Beyond 2000: Weaving PrepBy Dr. Sabit Adanur Weaving Speeds Up
From winding to automatic drawing-in, weaving preparation is becoming even more critical.
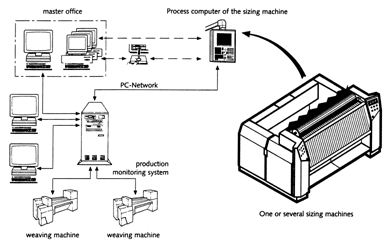
With ever-increasing weaving speeds, the requirements on weaving preparation are also getting
more stringent. The filling yarns are not subjected to the same type of stresses as are the warp
yarns and thus are easily prepared for the weaving process. Depending on the spinning method, the
filling yarns may not be prepared at all, but rather taken straight off the spinning process and
transported to the weaving process. Winding is the major preparation process for filling yarn. Warp
preparation includes winding, warping, slashing and drawing-in or tying-in.The cost to repair a
yarn failure is much less if it occurs prior to the weaving process. In addition, a yarn failure
during weaving also increases the chances for off-quality fabric. Many if not most of the quality
problems encountered during fabric forming are directly related to mistakes made during yarn
manufacturing or yarn preparation for weaving. These facts show the importance of weaving
preparation. Winding Winding produces a yarn package that is suitable for further processing. The
amount of yarn on several small spinners packages are combined by splicing or knotting onto a
single package. Knotting has been replaced by splicing in modern winding machines. The winding
process provides an opportunity to clear yarn defects. Thin and thick places, slubs, neps or loose
fibers on the yarn are cleared during winding and thus the overall quality of the yarn is
improved.The increasing use of newer spinning technologies resulted in a situation where the old
concept of yarn clearing and package quality now has become a part of the spinning process rather
than part of a separate winding process. Properly formed packages of defect-free spun yarn are an
even more critical factor. Package considerations include condition of the package core, the proper
provision of yarn transfer tails, properly formed splices or knots, elimination of internal defects
such as slubs, sloughs, tangles, wild yarn, scuffs and ribbon wind, elimination of external defects
such as over-end winding, cob webs, abrasion scuffs, poor package shape or build, proper density
(hardness) and unwindability.The clearers of todays technology are more sophisticated and contain
electronics that continuously monitor the yarn to detect thin and thick places. The latest yarn
clearing systems can also detect foreign fibers. Then these fibers are classified and eliminated
during the winding process. As a result, the quality of the yarn can be improved during the winding
process. Todays winding machines allow use of different size bobbins with different flange
diameters, overall lengths and winding widths on the same machine. For winding of industrial yarns
such as aramid, carbon or glass yarns and monofilaments, specially designed yarn guide elements are
used. A spindle speed of 5,000 rpm is possible.In precision winding, the position of the yarn as it
is laid on the package is controlled very precisely to increase the density of the package. With
the electronic system, freely programmable package build is possible.WarpingThe preparation of warp
yarn is more demanding and complicated than that of the filling yarn. Modern weaving machines have
placed increased demands on warp preparation due to faster weaving speeds and the use of insertion
devices other than the shuttle. Warp yarn must have uniform properties with sufficient strength to
withstand stress and frictional abrasion during weaving. The number of knots should be kept to a
minimum. The knots should be standard type and size so they fit through the heddle eyes and reed
dents. Size agent must be applied uniformly on the surface of the yarn. The yarns on the warp sheet
must be parallel to each other with equal tension.Todays warping machines can process all kinds of
materials including coarse and fine filament and staple yarns, monofilaments, textured and smooth
yarns, silk and other synthetic yarns such as glass. Usually a static eliminator device is
recommended for yarns that can generate static electricity. With todays computerized sectional
warping systems, once the basic style information is entered, the computer automatically calculates
the number of sections on the beam and width of each section, carrier lateral movement speed and
automatic positioning of each section start point, automatic stops for leasing and calculation of
the correct feed speed irrespective of the material and warp density.The computer can also monitor
the automatic stops for predetermined length, operating speed regulation of +/- 0.5 percent between
warping and beaming, beaming traverse motion and memory of yarn breakage during warping for
beaming.Other typical features of a modern sectional warper are:
- feeler roller to apply material specific pressure to obtain exactcylindrical warp
build-up; - lease and sizing band magazines
- constant warp tension over the full warp width;
- automatic section positioning with photo-optical section width measurement;
- pneumatic stop brakes;
- warp tension regulation for uniform build-up; and
- automatic warp beam loading, doffing and chucking.Todays headstocks are equipped with advanced
design features such as precision direct drive, advanced electronics, smooth doffing and
programmable breaking. Automatic hydraulic doffing is accomplished with the operation of one
button. Programmable pneumatic braking provides a constant stopping distance regardless of the
operating speed or beam diameter. The length of the yarn wound on the beam is controlled with a
measuring roller and counter device. The density of the yarn can be controlled by tension, pressure
or both. Frictional drive usually results in higher yarn density. In spindle drive, yarn tension
and a hydraulically activated pressure roller are used to control density. Some headstocks are
designed to run more than one beam width. Manual cutting and knotting takes an average of 8
seconds. For a 640-package creel, it takes 85 minutes for one person to complete the whole creel.
