Honeywell ExpandsSpectra Fiber ManufacturingThe specialty materials business of Honeywell International, Morristown, N.J., announced it is to expand manufacturing capacity of its Spectra® high-modulus polyethylene fiber. The need to increase capacity resulted from an increase in demand for Spectra fiber and Spectra Shield® composites.The expansion will be completed in two phases. Phase One, to be finished by the end of the third quarter 2002 and to cost approximately $20 million, includes the installation of a new gel-spinning line and additional drawing capacity at Honeywells Colonial Heights, Va., facility.Phase Two, still in the planning stages, involves the construction of a new, state-of-the-art plant. Locations in Europe, Asia and the United States are all being considered.January 2002
Textiles 2002
Textiles 2002
The worst is over, but recovery will be slow. Todays hard-pressed textile industry
coming off a miserable 2001 can probably look forward to some bottoming out, and even selective
fractional gains over the next few quarters. But by no stretch of the imagination does it look to
be anything even remotely resembling a good year.Blame it on the still-considerable number of mill
problems. Aside from the endemic headache, mills continue to face the multiple challenges of a
far-from-robust economy, excess capacity, a rapidly changing marketplace, fickle consumers and
relatively shaky financial positions.However, the situation is far from hopeless. Indeed, most
analysts see a viable domestic industry in the years immediately ahead one that may not be as large
as it once was, but one that will become relatively healthy, a lot more innovative, and
increasingly able to compete in what is now clearly a global market.To be sure, precise predictions
in these uncertain times are quite difficult to make. But at this stage of the game, heres a sketch
of what
Textile World envisions for the upcoming year:Demand: Mill output for the year as a whole
will lag behind 2001, reflecting the steady declines of the past 12 months. But on a 2002
quarter-to-quarter basis, totals should remain relatively flat. A similar pattern is anticipated
for dollar shipments, with combined 2002 totals of both mill and mill products estimated at just
under $80 billion some $10 billion under the peak hit in 1997.Inventories: Expect some improvement
in the textile mill stock/sales ratio, as holdings are slowly brought down to match lower demand
levels. But little or no further declines are seen for the mill product ratios the needed inventory
correction occurred over the past year.Prices: The combination of lackluster demand, strong
competition, and more-than-ample capacity would seem to rule out any significant price advances.
There could be some small, selective increases, but not nearly enough to make for any meaningful
advances in any major mill or mill product price categories.Costs: This is the one saving grace a
potent offset to still-sluggish prices. Specifically, there will be only modest increases in labor
rates, and they will be offset by continuing productivity gains. Fiber costs will show little or no
meaningful upward movement from current low levels.Foreign Trade: Import gains will be quite
modest, primarily because of the current domestic business slowdown. But because the economic
slowdown is now worldwide, it would be unrealistic to expect any export gains either. Look for
another huge textile and apparel deficit one that could top $65 billion for the first time in
history.Employment: Industry shrinkage is best illustrated by the continuing decline in textile and
apparel employees. Add lessened demand to rising productivity, and the textile workforce should
drop another 5 percent to 453,000 over the new year. The apparel total could be off by 7 percent,
to around 529,000 workers.Financial: Profit margins will begin to inch up, but only from very low
2001 levels. Moreover, theyll remain well under the U.S. industry average. This, in turn, will
limit any stock market recovery from recent lows though some slight uptick in textile securities is
likely as the general economy begins to improve.Capital Spending: Purchases of new, more flexible
equipment will continue and help bolster the overall upward productivity trend. Nevertheless, the
total of such outlays should dip again in 2002 as industry activity continues to disappoint and
current capacity utilization remains in the disturbing low-70s range.New Products/New Processes:
The still-growing number of new offerings is one of the industrys long-term plusses. Details seem
to assure makers of apparel and other textile-containing products of a spate of new products. These
innovations also enhance the trend toward more product differentiation something that can give U.S.
producers a leg up on overseas competitors.Another sign that the industry isnt about to disappear
is the continuing wave of mill acquisitions, consolidations, mergers, reorganizations and global
partnerships all designed to assure a viable industry over the longer pull.Finally, its hard to
ignore all the trade legislation of the past few years. While this clearly presents lots of
challenges, it also provides plenty of opportunities for U.S. textile firms to increasingly become
suppliers of choice for North American and Caribbean manufacturers.Bottom line: dont write off the
textile industry. True, mill activity has nosedived nearly 20 percent over the past few years, and
this, in turn, has dropped the mill labor force to less than half the million-plus level prevailing
as recently as 1992.A recent longer-term forecast by the prestigious DRI-WEFA economic consulting
firm calls for a basically flat mill activity pattern over the next four years, with output
declining only fractionally over this period. In the latter half of the decade, these economic
pundits see a move back into the plus column, though any gains are likely to be quite
minimal.Recent long-term government textile employment predictions tell much the same story.
