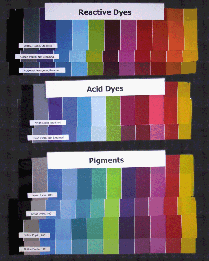
With the growth of the digital textile printing market has come a dizzying array of process
components, each of which individually and collectively will affect the results. Digital textile
printing output is a reflection of the design and color management software, RIP (raster image
processing software that provides the interface between the design software and the printer), the
printer, the printing environment, the ink, the fabric, the pre-treatment, the post-treatment and
last, but not least, the operator.With so many variables to evaluate, many of which are subjective,
how does one review digital printing output with the goal of finding the right printer or service
bureau This was but one of many questions answered in “A Realistic Guide to Digital Printing,”
presented during the CItdA 2000 NY Symposium offered at the CADExpo in New York City. In
preparation for the symposium, Alison Hardy of FabriCAD submitted test files to a number of service
bureaus, as well as hardware, software and media vendors. The vendors pro-vided several vari-ations
of output, each with a dif-ferent ink, medium, fabric treatment, hardware, software and RIP. While
the 181 resulting printed swatches paint a revealing arrangement of print designs, they are
meaningless without parameters against which to measure the results. Defining ParametersStep
number one in evaluating digital printing output is to define the parameters of the job. Issues to
be considered include the type of graphics being printed and the specification of colors to be
matched. The colors to be matched should be defined up front in conjunction with the
color-definition profile, be it swatches, process color (RGB or CMYK), spot color, L*a*b* or L*C*h,
or a digital color system such as those available from companies like Pantone, Datacolor or
GretagMacbeth. Another important parameter to be considered is the intended use for the printed
fabric. Is your output in-tended for storyboarding, sampling, trade-show displays, flags and
banners, or production Does it need to be flame-retardant The answers will determine the type of
fabric and inks to be used and determine what, if any, pre- and post-fabric treatments are
required.The industry segment for which the printed fabric will be used is an important
consideration. For example, in a review of test files of floral prints, some showed the colors
brilliantly, while others reflected more muted tones. There is no right or wrong, good or bad
result when taking market segments into consideration. Depending on the final use of these florals,
any of the results might be acceptable. Its a subjective decision.Ironically, it is the freedom of
this subjectivity that has created the greatest limitations and barriers to entry for this new
technology. The traditional industry still looks at digital textile printing parameters from the
context of what it “cant do,” compared to analog printing. According to industry veterans, the
technology is too slow and cant be used for production. They argue that process color printers dont
have enough of a color gamut, digital printing is too expensive, post processing is a pain, and the
fabrics are too limiting.For a much smaller group of designers, textile artists, fine artists,
costumers, wide-format printers and the like, this technology is much more about what it “can do”
to provide products and services the market has never before seen. For these people, textile
printing offers parameters not available with analog printing unlimited repeat size, tonal
graphics, engineered designs that cross several seam lines, quicker samples, customization and
short-run production.The traditional textile industry needs to understand that, in the same way the
Internet is not going to replace the television as a form of entertainment or information, this new
digital technology isnt about replacing existing analog processes, but rather about leveraging the
expanded parameters to offer new niche products and services. Distributing And Printing Test
FilesWhether shopping for a service bureau to handle printing, or looking to purchase a printer,
you will want to run test files that reflect the type of graphics to be printed on the appropriate
fabrics. Because software, inks, fabrics and post-treatment all affect color, results will vary.
While all equipment and media vendors will offer sample printed fabrics for review, the best way to
test results is with sample files that reflect the type of designs you plan to print.While most
software applications provide color charts that can be printed to test color selections on various
substrates, there are shortcomings to consider. These charts were developed for printing on
commercial paper, which has a much more consistent surface than textiles. In addition, these charts
represent only flat color, not the tonal colors that are an advantage of digital printing. If you
are using color charts to test colors for proofing on a digital printer, it is important to keep in
mind these colors will change when they are rotary screen-printed for production. Getting 40MB
files (or larger) to potential vendors can be a project in itself. While Hardy used zip disks,
several disks ruined in transit caused her to believe that writing the files to a CD-ROM would have
been more reliable.The ideal solution is an ftp site from which prospective vendors could download
the files directly. Files should be in a TIFF format, the established industry standard for image
files. Be sure to provide information on the parameters of the job. Evaluating OutputThe
final and most difficult part of the process lies in the evaluation of the printed results. How do
you compare product that, by virtue of strategic alliances between the software, hardware, ink and
fabric vendors, is likely the result of variables difficult to manage and evaluate.As a baseline,
you should start with the standard textile evaluation attributes of hand, wicking and performance.
If colorfastness, lightfastness and crocking are on your list of parameters, then be sure your
evaluation fabric has received the post-treatment required to give it these attributes.To evaluate
the actual image on the fabric, it is necessary to check the dots, lines and solid areas
(See Table 1).Once this evaluation has been made, quality “bins” can be established that
will categorize output as to its acceptability for production, marketing, concept or reference.
Table 2 shows a sample chart one might develop, using any choice of scales (i.e. 1-10, A-Z,
low/medium/ high, etc).As a part of the evaluation process, it is important to determine the
quality observation points based upon the relevance to the product. Here again, you want to
identify the parameters critical to your particular designs. These parameters may include the
intensity of black, the line quality for images with straight lines or text, and the smoothness of
color in solids. Watch for bleeding or drifting, check for dithering (which is most noticeably
found in neutrals and pastels), and check the quality of the color space by observing if design
elements such as subtle shade change steps are noticeable.On the subject of color, it is important
to control the environment in which you are checking color. Keep in mind that color changes with
the light source, so if you are checking color in an office setting, colors will appear differently
than when viewed in natural light. It is also important to be aware of the distinctions between
spot color and process color, with spot color being a pure pigment, and process color being a
combination of several different inks. Process color, the technology most often found in digital
printers, is a combination of cyan, magenta, yellow and black, though some of the newer printers
allow for process printing with up to 12 colors.Process colors, by being a combination of inks, do
not always have the clarity or brightness achieved when using spot colors. There is also a smaller
gamut of colors that can be achieved through process color. On the plus side, process color can
achieve tonal variations that are not possible with the use of spot color.
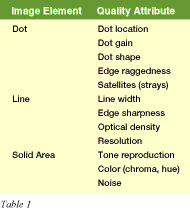
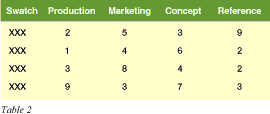
It’s SubjectiveDespite all of the research, development and technology behind digital
textile printing, in the final analysis, the evaluation of results is very subjective. Results
using a particular fabric, ink and medium may be fine for one company, market or end-use, but they
may not be satisfactory for another. The key is in defining parameters and objectives, be they for
concept, sampling, marketing or production.Because the technology is changing rapidly, so, too, are
the results. Dont assume that what couldnt be achieved last year isnt possible today. Keep in mind
the color results you see may not be the best possible. “Its all about the people operating the
machines,” states Hardy. “The designers, and not the machine operators, will be much better at
obtaining the desired results their subjective results. What you see isnt as good as you are going
to get if you tweak the colors yourself,” she adds.
Editors Note: Teri Ross is a writer, speaker and consultant focusing on CAD/CAM technology and
process improvement strategies for the sewn products industries. She is owner and president of
Imagine That! Consulting Group, publishers of the award-winning techexchange.com. She can be
reached at tross@techexchange.com or at (952) 593-0776.
October 2000