In modern machines, yarn cutting and knotting are done automatically. In an eight-tier creel,
automatic knotting and cutting device requires an average 2 seconds per package which totals 21
minutes for the whole creel. The automatic knotting and cutting devices are mounted on rails that
are integrated in the creel. There are as many cutting heads as there are tiers. The devices are
controlled by a PLC (programmable logical controller). Each package row is approached exactly at
traverse/creep speed by means of two proximity initiators. The oscillating suction and gripping
tubes offer the yarn ends to the knotting heads, where they are knotted and trimmed. The tails are
removed by suction. The current trend in weaving is towards larger warp beam diameters. Today,
weaving beams of 1,600 mm diameter are possible. SlashingThe ultimate goal of sizing is to
eliminate or reduce warp breaks during weaving. Warp breaks are caused either by high tension or by
low strength in the yarn. High tensions in the warp are caused by large shed openings, lack of
proper tension compensation, high beat-up force and inadequate let-off. Knots, yarn entanglement
and high friction also cause tension build-up. Slasher creel tension control is critical especially
with Murata jet-spun (MJS) and open-end yarns. Maximum tension should not exceed 5 percent of
breaking strength (15 to 20 grams (g) for ring-spun yarns and 12 to 15 g for open-end, MJS and MVS
yarns). With coarse yarns, sometimes 30 g is allowable. The amount of size picked up is affected by
the viscosity of the size mix as well as the yarn structure. The viscosity of the mix is controlled
by the recipe, amount of solid content in the size liquor and the type of sizing product,
mechanical mixing level, temperature and time of boiling. Flat filaments, textured and spun yarns
pick-up size differently. The critical parameters to watch in the sizing process are size
homogeneity, constant speed of the sizing machine, constant size concentrations and viscosity.
Flooding or dry zones should be prevented in the size box. Temperature of the size box is important
for proper size pick-up. For 100-percent polyvinyl alcohol (PVA) sizing, a temperature of 160° to
170°F is recommended.Todays modern sizing machines dynamically adjust the degree of sizing. Expert
software packages calculate sizing values on-line as a function of the warp weight. Size
application measuring and control systems are used to measure and calculate sizing parameters
automatically instead of time-consuming laboratory test procedures. Based on the calculated
parameters, the squeezing pressure at creep and normal speed is controlled via computer. A
byrometer measures the density of the mix and controls the supply rate of the ingredients. The
purpose is to keep the warp sizing degree constant.High-speed weaving machines require minimum
hairiness in warp yarns. During slashing, yarn hairiness is affected mainly by the spacing between
adjacent yarn ends in the size box and the slasher dryer configuration. In practice, the size box
occupation may be used to determine yarn spacing. The Teflon® coating on all of the dryer cans
should be in good shape to prevent dry can sticking (also called shedding) which may be a problem.
Since open-end and MJS yarns have high wet pick-ups, the slasher may have to be slowed down to
eliminate dry can sticking. Selection of a sizing machine depends on several factors including warp
specifications, weaving requirements and production volume. The output of the sizing machine is
determined by the size of the dryer.In so-called “walk-through head-end” beam winder, the beam
support/drive unit is independent of the delivery/comb unit. There is a “walk-through” platform in
between, which allows better access to the comb, delivery roll and beam. Automatic hydraulic beam
loading and unloading, independent hydraulically lifted delivery nip rolls, pneumatically operated
expansion, contracting and shifting of the comb are some of the other features of this new system.
This concept was developed for large warp beams. The quality of woven fabrics depends to a great
extent on the quality of warp preparation. Therefore, sizing machines are usually incorporated in
weaving room control and monitoring systems as shown in Figure 1. For trouble-free weaving, a
well-slashed warp is a must. Poor slashing may increase loom stops, which in return increases the
cost of weaving.Chemistry For SizingWith all the ingredients available, a size mix can get quite complex.
