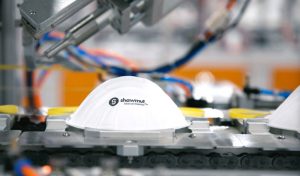
manufactured by Shawmut
No stranger to innovation and change, Shawmut is committed to helping customers rapidly solve pressing business challenges.
TW Special Report
Founded in 1916, West Bridgewater, Mass.-based Shawmut Corp. is no stranger to innovation and change. The fourth-generation, family-run, global company is the largest independent laminator for technical fabrics in the United States, and offers advanced materials solutions for the automotive, health and safety, military and protective, and custom lamination solutions markets. Shawmut employs more than 700 employees worldwide, operating 10 manufacturing plants and seven commercial offices across North America, Europe and Asia.
A History Of Change
What started in the location of America’s oldest woolen mill producing braided fabric and man-made yarn, has transitioned over time into a business that creates a range of soft composite materials and technical textiles, and provides lamination solutions. Throughout the years, Shawmut has supplied diverse products from branded knitted children’s apparel to yarns used by the U.S. military during World War II for parachute shroud lines, knitted blankets, field jackets and bomb parachutes. In the 1950s, the company focused on flame lamination to use with its jersey cloth, a process that continues today. In the mid-1980s, Shawmut relocated to its present West Bridgewater headquarters to focus on product development processes in advanced material technologies.
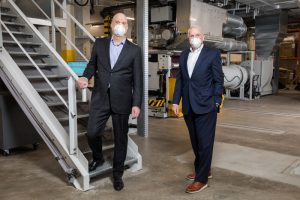
“Since our founding 105 years ago by my grandfather Rudolph Wyner, Shawmut always had the ability to adapt to changing markets and create innovation,” said CEO James Wyner. “Our history gives us a broad materials knowledge and expertise to engineer our own production techniques and capabilities that set us ahead of our competition. Our customers tell us that we can develop solutions to their challenging requests much faster and with higher-quality output than our competition. We embrace what we’ve learned but are always looking to innovate to create better solutions. Our purpose of ‘materials innovations for a better world’ may sound a bit aspirational, but we really do try to apply it to everything we do.”
An Automotive Leader
Shawmut is a global supplier in the automotive market supplying everything from laminated headliners to pillars, roller shades, seating, door and trim laminations, sun visors, package trays and parcel shelves. A few years ago, the automotive headliner and specialty industrial fabrics business of Glen Raven Technical Fabrics (GRTF) merged with Shawmut after an 18-year strategic partnership between the two companies. The merger fully integrated Shawmut’s composite development capabilities and global lamination platform with Glen Raven’s specialty industrial fabrics operation. About the venture, Shawmut said at the time: “Our recent merger with the specialty industrial business unit of Glen Raven Technical Fabrics represents the combining of forces between two longtime partners. We now offer the full suite of automotive interior and industrial solutions, from durable high-performance knit fabrics to flexible multi-layer laminated composites.”
Shawmut recently announced plans to introduce a brand-new customer-focused Technical Center at the Burlington, N.C., Park Avenue facility that houses the merged operations. The Park Avenue Technical Center will offer customers unparalleled access to Shawmut’s advanced design, engineering, and production expertise, multiple quality and testing labs, along with state-of-the-art customer collaboration tools, all under one roof. The development of the Technical Center helps to meet Shawmut’s goal of accelerating the timeline of the finished product with even greater quality production leading to an enhanced experience for the customer. The Park Avenue Technical Center is also the first Shawmut facility to be ISO 14001 certified and is a 100-percent-landfill-free facility meaning that less than 1 percent of the waste that comes out of the facility goes to a landfill. Waste is mainly repurposed and recycled by external sustainability operations.
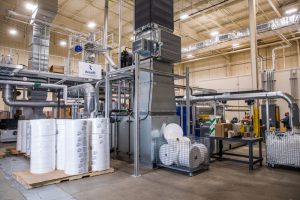
Investing In Health, Safety
In early 2021, Shawmut announced the creation of a new Health & Safety business unit, which was a strategic expansion into markets where Shawmut already had a foothold. According to the company, the new unit, applies “the company’s trademark advanced materials, textile manufacturing, and process innovation techniques to produc[e] high-quality, U.S.-made, health and safety products, including its Protex™ line of U.S.-made personal protective equipment (PPE).”
For decades, the company has produced medical-grade barrier and filtration fabrics, orthopedic medical devices, and certain inflatable medical devices. In the spring of 2020, Shawmut broadened its focus to produce PPE during the COVID-19 pandemic. The company rapidly developed its Protex™ N95 Particulate Respirator, and now also manufactures medical isolation gowns and surgical barrier fabrics. With these additional product lines, the timing was right to bring on board additional personnel with health and safety expertise and launch the new business unit.
“This is a very exciting time in Shawmut Corporation’s 105-year history, as we delve deeper into the healthcare solutions space,” Wyner noted. “We’re making a significant, long-term commitment to developing innovative U.S.-made — and Berry Amendment-compliant — health and safety products not only for this period of great need, but well beyond so that our country never faces a critical PPE shortage again.”
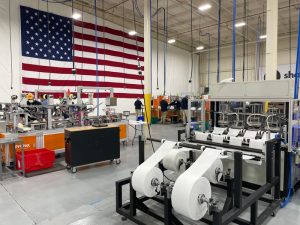
Making Room, Starting Up
According to Shawmut, the company retrofitted nearly 70,000-square-feet of space in its West Bridgewater manufacturing facility to produce isolation gowns and N95 respirators. Shawmut acquired nearly 60 tons of specialized, high-precision meltblown machinery from Germany-based Reifenhauser Reicofil GmbH & Co. KG, which was fast-tracked and shipped on an expedited timeline to the Port of Boston. In addition, Shawmut installed a fully automated and flexible production system to support its N95 particulate respirator line, and installed roughly 50 new assembly lines for gowns and masks, some of which are augmented with advanced robotics capabilities.
