I
t is difficult for textile finishing to escape the image of an industry that produces
emissions. However, there are ways to drastically reduce the difficulties associated with wet
chemical processes. This article describes the increasing global problems in the area of water and
energy policies, and presents a case study that demonstrates how it is possible to run
wastewater-free textile finishing operations.
Within the textile industry, finishing is one of the main sources of emissions. As a
supplier of modern, high-performance textile finishing machines that are both energy- and
water-efficient, Switzerland-based Benninger AG has now gone one step further to offer a new range
of machines that are specifically designed to save even more water and energy. The key to this
range is the diaphragm filtration systems that allow water, valuable materials and waste energy to
be recovered.
Global Water And Energy Shortages
In the future, water is set to become an increasingly scarce and therefore extremely
valuable resource. Demand for water is growing at more than twice the rate at which the world’s
population is growing. Over the past 100 years, the world’s population has increased threefold,
while water consumption has risen by a factor of seven. Since 1970, the available amount of water
per capita has been reduced by 40 percent as a result.
It takes approximately 2,500 to 3,000 liters of water to manufacture a single cotton shirt.
The bulk of this water is required to grow the cotton, followed in second place by the wet
finishing process. The first consequences of water shortages and wastewater problems are already
starting to be felt in the textile finishing industry. For example, new companies in China and
India have not been granted approval to set up operations if they have not been able to present a
convincing case to the authorities that their approach will help solve issues of water consumption
and wastewater. In Europe, companies face closure for the same reason. Textile centers in Asia are
reporting rapidly dwindling groundwater reservoirs and heavily salinated groundwater. As a result,
many companies face challenges that threaten their very existence.
Holistic Solutions
The global textile industry faces a new challenge. As a consequence of global energy and
water shortages, the industry now needs environmentally friendly production methods. In the
mid-1990s, Benninger began moving away from its conventional role of machine builder, and has since
established itself as a supplier of wet finishing equipment for woven fabrics and knitwear. Now the
company for the first time is offering holistic textile finishing solutions under the banner of
resource management. These solutions stand for sustainable textile production that is both
ecologically sound and ethical. Part of this approach involves adopting a more careful attitude to
the use of water, energy and chemicals.
In addition to finishing machines, Benninger supplies the matching diaphragm filtration
systems
(See Figure 1). These systems can be equipped with a number of functions that enable the
following processes:
• separation of water from the contaminants introduced by the process,
with subsequent recycling, whereby the contaminants are concentrated to the point where no liquid
waste is generated — zero discharge — and at least 80 percent of the wastewater is reused as
process water;
• recovery of recyclable materials, such as size and caustic soda, from
the wastewater and reuse of these materials in the process; and
• recovery of thermal energy.
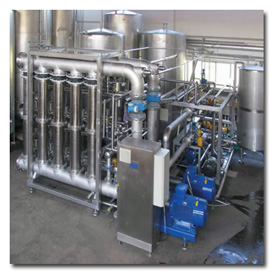
Figure 1: This ultrafiltration plant, featuring a diaphragm filtration system, was designed
for use in the textile industry.
Diaphragm Filtration System
In essence, the multi-stage diaphragm system comprises an ultrafiltration stage and
downstream reverse osmosis stage. The ultrafiltration stage is equipped with a special ceramic
diaphragm that is used to hold back particulates and long-chain organic wastewater components at
temperatures of up to 95°C. In the reverse osmosis diaphragm that follows, the dissolved dyestuffs
and salts are almost completely separated from the water. Afterwards, the process water can be
reused directly in all areas of the textile finishing plant without adversely affecting the quality
of the end product.
Although this method has long been used in the foodstuffs and pharmaceuticals industries, it
is only thanks to the use of back-flushable ceramic diaphragms, which are resistant to chemicals
and high temperatures, that this technique can now be applied in the textile industry. With the aid
of ultrafiltration, it is possible to protect the reverse-osmosis stage effectively against
contamination and thus ensure the operational reliability of the system.
Using a combination of ultrafiltration and reverse osmosis, a recovery rate in excess of 80
percent of the treated wastewater can be achieved. After processing with the diaphragm filtration
system, the recycled process wastewater is colorless and can have chemical oxygen demand (COD)
values of between 100 and 300 milligrams per liter and a conductivity of around 100 microSiemens
per centimeter.
In order to optimize the way the system operates as a whole, Benninger has fine-tuned the
design of the diaphragm systems to match the composition of the textile wastewater and the
contaminant loads
(See Table 1).
In resource management, the first step is always to optimize textile processes. In textile
finishing, there are still many ways of doing this, including:
• continuous dyeing instead of the obsolete method of exhaust dyeing;
• high-performance washing units instead of simple washing units;
• optimization of liquor flows with counter-flow and partial-flow water
guidance; and
• freshwater feed according to the level of contamination.
Only after the process has been optimized is a mass balance calculated as the basis for
designing a diaphragm system.
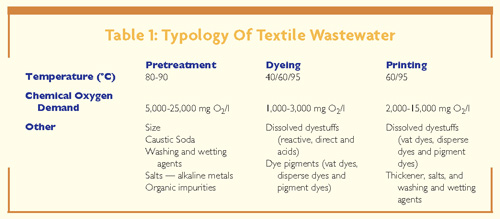
Wastewater-Free Textile Finishing Plant
Following are the most important results from a case study performed to understand how a
traditional finishing plant performs, and what can be achieved through modernization.