Several factors should be considered when choosing the size mixture:- yarn material (cotton, poly/cotton, polyester, rayon, wool, etc.);
- yarn hairiness;
- yarn structure (ring-spun, open-end, jet-spun);
- water used for cooking (recycled or fresh);
- type and speed of weaving machines to be used (projectile, rapier, airjet, waterjet);
- percent add-on (and percent solids) required;
- yarn occupation in the size box and on the dry cans;
- desizing procedures;
- reclamation of size and use of enzymes in the finishing plant;
- slasher design and number of size boxes; and
- environmental restrictions.
- The type
of weaving machine should also be considered for choosing the sizing material. Since sizing is not
a value-added process, minimizing the cost of sizing is extremely important. However, this should
not be done by using cheap size materials at the expense of productivity and performance in the
weave room. The ultimate goal is to optimize weaving performance with the cost of sizing. Cold
Sizing In this process, the warp surface is treated gently without squeezing. It is claimed that in
comparison to waxing on the sectional warper, cold sizing produces better yarn compaction, smoother
surface and less hairiness, which improves the weaving efficiency. Cold size products from the
suppliers can be used for cold sizing of single yarn, siro yarns and two-ply yarns of wool and
blends, terry warps and synthetic yarns. The chemical products used are water soluble, recyclable
and biologically degradable. The main advantages of this system have been reported to be less
liquor pick-up and high liquor concentration, 30 to 50 percent less application compared to normal
sizing, savings in energy in drying, less machine space and higher modularity and
productivity.Prewet Sizing TechnologyIn another recent development, called prewet sizing
technology, the yarns are wetted and washed with hot water prior to entering the size box. It is
claimed that by doing this, the size add-on can be reduced by 20 to 40 percent, size adhesion is
improved, abrasion resistance is increased and hairiness is reduced. Figure 2 shows the schematic
of the pre-wetting process. The improvement in weaving performance is attributed to better
encapsulation of the yarn by the sizing agent and better adhesion of the sizing agent to the yarn.
The advantages of this system are an increase in tensile strength and abrasion resistance,
reduction in hairiness, clinging tendency reduction and reduction in lint formation during
weaving.Drawing-in and Tying-inToday, the drawing-in and tying-in processes are fully automated.
Drawing-in is done using robot-like machines. A special type of heddle is needed for automated
drawing-in. The warp ends, taken from the warp sheet, are fed individually to the drawing-in
element. Heddles are separated from the stack and brought to the drawing-in position. A plastic
knife opens a gap in the reed, and a hook draws-in the warp end through the heddle and reed in one
step.Automatic drawing-in increases speed, flexibility and quality in weaving preparation compared
to manual drawing-in. A drawing rate of 50,000 warp ends per 8 hours (200 ends per minute) is
possible.A small portable robot is used on or off the weaving machine for tying-in. A typical
warp-tying machine can knot single or ply yarns from 1.7 to 80 Ne (340-7 tex). They can knot
cotton, wool, synthetic and blend warp yarns. Yarns of different thicknesses can be knotted.
Typical knotting speed of a knotter is from 60 to 600 knots per minute. With continuous filaments
and bulky yarns, a non-slip double knot is recommended which can be handled by knotting machines.
Some automatic tying machines can knot extremely short tails of yarns, 5 mm. Tape yarns and
monofilaments require a slightly different tying machine. Tape yarns of up to 8-mm width can be
tied. The knotting speed is typically 60 to 450 knots per minute. The number of warp ends to be
tied together can be preprogrammed; once this number is reached, the knotter stops automatically.
Dual knotting system is used on a double-beam weaving machine. The knotters work from left to right
and from right to left simultaneously. Several points should be considered during drawing-in and
tying-in. Improper splicing and/or knotting can become critical to good weaving performance. The
straightness of individual warp yarns and their freedom to act independently as they pass through a
weaving machine is important to good weaving performance. Yarns that are crossed and tangled can
not proceed without excessive stress and yarns that are restricted or influenced by drop-wire
activity, heddle spacing, harness interference or reed spacing will not weave at top
performance.
Editors Note: Dr. Sabit Adanur is an Alumni Professor for Auburn Universitys Department of
Textile Engineering. He has written for a number of publications and is the author of the
Wellington Sears Handbook of Industrial Textiles.
May 2000