Workforce totals will continue to fall. But when increased productivity per worker is factored in,
the figures suggest level-to-slightly-higher mill production levels.
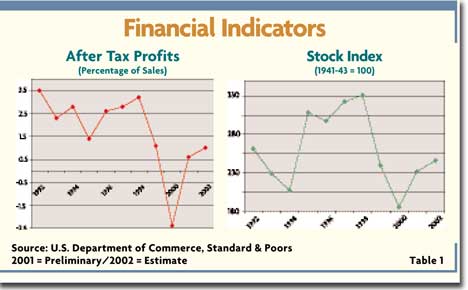
A Closer Look At 2002 MarketsAs noted earlier, overall mill production and shipment
totals over the new year arent likely to be rising much from recent levels. One big braking force
here will be the still-very-high mill inventory levels.The key textile mill/stock sales ratio now
near a 1.70 months supply is significantly above the 1.40 low in 1994. This very high ratio is
almost sure to have a negative effect on textile activity as a fair amount of early 2002 demand is
met by drawing down existing stocks rather than by new output. A relatively low mill operating rate
also doesnt bode too well for the industry. Right now, mills are operating at only 73 percent of
their potential a far cry from the 91-percent peak hit in 1994. Moreover, theres little to suggest
this key barometer will be turning up anytime soon.But not all areas of the industry will be
equally impacted by these problems. Denim markets, for one, look to remain tolerably firm, thanks
to a variety of new weaves and washes plus a still-growing interest in fashion constructions. Some
fleeces, velours and nylon types are also moving well. And corduroys, too, remain fairly
strong.Zeroing in on menswear, a fashion shift toward luxury and elegance should help both
wool/cashmeres and all wools. Biggest interest may be in light wools for pants. In coats,
wool/cashmere blends will dominate.The outlook for nonwovens is also fairly bright. And that goes
for the two segments of this fastest-growing textile area: the high-volume roll goods going into
diaper and feminine hygiene markets; and specialty markets for industrial applications.As well,
nonwovens are tending to make for new classes of products instead of replacing older markets. New
markets include allergen-barrier products, negatively charged dusting materials and vacuum filters,
and incontinence products for an aging population. But at the other end of the spectrum are several
weak spots. Khaki, for example, continues sluggish as fashion interest wanes.Carpets, too, leave a
lot to be desired as a slowing housing market could make for a second year of decline.
Floor-covering shipments are expected to be off another 1 to 2 percent in 2002, on top of last
years close to 7-percent slide.Home furnishings markets dont look especially buoyant either. The
past reflects sagging consumer optimism. But other factors here, such as growing imports and a
sluggish housing market, will also tend to put a damper on near-term sales.

No Labor Cost PressuresOn a more upbeat note for all mills, however, is the likelihood
of little or no upward cost tug on the pay front. This past year, labor rates rose by only about
1.5 percent, with only fractionally higher figures projected for 2002 and 2003. Moreover, factoring
in productivity gains, textile unit labor costs have actually been declining.This productivity
factor cant be underestimated as the industry strives to remain at the cutting edge of technology
and become globally competitive in world markets. To ensure this, the industry has invested more
than $2 billion annually in new plants and state-of-the-art equipment from 1987 onward. The figure
reached a peak of almost $3 billion in 1994.In 1999, the most recent year available, industry
capital expenditures were again near the record of just under $3 billion. Upshot: the American
textile industry consistently ranks as one of the most efficient and productive in the world.To
emphasize this last point, the American Textile Manufacturers Institute (ATMI) notes that in 1987,
the average loom produced 12.9 square meters of fabric per hour. Ten years later, the average was
34 square yards a jump of almost 165 percent.Bureau of Labor Statistics output-per-hour figures
tell the same story. They show that this past decades productivity gains for broadwoven fabrics,
yarn and thread, and knitting mills all managed to outpace those made by autos, machinery, paper,
steel and a host of other industries.Indeed, man-made broadwoven fabric and yarn and thread mills
both improved output by more than 50 percent enough to rank these two textile areas 11th and 13th
among 199 industrial categories.Still another measure of productivity progress: A decade ago, the
industry shipped $39.40 worth of product every employee hour. Recent figures show a jump to $54.20
after an inflation adjustment an efficiency gain of 38 percent. The advance was also 30 percent
larger than the average for all manufacturing. These gains have dissipated in recent quarters,
reflecting normal efficiency deadlines during a production downturn. Nevertheless, the fact that
there was no meaningful drop in mill productivity last year has to be regarded as a positive
suggesting a shift back into the gains mode again, if not over this year, then certainly by 2003.
