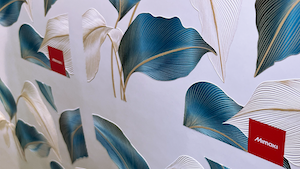
By Marc Verbeem
The print industry faces significant challenges in becoming sustainable, especially given its integral role in our daily lives. Each part of the industry has its own flaws that hinder environmental responsibility. From the chemical hazards of certain inks to the energy-intensive nature of printing technology, these issues collectively highlight that a shift towards more sustainable practices is urgently needed to reduce the industry’s environmental impact
The textile industry has been particularly under scrutiny when it comes to unsustainable production practices, particularly regarding water use. According to research by the UN Trade and Development, the textile and fashion industry is the second-largest consumer of water, accounting for about 20 percent of global wastewater. The dyeing and finishing processes with the industry require approximately 93 billion cubic meters of water annually — enough water for five million people — while generating 2 to 8 percent of the world’s global greenhouse gas emissions.1 It is estimated that fashion production comprises 10 percent of total global carbon emissions, as much as the emissions generated by the European Union.
And beyond the production itself, the microplastics and harmful chemicals in some inks end up in our oceans and natural surroundings, increasing the detrimental environmental impact of print. Addressing these challenges is crucial for reducing the industry’s environmental footprint and ensuring a greener future.
Transforming Print For A Sustainable Future
Making the switch to digital printing alone is already much more environmentally friendly than conventional printing methods. This type of printing enables on-demand, personalized prints, with no inventory or storage space required, reducing waste of all types.
While digital printing is quickly becoming the norm and is often the clear choice to support changing brand and consumer demands, manufacturers and print service providers need to look beyond the shift to digital and further innovate how to create a more environmental-conscious printing ecosystem.
Using LED-UV technology, Mimaki’s UJF, JFX and UJV printers tackle energy consumption concerns with the use of ultraviolet light to instantly dry or cure the ink as it is being distributed across the substrate. According to Mimaki’s own research, the company’s UV roll-to-roll printers consume five times less power compared to solvent printers and eight times less power compared to resin printers on the market. This is primarily due to the power consumption and heat generation of LED lights being remarkably lower than those of metal halide lamps, traditionally used to dry inks.
It’s important to look to the small changes as well as the major technological innovations, for example with inks. The majority of Mimaki’s printer inks used with sign graphic and industrial printers have achieved the GREENGUARD Gold certification and last year, 84.7 percent of the company’s ink sales for these two markets were GREENGUARD Gold certified. For textiles, Mimaki offers a range of water-based pigment inks suitable for both direct-to-fabric and transfer printing. Many of these inks hold certifications such as OEKO-TEX® ECO PASSPORT or bluesign® APPROVED, ensuring compliance with safety and environmental standards in line with Mimaki’s sustainability pledges.
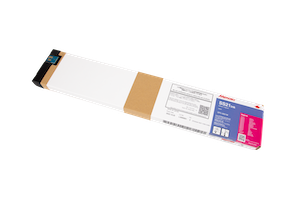
Even the packaging has been adapted. The popular SS21 ink now comes in a carton cartridge, and with this change, Mimaki can reduce annual plastic use by 29.2 metric tons, which equates to a reduction of 38 metric tons in carbon emissions. This move to carton will enable a 68-percent reduction in plastic use and is already being adopted in Europe following its success in Japan.
Innovations With A Common Thread — Sustainable Textile Production
Noting the concerns within textile printing, Mimaki focused on developing sustainable textile printing technologies, which tackle wastewater, energy consumption, while increasing efficiencies, and maintaining customers’ profitability.
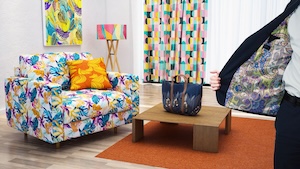
Recently introduced to the market, TRAPIS — Transfer Pigment System — is more sustainable than both analogue and digital textile dye printing methods with zero water consumption, aside from any used in the production of the material, and substantially lower carbon dioxide emissions. By simplifying the textile printing workflow to require only a large-format printer and a high-pressure calender, it eliminates the need for equipment like steaming or washing machines, making small-scale textile production more feasible and accessible locally.
The printing process involves three key elements: the Textile Pigment Ink, the Printing System and the Pigment Transfer paper, Mimaki Texcol.
Mimaki Texcol paper allows for transferring a digital print onto a wide range of materials, including natural fibers. The design is initially printed onto the paper using a slightly updated version of Mimaki TS330-1600 printer and Mimaki’s bluesign APPROVED pigment inks developed for the process. In the final stage, the Mimaki Texcol paper undergoes a one-step waterless process, through a calender machine onto the textile of choice.
Mimaki’s commitment to sustainability goes beyond the development of the company’s core solution. In an attempt to tackle one of the most pressing issues in the fashion and textile space, the company debuted a new unique concept set to revolutionize the reuse of coloured polyester textiles — the Neo-Chromato Process.
The growing awareness of sustainability has led to a significant disposal issue within the textile industry, with polyester textiles accounting for approximately 60 percent of 92 million tonnes of wasted textile materials worldwide2. Of this enormous amount of polyester waste, currently around only 15 percent is recycled. Mimaki’s Neo-Chromato Process tackles this issue head on by utilizing a discolouring technology for dye sublimation inks. By decolourizing polyester textiles that have been dyed, this innovative process allows materials to be re-printed or dyed immediately, contributing to a smaller circular economy. In fact, reused polyester can be repeatedly treated with the Neo-Chromato Process, which extends the lifecycle of materials.
Working Towards A Greener Future
While the printing industry is taking on the responsibility of creating a more environmentally friendly landscape, there is always more that can be done to further this progress. Innovative and exciting developments in technology are continuously breaking new ground, but there is still a way to go to see them being implemented globally.
While legal regulations are demanding more of manufacturers when it comes to their sustainability efforts, this shouldn’t be the driving force behind the need for change. It is important for printing companies to be both ambitious and strategic with the implementation of eco-friendly products and practices, while remaining transparent and articulating this clearly with all the stakeholders involved.
References:
1https://unctad.org/news/report-maps-manufacturing-pollution-in-sub-saharan-africa-and-south-asia
2 Based on Mimaki’s own research
Marc Verbeem, is supervisor, Product Management, Amsterdam-based Mimaki Europe.
June 26, 2025