P
olytetrafluorethylene (PTFE) is more commonly known by the trade name Teflon®. Consumers
identify the name with cooking pans treated with PTFE to provide non-stick properties. Over the
last 50 years, the fluorocarbon family of polymers has grown to include polymers used in a myriad
of forms and applications ranging from high-temperature filtration and gasketing to surgical
sutures and stain-repellent agents for fabrics.
PTFE is a vinyl polymer, and its structure, if not its behavior, is similar to that of
polyethylene. PTFE is made from the monomer tetrafluoroethylene (TFE) by means of free radical
vinyl polymerization.
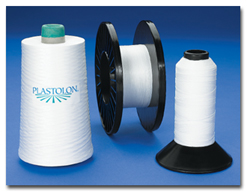
PLASTOLON™ filtration sewing thread from Plastomer Technologies also is suitable for
geotextile sewing and bagging for chemical products.
Discovery And Development Of Teflon®
Fluorocarbons is not a household word, but fluorocarbons have been an important part of
households for many years. In the 1930s, chemists at General Motors and DuPont collaborated on the
development and use of chlorofluorocarbons as refrigerants to replace ammonia, sulfur dioxide and
propane, which were hazardous. The chlorofluorocarbon Freon® gradually became the refrigerant of
choice for the Frigidaire and other household and commercial refrigerators.
In 1936, Roy Plunkett, who earned a Ph.D. from Ohio State University, was hired by DuPont at
its Jackson Laboratory in Deepwater, N.J., to develop new refrigerants using TFE gas as a starting
point. As a result of a serendipitous discovery by Plunkett and his assistant Jack Rebok, Teflon
polymer was developed and has led to Teflon and a family of fluoropolymers used in fibers, films
and plastics in a variety of high-performance applications.
Plunkett first produced several hundred pounds of TFE gas and stored it in small cylinders
at dry-ice temperatures prior to chlorinating the TFE. When he and his assistant prepared a
cylinder for use, none of the gas came out – yet the cylinder weighed the same. When the cylinder
was cut open, they found a white powder.
Plunkett was curious about the white powder and had the presence of mind to characterize the
material for properties other than its refrigeration potential. He found the material was
heat-resistant and chemically inert, and had very low surface friction so that other materials
would not adhere to it. Although it was thought at the time that the gaseous TFE could not be
polymerized, the exact temperature and storage conditions in Plunkett’s lab enabled PTFE, later
named Teflon, to be formed. This was truly a remarkable discovery. Plunkett’s work resulted in
patents for making Teflon that were assigned to DuPont, and in 1985, Plunkett was inducted into the
National Inventors Hall of Fame for his discovery of Teflon.
Plunkett moved on to other assignments at DuPont, and DuPont’s Organic Chemicals Department
experimented with ways of safely polymerizing TFE to make Teflon. During World War II, about
two-thirds of the TFE, then known as K-416, was made for the Manhattan Project and other military
uses. Teflon was trademarked in 1945. After the war, DuPont was able to concentrate on industrial
uses for Teflon products. Teflon tapes and sheets were sold for electrical insulation, as well as
gaskets and sealers for pumps and valves because of Teflon’s extreme chemical resistance. Teflon
was produced in fiber form in the early 1950s.
DuPont initially produced Teflon filament yarns at its Richmond, Va., rayon plant. PTFE is
insoluble in most solvents and decomposes before melting. The PTFE resin is dispersed in a viscose
rayon spinning dope and extruded into an acid bath, where the dispersion is coagulated and the PTFE
forms filaments. The fiber structure is then heat-treated, and then sintered and fused into a
coherent filament. The viscose carrier material is decomposed. The PTFE fibers are then drawn.
Modifications to the process were used to form multifilament, tow and staple fibers.
Copolymers of TFE with other fluorochemicals such as hexofluoropropylene were developed. These
produced a copolymer that was suitable for melt spinning.
DuPont’s Early Work With Teflon Fibers
By the mid-1970s, DuPont developed an extensive line of Teflon fibrous products including
multifilament yarns from 200 denier up to 39,600 denier. These yarns also could be obtained in
bleached and impregnated forms. Teflon monofilament yarns were available from 4 mils to 60 mils,
and Teflon flock and staple fiber were made in 6.67 and 7.50 denier. The high price of the Teflon
fibers ($27 per pound for a 200-denier/30-filament yarn in 1974) was a limitation to early
widespread use of the fibers and dictated their use only in applications that required some of the
properties described in Table 1. Staple-type yarns of Teflon were made by direct spinning from tow
because of the difficulty of carding the slippery fiber. Multifilament yarns also were processed by
air-jet texturing for filtration fabrics and other applications.