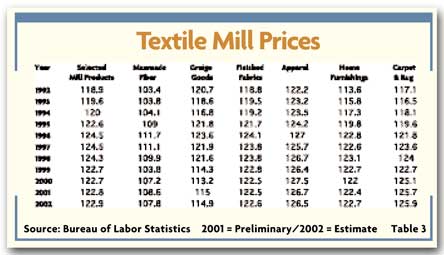
No Fiber Cost Pressures EitherFiber outlays also remain under control. Cotton quotes
have been running close to 30 cents per pound under year-ago levels, marking a 30-year low for this
key natural fiber. More importantly, theres little to suggest that this weak price pattern is about
to end. Both U.S. and global production look to remain quite high at a time when demand has been
doing little more than marking time.On the U.S. production front, some 20 million bales are seen
for the current marketing year. Factor in sluggish demand, and this suggests domestic cotton stocks
will rise 44 percent this year, to 7.7 million bales.Adding to downward price pressure is the
currently strong U.S. dollar. It makes dollar-denominated cotton a lot less attractive to foreign
buyers.The improving quality of cotton has to be regarded as yet another long-term plus for mills
one that should help the industry over the longer pull. In any case, new varieties are being
developed that are higher-yielding, higher-quality, hardier and more pest-resistant.Current
man-made fiber trends also offer some cost encouragement to mills. Quotes have been quite stable
over the past few months, with the governments official man-made producer price index actually
running fractionally under a year ago. And the pattern is pretty much the same where individual
constructions are concerned. At latest report, small year-to-year declines were noted for nylon,
polyester and polyolefins. Looking ahead, many man-mades could continue on the soft side. Aside
from overseas competition and excess capacity, theres the added downward pressure from sagging
crude oil the basic feedstock of most man-mades.How much of a drop A lot depends on when business
picks up and how much oil producers curtail production. But right now, a further 0.5- to 1-percent
slippage in this area is quite possible. Wool, too, isnt likely to cause any headaches. Theres an
ample supply around, with prices of some key grades running only slightly above a year ago. And
cashmere tags are down sharply enough to drop cashmere fabrics by as much as 12 to 15 percent under
last summers levels. Some Further Thoughts on PricesGiven the current supply-demand-cost
situation, its hard to anticipate any meaningful near-term price rebound. Best bet for 2002 is
perhaps a repeat of last years relatively flat pattern at least as far as overall mill product
averages are concerned.
TWs actual price projections for key subsectors of the textile industry are detailed in
Table 3. In virtually all cases, there are no significant advances. Even relatively strong areas
such as denim should continue to have trouble posting higher prices.Beyond 2002, however, some
modest textile price increases are possible as the economy begins to pick up steam, the positive
effects of recent North American trade legislation take hold, and current industry-strengthening
strategies bear fruit. On the latter score, these would have to include additional domestic mill
capacity declines reflecting somewhat reduced capital spending and the impact of plant shutdowns.
All told, industry potential has shrunk 3.5 percent over the past year on top of the previous years
1.5-percent decline. And this trend, which could help bolster prices, looks to continue.In any
event, the longer-run price prognosis is not all that bad. Recent DRI-WEFA projections see average
textile mill product quotes edging up as much as 1 percent annually as we move further into the new
decade.