The multi-million-dollar investment enables Shawmut to help customers meet demand and rapidly respond to their evolving business needs.
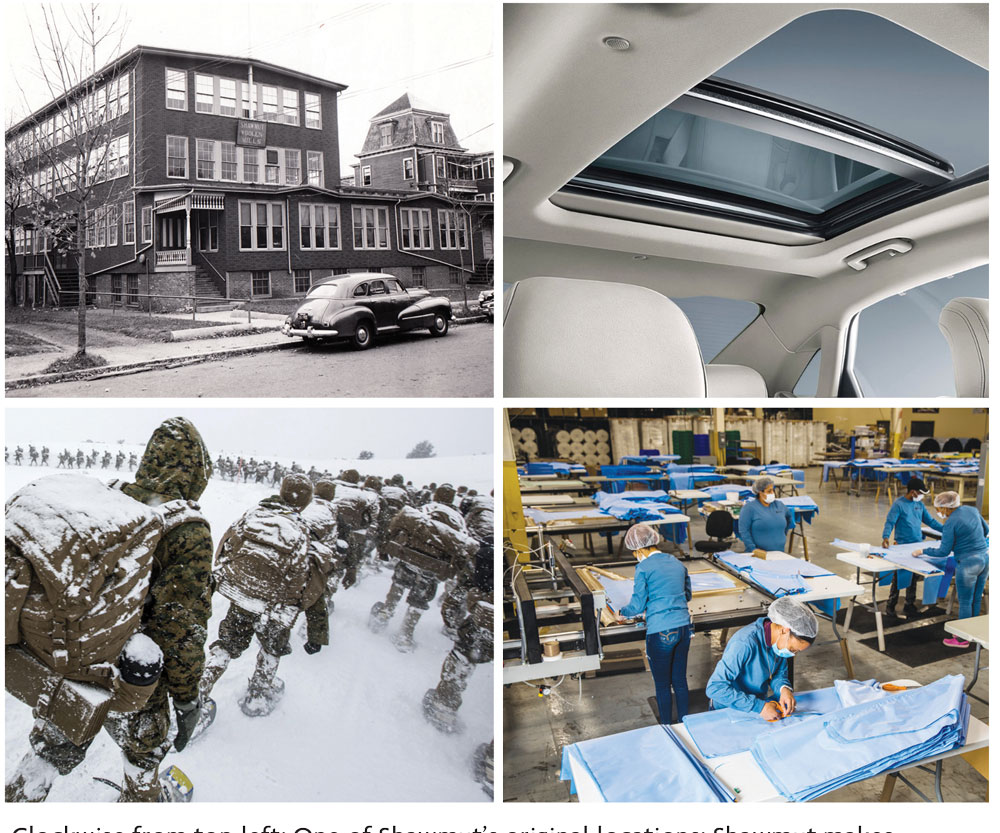
A Military Focus
Most recently, Shawmut announced another strategic expansion with the creation of a new Military & Protective Materials business unit. The unit will produce high-quality, U.S.-made, ultra-high-specification and high-performance technical fabric solutions, many of which will also be Berry Amendment-compliant. Shawmut’s military and protective solutions feature waterproof, windproof, flame-resistant, and chemical and biological protection properties, and are ideal for high-stakes usages required in military and in-the-field professionals who need high-performance gear to safely do their jobs. With new business development leadership on board focused on high-performance materials solutions, the division integrates Shawmut’s textile manufacturing, dyeing, finishing and lamination capabilities to develop game-changing new technologies that will further establish Shawmut as a key player within the high-performance U.S. textile and garment industry.
Providing Protection
Shawmut’s leadership position in lamination technology has resulted in multiple applications in protective gear including products in the high-spec utility workwear market; fire-retardant fabrics area; and chemical, biological, radiological, and nuclear protection markets. Shawmut’s ability to manufacture high moisture vapor transmission laminates provides solutions for firefighters’ gear; surgical gowns; and waterproof, breathable utility and outdoor gear, among other applications. The waterproof, but breathable attributes also extend into products like footwear, military outerwear, as well as boots for hunting, hiking and military use.
Clean Water
Shawmut leverages its advanced process technologies and technical fabric expertise to deliver custom-engineered materials solutions and solve complex challenges. Its global team believes that no challenge is too great, and they have a long history of solving a wide variety of industry needs through dynamic and innovative textile approaches. As an example, Shawmut is part of the worldwide push for innovative textile water filtration technologies as a producer of tricot knit technical fabrics that are used as permeate carriers in salt and brackish water reverse-osmosis filtration processes and systems. Shawmut reports its nonwoven filter fabric is U.S. Food and Drug Administration (FDA)-compliant and certified by the National Sanitation Foundation.
Looking Forward
In this day and age, a fourth-generation, family-run international company is not commonly found, and Shawmut is by no means a common company. Drawing upon more than 100 years of experience in fabric formation and lamination, Shawmut uses materials innovation, engineering expertise, advanced processes, and global supply chain strategies to help rapidly solve customers’ advanced material design challenges, truly distinguishing itself from the conventional New England textile company stereotype. Shawmut’s story is rooted in agile technology application, advanced processes, performance testing, and quality — all while keeping the needs of the customer front and center.
“We’re excited to leverage our expertise in textile engineering, process innovation and commitment to excellence to produce the highest quality materials for the highest performing individuals,” Wyner noted when speaking about the new Military & Protective Materials business unit. This excitement, commitment, and problem solving is at Shawmut’s core.
July/August 2021