Early Successful Teflon Fiber Applications
Braided packings made of Teflon fibers proved cost-effective for pumps and valves. The hard
packing made with Teflon fibers impregnated with Teflon dispersed resin give excellent service in
high-pressure pump and valve applications. The soft packing material, in addition to the dispersed
resin, incorporates a high-temperature inert lubricant for high-speed pumps.
Bearings of Teflon in fiber form are successfully used in high-load, low-speed areas and
require no lubrication. The coefficient of friction of Teflon fiber can be as low as 0.01 depending
upon surface speed, load and temperature. Since the static coefficient of friction for the fiber is
only slightly higher than the dynamic value, it does not exhibit stick-slip. Stern & Stern
Industries Inc., New York City, developed a line of fabrics woven of Teflon yarns for bearings that
are used on highway bridges. Other applications for Teflon-bearing fabrics include: agricultural
equipment, where non-lubrication and impact resistance are important; steel rolling mill bearings,
where high load-carrying ability and impact resistance are required; and aircraft and missiles,
where lack of stick-slip resistance under extreme temperature is required.
Filtration is an important application for Teflon fibers and yarns in woven fabrics and in
needlefelts, particularly for filtering products such as titanium dioxide; carbon black, where
temperatures as high as 500°F (260°C) are encountered; and where corrosive products like acids have
to be filtered.
Tapes and narrow fabrics of Teflon fibers have extensive use in the aerospace industry,
where they are used for wrapping and splicing of wire and cables because of Teflon’s favorable
dielectric properties, heat resistance and low flammability.
A relatively new application for Teflon yarns is Blister Guard® socks made from this
material from Friction Free Technologies Inc., New York City. The use of these socks reduces
blisters, hot spots and abrasion, and keeps the skin cooler and drier than conventional socks. Wear
tests by the US Army Rangers, Marines and Navy Seamen of socks containing Teflon showed that
calluses, blisters and hot spots are reduced by 80 percent.
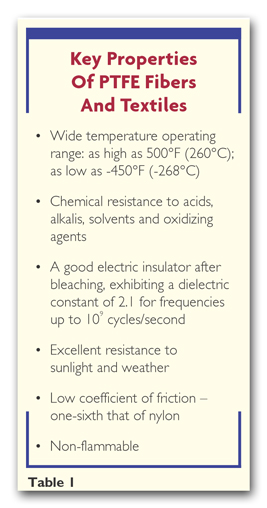
Toray Acquires
DuPont’s Teflon® Fiber Business
In June 2002, Toray Fluorofibers (America) Inc. was formed after the company purchased the
exclusive rights to the Teflon brand of fluorofibers from DuPont. DuPont sold this fiber business
in order to further reduce its dependency on the textile fibers business and to permit the company
to invest in newer businesses.
Toray will produce the Teflon product in Decatur, Ala., at a new plant estimated to cost $30
million. Equipment from DuPont’s Teflon fiber manufacturing operation in Wilmington will be moved
to Decatur.
W.L. Gore And GORE-TEX®
For some years after Teflon’s discovery, DuPont was the primary company working with
fluorocarbon chemistry. From 1945 to 1957, William L. “Bill” Gore worked on PTFE while serving on a
task force at DuPont’s research center. Since PTFE could not be extruded like nylon and other
thermoplastic resins, the only technique for making Teflon tapes and tubing was by “ram” extruding.
In 1957, Gore’s task force was disbanded. Gore continued to work with the PTFE resin in his
home workshop. He and his son Bob, who was then studying chemical engineering at the University of
Delaware, were trying to develop PTFE for computer wiring insulation. They succeeded in making a
PTFE ribbon that could be used for such insulations. Bill Gore tried to interest DuPont in further
developing the product, but at the time, DuPont was not interested in pursuing downstream products
of PTFE.