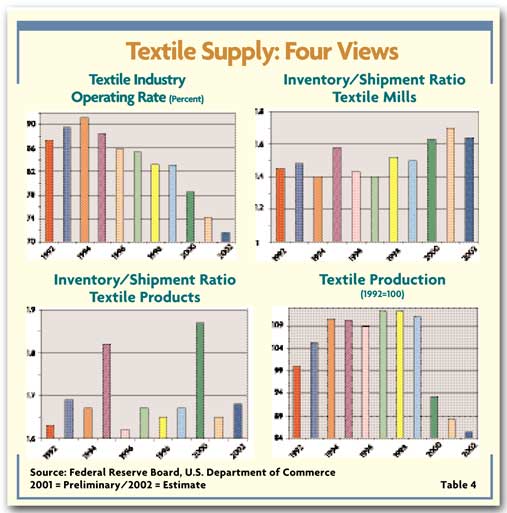
The Big Imponderable: International TradeBig question marks persist on the foreign
trade front. To be sure, imports may not grow at the pace of recent years, but they should continue
to mean the difference between a healthy and a not-so-healthy industry.If theres any doubt on the
import impact, take a look at the more than doubling of incoming shipments over the past decade.
This increase has far outweighed export gains and made for todays huge textile and apparel trade
deficit. Analysts put most of the blame on the recent Asian currency devaluations. These made for a
huge wave of low-priced textile and apparel imports.ATMI officials note textile imports from Asia
which had shown relatively little growth over a recent 10 years, jumped over 80 percent over the
next four years when Asian currencies dropped in value by an average of 40 percent.Burlington
Industries Chairman, George W. Henderson, concurs, saying that since 1995, the volume of imported
apparel has grown at five times the rate of consumption and that four out of five garments sold in
the United States today are imported.To counter all these developments, ATMI is asking for a longer
carryback period for textile companies with net operating losses; no acceleration of the Uruguay
Round quota phase-out schedule, as sought by many foreign exporters; opening up foreign markets to
U.S. textile exports; stricter enforcement of current trade laws; and strengthening of U.S. efforts
to fight textile transshipments.ATMI also wants to work with supporters in Congress to ensure that
any economic assistance to Pakistan minimizes the impact on U.S. textile and apparel industries;
and enact legislation to clarify that dyeing and finishing of U.S. fabric must be done in the
United States under the Caribbean Basin (CBI) law.Meantime, there continues to be some progress in
the export sphere. Dollar volume totals of outgoing textile and apparel shipments though admittedly
from a very small base have doubled over the past decade.Another positive sign: the shift in
imports away from the Far East and toward North America. Mexico, for example, now sends in three
times the apparel as Asia. The key point: these south-of-the-border imports are mostly made of U.S.
fabrics. Recently passed CBI legislation also has positive implications for domestic mills. Many
now see the Caribbean as at least a partial solution to their current problem. The primary
advantage of CBI sourcing, they add, is speed. In any case, CBI apparel growth should average 10
percent annually over the next few years. After that, an 8-percent growth rate seems likely. But
some of these gains could be at the expense of Mexico.This by no means implies that CBI trade wont
present problems. Some textile executives cite the complicated logistics involved in moving fabric
and apparel from country to country. The paperwork can be overwhelming.Another question mark: what
happens to CBI when trade quotas are eliminated in 2005 Some feel commodity apparel could well go
to Southeast Asia, with the CBI zeroing in on moderate and upper-moderate apparel lines. This, in
turn, suggests the need for domestic mills to develop and sell more novelty fabrics to Caribbean
Basin apparel makers. More New and Improved OfferingsThis emphasis on innovative niche
products, or improved versions of existing ones, could well be the key to survival. Not
surprisingly, virtually every large company has plans for creative introductions to entice
consumers and protect competitive positions.As one mill spokesperson puts it, more people than ever
are going to be interested in newness. Retailers will be more receptive to accept new fabrics, and
manufacturers should have better opportunities to place new products. On a similar note, another
executive said, theres a lot of opportunities if you develop the right fabrics. We always have an
eye open for high-profit niche fabrics that will be difficult for importers to imitate.One example
of the new emphasis is todays growing interest in nanotechnology the changing of the molecular
structure of fibers in a fabric to give it different properties. Some of the developments here
include providing fabrics with wicking, moisture control, and wrinkle-resistant qualities,
providing the soft hand of cotton, but the performance of polyester.In another area, Schaumburg,
Ill.-based Motorola is working on fabrics that can talk to washing machines giving instructions on
how the garment should be washed. Another firm is working on fabrics that allow the expanding of
pants waistlines with the push of a button.At Nano-Tex, Greensboro, N.C., researchers play
basketball everyday in the same socks, engineered with molecular-scaled sponges that absorb the
rancid hydrocarbons responsible for body odor. Another firm hopes to introduce a T-shirt that will
monitor heart-rate, track body temperature and respiration, and even count how many calories a
wearer is burning.Even old standbys such as denim are getting a lot of new product attention. Mills
are developing special denims with unique finishes. They want to avoid basic constructions they
feel can only be sold on the basis of price. There are also a lot more blend denims, especially
with spandex, polyester and polypropylene. Some of these add strength in the fill and wash out more
evenly. Again, its all about specialized markets with one Burlington denim executive observing:
Theres not a million yards of one fabric but a million yards made of 10 fabrics.
