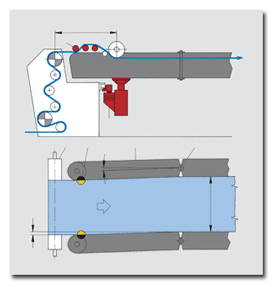
Figure 4: Tenter rail guiding systems ensure precise positioning of tenter frame clips or
pins to the fabric edges at the infeed of the tenter frame.
Tenter rail guiding systems ensure precise positioning of tenter frame clips or pins to the
edges of the fabric at the infeed of the tenter frame, which is critical to producing quality
fabric with consistent width
(See Figure 4). As speeds have greatly increased, this control has been improved through
the development of highly accurate infrared edge sensors, digital controllers, and positioners with
encoder feedback. The rails can be moved at rates from 120 to 180 mm per second to exactly follow
the fabric edges.
Many textile processes require the use of unwind or rewind systems to properly control the
fabric into the process and to produce rolls of fabric with uniform edges at the rewind station.
Various sensors – such as edge, line, or center-guiding – can be used; and various actuators are
available for different strokes and forces.
A range of control systems consisting of sensors, controllers and actuators can be adapted
for many other positioning applications, such as coater-dam positioning and slitter positioning,
for example.
Heightened Control
Despite a consistent specialization in web guiding systems for the various automation and
production processes in the textile industry, a broad range of products, from individual mechanical
components to multifunctional systems, is available to meet the requirements. This means that even
the most complex projects may be completed cost-effectively. These efficiency solutions provide
manufacturers with heightened control of processing variables, which ultimately increases
productivity, reduces waste, and improves the quality of the end product.
Editor’s Note: Udo Skarke is CEO of Erhardt + Leimer Inc., Duncan, S.C.