AACHEN, Germany — APRIL 11, 2024 — At Techtextil in Frankfurt, Germany, the ITA Group will be presenting its entire range of research on sustainability and recycling at the Elmatex joint stand in Hall 12.0 D63 from April 23-26, 2024:
- The BIOTEXFUTURE innovation area is gaining speed and is presenting most of the exhibition items at its own stand and at the stand of ITA Institut für Textiltechnik of RWTH Aachen University. Specifically, these are the projects BIOBASE, BIOTURF, CO2TEX, DEGRATEX and LIGHTLINING projects.
- BIOTURF, CO2TEX and BIOBASE will also be presented at the joint bioeconomy stand of the Federal Ministry of Education and Research (BMBF) in Hall 2, Stand A35, at the Hannover Messe (22-26 April 2024) in Hannover, Germany, which is taking place at the same time.
- ITA will also be presenting a more wear-resistant hemp polishing disc at Techtextil in Frankfurt am Main.
- The Recycling Atelier ITA Augsburg gGmbH presents its core competence as the first model factory for mechanical textile recycling.
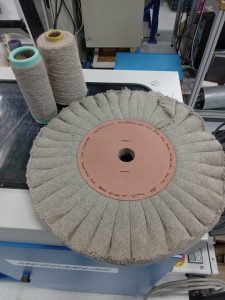
Please find below a brief overview of the individual exhibits:
- BIOBASE – Interior textiles made from biopolymers
As part of the BIOBASE project, funded by the Federal Ministry of Education and Research, interior textiles made from biopolymers have been developed together with Krall+Roth Produktions GmbH. In order to investigate the substitution potential of different biopolymers, an established, petroleum-based product is being modelled with polymers based on renewable raw materials. Therefore, commercially available bio-based polymers have been selected, melt-spun into filament yarns, then air-texturised and further processed into fabrics. The manufacturing processes and machine settings along the textile value chain had to be adapted to the respective material behaviour of the biopolymers. Using this process, fabrics made from four different (partially) bio-based polyamides were successfully realised for the interior sector. Please find further information here – https://biotexfuture.info/projects/biobase/
- BIOTURF – Bio-based artificial turf without microplastic granulate infill
The aim is to develop an artificial turf structure made of bio-polyethylene (PE) that does not differ chemically from petroleum-based PE in terms of its essential properties. The mono-material structure should enable high-quality material recycling – an important starting point for the subsequent recycling of the product. In addition, the new artificial turf structure will not require the addition of infill granules, thus solving the current microplastic problem of artificial turf pitches. Please find more information here – https://biotexfuture.info/projects/biobase/
- CO2TEX – Lifestyle compression stocking with TPU yarns that contain CO2, among other things
Elasticity is the ability of a textile to stretch or recover when required. This has a direct effect on functionality. Currently, elasticity in textiles is almost exclusively provided by so-called “elastanes”.
Elastanes are elastic filament yarns that are usually made from fossil-based elastomeric polyurethanes. The estimated production volume is around 1.22 million tonnes per year. The elastomeric character requires the use of dry spinning technologies for yarn production, which leads to challenges such as low production speeds and therefore comparatively expensive yarns.
In addition, potentially hazardous and environmentally harmful solvents must be used – an appropriate occupational safety concept is therefore essential. At the end of the product life cycle, dry-spun elastanes impair recycling because the individual components of the textile cannot be separated with technically and economically justifiable effort.These challenges can be solved by using elastic, bio-based or CO2-containing TPU filament yarns.
In the CO2Tex project, TPU yarns were developed on industrial melt spinning systems using polymers with a renewable content of up to 18 per cent by weight. With elongations of up to 600 per cent, diverse and innovative applications can be developed, such as the lifestyle compression stocking exhibited here – https://biotexfuture.info/projects/co2tex/
- DEGRATEX: Degradable geotextiles
The aim of DEGRATEX is to develop bio-based, degradable solutions for geotextiles for short-term applications such as the temporary stabilisation of earth structures or vegetation protection. The materials fulfil their function until they can be taken over by natural components such as soil-stabilising or ground-covering plants.
As part of the project, various materials and textile structures for these applications are being researched and the effects of the degradation process on the surrounding environment are being scientifically assessed. In addition, the project aims to develop assessment and decision-making tools for the use of degradable geotextiles. The results will make it possible to replace conventional geotextiles with bio-based and degradable product solutions within a technically and ecologically sensible framework. In this way, material structures can be used resource-efficiently in applications, provide added value from a technical and functional point of view and reduce the use of petrochemical plastics for use in nature. Please find more information here – https://biotexfuture.info/projects/degratex/
- Hemp polishing disc
Currently, polishing discs are generally made of cotton, for more abrasive polishing processes they are made of sisal, for example. For ecological reasons, the cotton polishing disc will be replaced by a more wear-resistant hemp polishing disc. For this purpose, cotonised – i.e. cotton-like – hemp is used. The wear resistance is ensured by a stronger material removal behaviour, which polishes the components faster. This saves time in the polishing process and therefore money. Please find more information here – https://www.ita.rwth-aachen.de/cms/ita/das-institut/aktuelle-veranstaltungen/ita-auf-der-techtextil/~bgdaxr/hanfpolierscheibe/?lidx=1
- LIGHT LINING – Aerogel fibres and textiles
The ITA has succeeded in developing a cost-effective and industrially scalable manufacturing process for insulating textiles made from 100 percent aerogel fibres. Cellulose aerogel textiles are not only sustainable, but also very flexible and drapable compared to conventionally rigid or brittle aerogel products, which means that they can also be processed on conventional textile machines. The development at ITA promises a new, globally unique, sustainable, highly efficient insulation material that combines the advantages of textiles (flexibility & good processability) with those of aerogels (very low weight & very good thermal insulation). Please find further information here – https://biotexfuture.info/projects/lightlining/
Recycling Atelier ITA Augsburg gGmbH
The Recycling Atelier is a centre for research and development along the entire textile production chain for textile recycling. The bundling of the most important processes enables holistic and comprehensive research that has not existed in this form to date. Together, the partner network is looking for answers to the scarcely practised textile recycling and the missing triad of technical meaningfulness (downcycling), economic benefit (lack of profitability) and ecological meaningfulness (CO2 footprint).
Under the title “Walk4Recycling”, the Recycling Atelier now presents products made from post-consumer recycled materials. A new flat-knit jumper, teddy bears and a fleece bag have been produced from used textiles (worn knitwear) with the help of the strong partner network. The ring yarn used for the jumper consists of 65 per cent recycled cotton and 35 per cent new polyester. This high proportion of post-consumer recycled material is an innovation for a ring-spun yarn of this fineness, as today mainly coarse rotor yarns for lower-quality textiles are spun from these materials. The dyeing and decolouring process, which is essential for the fashionable reuse of textiles, is demonstrated using the teddy bear as an example. The non-woven bag shows the potential to close further circles. The fibre remnants from the ring yarn production of the jumper and teddy were collected for this purpose. The fibre remnants were processed with regranulated LooPET fibres to create a nonwoven fabric. This gives the cotton fibres a further life cycle.
Come and see us – we look forward to your visit
Posted: April 11, 2024
Source: ITA – Institut für Textiltechnik of RWTH Aachen University