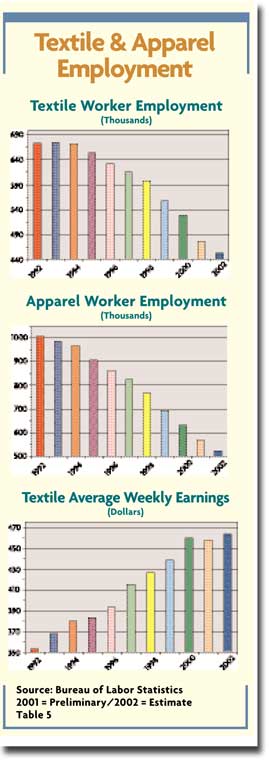
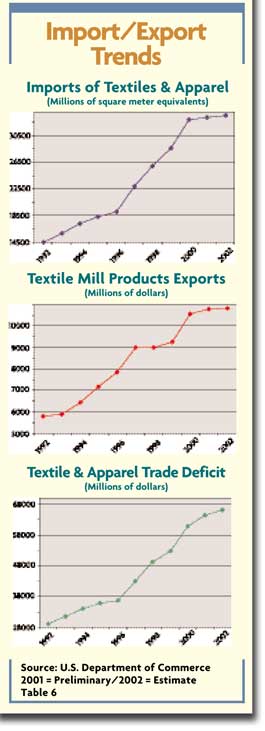
The Prognosis Is GoodThe textile and apparel industries are in a state of flux. Changes in
the works will make them almost unrecognizable in a few years. Clearly, these industries will be
smaller, more oriented toward specialty offerings, a lot more efficient, and tuned into the
electronic age. More importantly, all major players will be globally oriented. To assure all this,
advance planning, research and development will be musts. Emphasis will be on items that offer
competitive advantages to end-users.But the prognosis is good. Virtually all analysts now agree
that there will be a viable textile industry five to 10 years down the pike. But the emphasis wont
be on commodity goods, but instead, mainly on high-end goods with a limited but steady market, and
niche products where mills can maintain a competitive advantage.Thats not to say pitfalls wont
continue to exist. One things for sure: once the quota system now in place ends at the beginning of
2005, the industry will be entering unchartered waters.To end on an upbeat note: the textile
industry will survive over the long haul. Indeed, given todays underlying trends and changes, there
should be a lot more plusses to talk about next year when
TW takes its next annual look at the industrys future.
