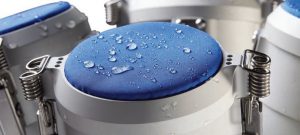
Water repellency testing helps retailers and manufacturers meet and exceed consumer’s comfort and performance expectations in outdoor apparel.
By Paul Montalto
In 2019, the waterproof, breathable textiles market was valued at $1.7 billion, according to a Market Analysis report. The report further estimates a compound annual growth rate of 6.6 percent over the following six years for that particular market. This trend is driven by a growing awareness of the health benefits of sports and the increased necessity to exercise outdoors. Within this space, water repellent garments have become key performers.
Water repellency describes water beading on the surface of a textile, where the water resists penetrating the fabric. This property often is achieved by combining membranes or coatings with tightly woven fabrics. The benefit of water repellent garments is their breathability. The fabric remains porous making it permeable to air and water vapor, which makes them more comfortable for the wearer. Ultimately, a water repellent garment should offer comfortable protection from intermittent rain.
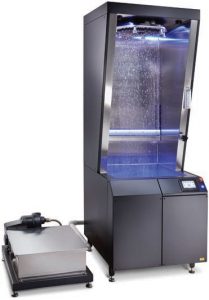
Why Is Water Repellency Important?
Water repellency is important largely because a change in consumer behavior makes it so.
There has been an increased interest in athleisure for many years now. The sportswear industry has influenced mainstream fashion, and innovations in technology have led to improvements in functionality.
For outdoor wear in particular, the onset of a global pandemic increased demand even further. With the long-term closure of gyms, swimming pools and exercise classes, more and more people headed outdoors to exercise. In addition, more people are holidaying in their home country, which for many, means swapping swimwear and shorts for raincoats and walking trousers. With this increase in demand comes more rigorous performance testing to ensure the garments perform as they should when exposed to the elements.
It is also becoming more common to select accessories such as backpacks for their water repellent or waterproof qualities. Another consideration for brands and manufacturers can often involve more feature specific testing to establish, for example, what role seams, zips and pockets play.
Consumers expect comfort from their garments. Comfort is influenced by fit factors as well as fabric properties such as stretch and recovery, and thermal and moisture management properties. But for outdoor wear in particular, comfort is about finding a balance between keeping water out and letting sweat escape.
Risks Involved In Getting The Breathability Of Water Repellent Fabrics Wrong
Safety is arguably the most important feature that users expect from their performance garments. There are risks involved with getting the breathability of water repellent fabrics wrong, mainly that they can trap sweat and cause the wearer to overheat. This might not seem like an issue for a quick walk around the park, but for wearers on long hikes this could cause serious health risks.
To understand the testing that must be performed, it is important to understand the make-up of a garment, and the role that layers play.
In sportswear, and especially outdoor wear, a three-layer clothing system is often advocated, with each layer in the system performing a different function that complements the whole for maximum comfort.
A layering system typically includes:
- A base layer;
- A mid layer; and
- An outer protective shell layer.
An effective outer layer should have a high level of water resistance as well as a high level of water vapor permeability, or breathability. How this layer is constructed plays a significant part in this permeability.
This is where the challenge for the outer layer comes in — creating a fabric that provides good water resistance is relatively simple, but doing so while maintaining breathability is a more complex process because the two properties have an inverse relationship in typical textiles. A thorough testing regime can prove the balance between these properties have been met.
Testing Water Repellency
Water repellency is tested by spray methods, using instruments such as the Bundesmann or Spray Rate Tester, where water is run over the surface of the fabric and the repellency is visually graded.
For the Bundesmann method, in particular testing to ISO 9865, the test instrument generates artificial rainfall to simulate the real life conditions the end garment will be used in. Here, three aspects of water repellency are measured:
- Surface water repellency is visually assessed;
- Resistance to water absorption is evaluated by weighing the specimen; and
- Resistance to water penetration is determined by collecting water that has passed through the sample.
As with any testing, there are certain parts of the process to look out for, which can have an impact on the results.
Pro tips for testing include:
- Clamping the fabric correctly to avoid variance in results;
- Timing is everything – be ready to assess as soon as the test finishes;
- Condition the samples in accordance to the standard;
- Water temperature is important and should be recorded; and
- The Bundesmann must be run for 15 minutes prior to testing to guarantee water flow is consistent.
Sustainability
Traditionally, the Bundesmann test requires a lot of water, which can be an issue for apparel brands and manufacturers who are tackling sustainability issues.
The UN Partnership on Sustainable Fashion found that fashion is responsible for nearly 20 percent of the world’s wastewater, and 10 percent of global carbon emissions, so there is a lot of pressure to be cleaner, more efficient and ultimately sustainable. Although testing plays a small part in the process, there are significant savings to be made in water usage during testing.
James Heal recently conducted a small research project into the efficacy of water recirculation on its Bundesmann testing instrument.
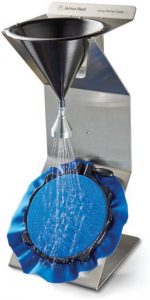
A typical Bundesmann water repellency tester that runs for eight hours per day, five days per week, is consuming 3,360 liters of water. It is plumbed into the mains and drained directly after a single fall onto the specimen. Recirculating the water would reduce usage, but we had to establish there would be no detrimental effects to testing when doing this.
Concerns included:
- If the fabric sheds when being washed — and man-made fabrics in particular shed a lot of microplastics — would this shedded material stay in the water and impact the next round of testing?
- Would the shedded material stick to the next specimen being tested and give a false impression of water repellency for a garment that would then fail when worn?
James Heal conducted significant testing, both in-house and using an external laboratory, to verify that the results would be accurate regardless. The test results concluded that there was consistency from start to end, and by confirming this, the company was able to calculate the savings its recirculation unit could offer, including:
- An eight-hour working day’s use of the James Heal TruRain Bundesmann recirculation system sees 83 percent total cost savings in energy consumption and total running costs.
- There is less waste: 99-percent less water is used during testing alone — 150 tests a week equates to a drop in water consumption from 2,100 liters to just 23 liters.
- Additionally, it is accurate, safe and reliable: Through the use of an effective Water Safety Plan, health and safety can be maintained.
James Heal also found that by using the recirculation unit, it was much easier to maintain the temperature of the water. The percentage of water absorbed by fabrics can increase as the temperature increases, so it is important to control temperature for consistency in results.
Proving Water Repellency
With an increase in demand for water repellent clothing, and the subsequent increase in the popularity of Bundesmann testing, understanding and implementing repeatable testing is crucial to substantiate any claims made about a garment. The challenge for retailers and manufacturers is to meet and exceed consumer’s expectations for comfort and performance, and water repellency is one part of the puzzle for achieving this.
Editor’s Note: Paul Montalto is a Technical Knowledge manager for the Physical Properties Testers Group (PPT Group), an England-based family of brands — James Heal, Mecmesin and Alluris — that design and produce solutions for testing a wide range of physical properties including compression, light fastness, moisture, dry rate, water repellency, abrasion, flammability, and tensile and torque properties.
January/February 2022