Desizing
Desizing wastewater carries an extremely high COD load. At the same time, recyclable
materials can be recovered by using water-soluble size. To do this, an ultrafiltration plant with
temperature- and chemical-resistant ceramic diaphragms is required. The results are as follows:
water recycling, 85 to 90 percent; size recycling, 75 to 85 percent; and heat recovery, 70 percent.
Bleaching And Scouring
Wastewater from cotton bleaching has a high COD value due to the organic substances that
accompany the cotton. This water also usually is yellow, so a combination of ultrafiltration
followed by reverse osmosis is needed in order to neutralize the color. The concentrate cannot be
reused. It is subsequently concentrated even further and processed into solids or burned. At this
stage, the results are highly impressive: water recycling, 80 to 90 percent; heat recovery, 70
percent.
Mercerizing
The mercerizing process generates wash water with a high concentration of caustic soda —a
round 60 grams per liter (g/l). Ultrafiltration is used initially to clean and concentrate the
caustic soda in the wash water and reduce its volume. Afterwards, the caustic soda is concentrated
to 35 to 42 g/l by using conventional evaporation methods, which allows the caustic soda to be
reused in the mercerizing plant. As the conventional evaporation methods used are very
energy-intensive, this is a good approach to concentrate the wash water beforehand via
ultrafiltration. The potential savings after this step are high: caustic soda recycling, 75 to 80
percent; water recycling, 80 to 85 percent; heat recovery, 70 percent.
Dyeing
Wastewater from the dyeing process has a high coloration and a high content of electrolytes,
so a combination of ultrafiltration and reverse osmosis is required. The results achieved here are:
water recycling, 80-90 percent; heat recovery, 70 percent. Figure 3 shows wastewater from dyeing
processes that has been treated in diaphragm systems.
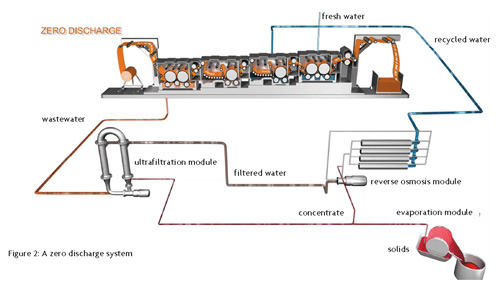
Figure 2: A zero discharge system
Processing The Concentrates
As described above, the concentrates generated in diaphragm systems can be reused only for
size recycling and caustic soda recovery. In all other cases, the concentrates are highly
contaminated liquors. It is not possible to discharge these concentrates into rivers or lakes. For
wastewater-free operation of the plant, all concentrates must be thickened and solidified. The
thickened concentrates can be further solidified using evaporation techniques, for example, or they
can be burned.
Potential solutions for knitwear finishing plants are based on the same principle as those
used for woven fabric finishing with no desizing. However, a lot more needs to be done to ensure
the methods used in knitwear finishing can catch up, particularly as the plants often use exhaust
processes in jets or softflow machines. The associated water and power consumption is two to three
times higher than a more modern open-width finishing system.
Operating Costs
Diaphragm filtration plants run automatically. All of the relevant operating parameters —
such as temperature, flow rate and operating pressure — are controlled via PLC. Back-flushing
processes and cleaning processes are started automatically.
The initial investment for ceramic diaphragms is higher than for polymer diaphragms. Thanks
to their high temperature resistance and chemical resistance, their lifetime is between five and 10
years. Conventional polymer diaphragms are used in the reverse osmosis stage, and these have a
lifetime of two to three years. The operating costs for a two-stage diaphragm system are around
0.60 euros (US$0.90) per cubic meter, which includes both the initial investment costs and the
running costs of the plant. The amortization period for a diaphragm system for textile wastewater
is around two to three years for water recycling and heat recovery. If the system also is used to
recycle size and recover caustic soda, the amortization period is around one to two years.
However, rising energy costs and the increased shortage of water will significantly reduce
the amortization period in the future.
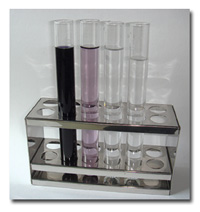
Figure 3: Samples of dye-process wastewater treated in diaphragm filtration systems.
1 = Wash water
2 = Filtrate from the ultrafiltration stage
3 = Permeate from the reverse osmosis stage
4 = Fresh water, for comparison
Solutions For Emissions Reduction
There is no getting away from the image of textile finishing as a major contributor to
emissions. Even in the long term, it is not going to be possible to replace wet chemical methods
with physical finishing methods. This is reason enough to start looking for ways to reduce
emissions.
Passive protection options against emissions include: process changes such as continuous
dyeing instead of jet treatments; optimization of existing processes and recipes; and the use of
highly efficient washing and finishing technologies.
The list of active protection options against emissions includes the use of filtration
technology to recover water, energy and recyclable materials from the wastewater of wet finishing
plants. For the first time, the ceramic diaphragms used in the ultrafiltration stage enable
reliable and continuous operation for the treatment of wastewater from textile finishing processes.
At the same time, they also act as a protective buffer for the downstream reverse osmosis stage,
which is used for filtration of dissolved dyestuffs and electrolytes. In addition to the recovery
of water, energy and recyclable materials, the use of an evaporator and an evaporation plant makes
it possible to run textile finishing plants that generate no wastewater at all.
Editor’s Note: Jürgen Ströhle, Benninger AG, and Dr. Dieter Böttger, MDS Prozesstechnik GmbH,
contributed to this report.
March/April 2008