January 2002
Norstat Offers Lauer PC
Norstat Offers Lauer PCNorstat Inc., Rockaway, N.J., offers its Lauer line of industrial PCs for machinery and automation end-uses. The PCs are equipped with 12-, 15- or 18-inch resistive touch screens. A front side alpha-numeric key pad with finger mouse is used to access information. Certain models provide connection for an external PS/2 keyboard or a mouse. A standard Intel Celeron 433-megahertz (MHz) processor can be upgraded to an Intel Pentium III 700-MHz processor. Other options include 256 MB of RAM, CD-ROM, Ethernet, nickel-plated face plates and front side foils.January 2002
Solutia Introduces Vapor-Phase Heat-Transfer Fluid
Solutia IntroducesVapor-Phase Heat-Transfer FluidSolutia Inc., St. Louis, has introduced Therminol VP-3 vapor-phase heat-transfer fluid. The low-odor fluid has a boiling point of 243°C 14°C lower than the boiling point of 257°C for current vapor-phase heat-transfer fluids.That boiling point difference of just 14°C can have a major impact on the efficiency of nylon and specialty polymer operations, said Dale Kline, worldwide business manager, heat-transfer fluids. It enables manufacturers to easily process or spin nylon 6 or specialty polyester-based polymers at a lower temperature, which they could previously achieve only by operating a conventional biphenyl/ diphenyl oxide heat-transfer system under vacuum.January 2002
Industry Situation
N
ot much has changed for spinners, weavers and knitters in the United States. At a recent
meeting of textile executives, several were asked, “What are your feelings on the current state of
affairs in the textile industry?” The answers were generally the same. They might be summed up in
what one of them said: “Never in my 30 to 40 years have I seen anything like it. There have been
times when one or two segments have been bad, but I have never seen a time when all segments were
like we have now. I don’t know what is going to happen.”
One attendee responded a little more positively. He said, “I know of a few areas that are
doing okay. Some are doing so because their competition has closed down and they are getting some
of that business. Others have come up with new/different products, and a few have found a little
life in their military/uniform markets. Also, a few areas of knitting are doing very well. In fact,
I think that there are some positive signs
out there. First of all, plants stopped off during the past several months to reduce or
eliminate inventories. Inventories have really hurt. So this year will start out with very low or
no inventories. Secondly, the pipelines are about empty.” He went on to say, “I look for things to
pick up in the later part of the first quarter or in the second quarter. With inventories at such a
low level and the pipelines almost empty, any movement would translate into a positive response
from spinners, weavers and knitters.”
So, have we seen the worst of it? The optimistic outlook of the above presenter appears to
fall in line with overall views of the general economy. Economists are projecting that the general
economy will begin to improve in the third or fourth quarter of this year. If this is true, and if
history repeats itself, then we in the textile industry should expect to see an upturn during the
first or second quarter. This follows from past eco-nomic trends that indicate the textile industry
leads the general economy into a slowdown or recession, and it leads the economy out of a
recession.
How valid are these trends? No one knows. But there is one thing for certain; we in textiles
knew the economy was in recession long before it was openly stated by economists.
Cotton Prices
In the cotton market, things have become much more aggressive. Prices hit a 27-year low
during the past few weeks, and this led some speculators into the market. Last month, the Yarn
Market reported the price of cotton at 26.77 cents per pound for the base-grade
seven-designated-markets average. This month, the quoted price is 33.36 cents per pound. This is a
6.5-cent increase, or about 25 percent. As we have moved down and out of this “trough,” there has
been a large volume of fixing by producers, cooperatives and mills. Does this mean that someone
sees a glimmer of light at the end of the tunnel?
Focus On The Customer
Maybe it is time to focus more on our customer needs. It has been stated many times that the
weaving machine is one of the most effective yarn testers in the plant.
If you ask a weaver what he needs most for effective weaving, he would probably say strong
or stronger yarns. However, if you ask the same question of the weaving machine/customer, the
answer would probably be, “more consistent or uniform yarn strength.” Stronger yarns alone, or on
average, may not lead to improvements in weaving performance. In fact, lower average yarn strength,
with less variation, may contribute more to improvements in weaving performance.
As variations in yarn strength are reduced, measurements become more closely clustered about
the average, and extreme measurements are reduced/eliminated.
As a result, one would expect better weaving performance. More recently, a purchaser of
weaving yarns was asked, “What are the most important issues that you have with yarns purchased?”
He listed imprint bruises, cobwebs, overshots, no/bad/trapped transfer tail, loose ends, cuts,
tangles, rolled selvages, damaged sleeve/cone, wild yarn, malformed package/soft/hard, and run-outs
as having serious impacts on quality and production.
An interesting list, particularly since many spinners have no measurable system for these
types of defects. Given all of this, how can we give the weaving machine/customer a package that is
free of anything that might cause it to stop?