In 1958, Bill Gore left DuPont after 17 years with the company to pursue making PTFE ribbon
cable, forming W.L. Gore & Associates Inc. After two years of hard work and frustrations, he
received an order for about $100,000 of the ribbon as part of a system that monitored pressure in
water mains. By 1963, Bob Gore had received his Ph.D. in chemical engineering, and the company
occupied a new plant in Newark, Del. By 1969, sales at Gore had reached $6 million, most of which
were to the wire and cable business. Bob Gore experimented with techniques to expand PTFE by
heating and drawing techniques. This work led to making PTFE membranes in wide sheets. A surgeon
used the PTFE membrane in a vascular graft on a pig and found it was successful. It took four years
to develop GORE-TEX® vascular grafts for humans, and they now are used throughout the world for
treating cardiovascular disease. Later improvements were made to the Gore-Tex material for vascular
grafts to improve its rupture tolerance.
By 1973, the company could stretch Gore-Tex wide enough for lamination to textile fabrics.
One of the company’s objectives was to produce a breathable waterproof tent material. In the
beginning of 1976, Gore still generated 90 percent of its sales and profits from its basic wire and
cable business. Only $2 million of its sales came from microfiltration, industrial filter bags,
joint sealants and medical products. This situation was to change in 1976, when, led by a surge in
the medical products division, sales within the whole company took off and started growing at 75
percent per year. During this period, the Gore-Tex fabric division’s products were used in a
commercial tent.
In 1974, the company started working with Bill Nicolai, Early Winters Co., currently a
division of Norm Thompson Outfitters, Portland, Ore., to incorporate a Gore-Tex microporous fabric
laminate into a tent. Nicolai, an experienced mountaineer, christened the resulting tent “Light
Dimension” and it became a successful product. Gore later sold its laminates to other portable tent
makers such as Sierra West, Banana Equipment and Recreational Equipment Inc.
By 1978, Gore was selling its laminates for use in parkas and other outdoor apparel. That
year, a major crisis developed with the Gore-Tex laminates – body oils from perspiration were
clogging the microporous membrane. Gore recalled more than $3.5 million worth of apparel while it
redesigned the microporous membrane to make it more oleophobic.
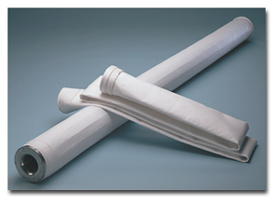
Gore’s REMEDIA™ catalytic filter system is designed to destroy dioxin and furan
emissions.
Gore Continues To Grow
Gore is still a privately held company; and now has sales of $1.35 billion, and 6,000
associates in 45 locations around the world. Filtration is an important business for the company. A
microporous Gore-Tex expanded membrane is applied to woven or nonwoven filter media to improve
filter efficiency and to improve filter cake removal in shaker-type baghouses.
Gore recently introduced its AMAZON™ filter bags, which have a hydrolysis treatment to
improve durability. These bags incorporate a Gore-Tex membrane with an aramid needlefelt. They are
designed for pulse-jet baghouses and can perform well in an acidic environment.
Gore’s REMEDIA™ catalytic filter system is designed to destroy dioxin and furan emissions.
The system is designed for use in baghouses for applications such as incinerators,
pyrometallurgical processes and cement kilns.
Gore has been producing Gore-Tex cleanroom garments for about 15 years. They are designed to
meet the requirements of ultra-clean (non-sterile) Class 1 to Class 100 environments. These
garments are flame- and chemical-resistant and have built-in static dissipation properties.
The development of microporous membrane for desalination units and the separation of other
liquids and gases is a future goal of the company.
Donaldson Tetratex®
Tetratec Corp., Ivyland, Pa., was started about 20 years ago and recently was acquired by
Donaldson Co. Inc., Minneapolis, a leading manufacturer of filtration equipment and filter media.
Tetratec manufactured Tetratex®, a microporous semi-permeable membrane film. The film repels water
while allowing air and moisture vapor to freely permeate the membrane. Product applications include
filtration, fire-fighting apparel, medical drapes and gowns, recreational tents, and apparel and
industrial garments.
Donaldson’s Tetratex will be competing in many of the same markets as Gore. This competition
should result in many new and improved products, since both companies invest heavily in their
capable research and development efforts.
Plastomer Technologies
Houston-based Plastomer Technologies produces expanded PTFE (ePTFE) monofilament for
industrial and consumer applications. One of its major products is PLASTOLON™ filtration sewing
thread. This thread has high tenacity, low shrinkage, high chemical resistance and high resistance
to ultraviolet (UV) light and sunlight. In addition to filtration applications, it is useful for
geotextile sewing and bagging for chemical products. Plastolon supplies its ePTFE sewing thread in
nominal deniers of 600, 800, 1,200, 1,800 and 3,600 on various packages.
The Plastolon product range also includes Plastolon Outdoor Fiber.
Fluorocarbon Treatments
The invention of Scotchgard™ represents another serendipitous discovery involving
fluorocarbons. In 1953, Patsy Sherman, a researcher with 3M Corp., St. Paul, Minn., was working on
a project to develop a rubber material that would be resistant to deterioration from jet fuels. An
assistant in her laboratory spilled an experimental compound on her new tennis shoes and was unable
to remove the material with soap, alcohol and other solvents. Sherman and fellow 3M chemist Sam
Smith became fascinated with the properties of the experimental compound and initiated work to
enhance the liquid repellency and the cost of this compound. As a result of this work, Scotchgard
Fabric and Upholstery Protector was launched in 1956.
In mid-2000, 3M discontinued Scotchgard Protector manufactured using C8-type fluorocarbons
because of environmental concerns over the persistence of C8 products. Since then, 3M Scotchgard
products have been reformulated with a different type of fluorocarbon material.
Coating Of Fabrics With Fluorocarbons
In 1973, the first permanent fabric structure was completed at LaVerne College, LaVerne,
Calif. The structure was built using woven glass fabric coated with PTFE resin. The world’s largest
fabric structure, the Haj Terminal, was built in the early 1970s in Jeddah, Saudi Arabia. This
structure covers 105 acres and was built to service Muslims making their pilgrimages to Mecca(See ”
From
Radomes To Mega Structures,” October 2002). More than 500 million square feet of woven
fiberglass fabric coated with PTFE resin were used for the structure. This building is a tribute to
the outdoor weathering resistance of fluorocarbon polymers.
Fluorocarbon Films For Lamination
DuPont makes Tedlar® films, which are based on polyvinyl fluoride (PVF) in oriented and cast
forms. DuPont supplies its PVF only in film form. PVF resin also can be used for coating fabrics
and other structures, but it must be applied in a solvent system.
The air-supported Paddock Chevrolet Golf Dome in Tonawanda, N.Y., is an example of how
Tedlar film is used in a fabric structure. The fabric is Shelter-Rite® vinyl-coated polyester
fabric manufactured by Seaman Corp., Wooster, Ohio, with a durable Tedlar PVF soil-resistant outer
surface. The structure is 270 feet wide, 350 feet long and 80 feet high, and does not have any
supporting pillars. When the golf driving range and the miniature golf course are not in use, the
space is used for indoor soccer, baseball or softball.
Atofina’s Products
Atofina, France, produces the polyvinylidene fluoride (PVDF) film KYNAR®. PVDF resins
have a wide processing window and can be used in a range of processes including solvent casting,
blown film extrusion, cast film extrusion and biorientation.
Monofilament Fluorocarbons
PVDF has the capability of being melt-spun into fibers. PVDF monofilaments are produced for
sewing thread, filtration and fishing lines. A major producer of PVDF monofilament products is
Shakespeare Co., Columbia, S.C. Shakespeare also manufactures monofilament yarns from most
melt-spinnable polymers including nylon, polyolefins, polyetheretherketone (PEEK™), Ryton™ and
other specialty polymers.
The properties of PVDF monofilament yarns that make them useful in textile applications are:
• outstanding resistance to weathering and UV light;
• outstanding chemical resistance;
• high continuous use temperature (up to 150°C);
• inherent flame resistance;
• low coefficient of friction;
• lowest moisture regain; and
• excellent soil resistance.
Shakespeare supplies its ISOray™ UV-resistant PVDF sewing thread in a range of diameters
from 0.006 inches to 0.012 inches (295-1,180 denier) for applications such as awnings, tents,
sails, flags and banners, tarpaulins, boat covers and filtration fabrics. These yarns can last for
up to 10 years in outdoor applications, according to the company.
Shakespeare produces a range of standard and custom PVDF monofilament yarns for fishing
lines. The refractive index of PVDF monofilaments makes them highly transparent and invisible to
fish.
Diverse, Specialized Products
Since the discovery of PTFE, the uses of fluorocarbons have proliferated in the forms of
fibers, films, coatings, surfactants and finishing agents. Although most fluorocarbons are
relatively high in cost per pound, they are very cost-effective when used in high-performance
applications. Without fluorocarbons, our present high-technology society, which uses fluorocarbons
in products from vascular grafts to aircraft and vehicle bearings, could not function.
September 2004