January 2002
ATMI Makes Major Cuts In Staff
Reflecting the adverse business conditions in the U.S. textile industry, the Washington-based
American Textile Manufacturers Institute (ATMI) has announced a major downsizing that will result
in the elimination of a number of key senior staff positions.ATMI President Charles A. Hayes,
Guilford Mills, said that over the next 60 days the positions of director of government relations
(chief lobbyist) an assistant director of government relations, chief economist, and director
of membership and administrative services will be eliminated. Executive Vice President
Carlos Moore will go on half-time status until a new executive vice president is hired, and he will
focus on international trade and cotton issues. While some industry observers believe the move
could seriously weaken the industry’s ability to lobby Congress and the administration, Moore said
the industry’s lobbying strength comes from its members and its textile state supporters in
Congress. He says the industry has succeeded in getting strong commitments from Congress and the
administration to address critical international trade and economic issues. “Much of the hard
work is done,” he said. ” Those commitments are in place, and our staff, our members and our
supporters in Congress are committed to following through and getting them implemented.
Beyond that, Moore said, ATMI will continue to have the services of Boyden Gray, a former
White House chief of staff, who has been successfully lobbying the administration. In
making the announcement, Hayes said: “These changes in no way diminish our continued committment to
lobby our industry’s issues in Washington. There should be no confusion as to the high priority
that effort has.”
Quality Fabric Of The Month: Intelligent Fabrics
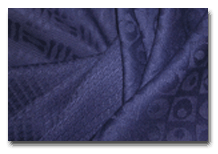
initiatives are being taken to manufacture “intelligent” fabrics that use environmentally sustainable processes as well as eco-friendly raw materials such as biodegradable or recyclable fibers and optimized dyestuffs/auxiliary chemicals.Biodegradable materials are returned to the earth as “biological nutrients” at the end of their useful lives. Recyclable materials, or “technical nutrients,” are reused over and over in new textile products.
A number of players within the industry — such as visionary architect William McDonough and chemist Michael Braungart, McDonough Braungart Design Chemistry (MBDC), Charlottesville, Va.; textile manufacturers Rohner Textil AG, Switzerland, and Victor Innovatex Inc., Quebec; textile distributor DesignTex (a Steelcase Company), New York City; and others — are collaborating to introduce at competitive prices such fabrics for use in contract furniture and transportation
applications. These fabrics include Rohner’s fully biodegradable Climatex® LifeguardFR™, a blend of wool and Austria-based Lenzing’s Redesigned LenzingFR™ — a beechwood-based cellulosic fiber
containing a flame retardant derived from a natural source and developed by Switzerland-based Clariant. Rohner has granted Victor Innovatex exclusive rights to manufacture the jacquard-woven fabric in North America.
Climatex LifeguardFR is a redesign of Rohner’s award-winning Climatex Lifecycle™, a wool/ramie climate-control seating fabric that complies with MBDC’s Sustainable Design Protocol™ for environmental soundness of materials and processes used. The fabric is dyed using 16 dye
chemicals from Switzerland-based Ciba that are free of negative environmental impacts, while complying with industry standards for lightfastness, durability and color process reproducibility. All colors except black can be produced.
Flame retardation has been among the least environmentally compatible properties found in commercial fabrics. Rohner claims the addition of Clariant’s sustainable flame retardant meets the most stringent flame-retardation standards, including those for aviation applications.
Climate-control properties are inherent in the fibers used. Wool conserves heat and absorbs moisture, while Redesigned LenzingFR transports moisture.
Victor Innovatex is introducing Climatex LifeguardFR as part of its Eco Intelligence™ Initiative (EII), which also includes fully recyclable Eco Intelligent™ Polyester made using titanium, a safe alternative to antimony, a toxic heavy metal. The fabrics are among others the
company is developing for Steelcase and DesignTex.
For more information about Climatex® LifeguardFR™, contact Jean François Gagnon (418) 227-9897;
or Beth McInnis (212) 741-4016, Ext. 21.
January 2002
Celanese Acetate And Teijin Form Marketing Alliance For Acetate Filament
KRONBERG, Germany, Dec. 20 /PRNewswire/ — Celanese AG (NYSE: CZ)(Frankfurt: CZZ) and Teijin
Limited announced today that they have signed a Marketing and Sales Assistance Agreement. Under the
terms of the agreement, Teijin will market Celanese Acetate filament products in Japan as an
independent consultant and assist in sales inthe Asia region. In a related move, Teijin will
discontinue production of acetate flake at its Matsuyama site in December 2001 and acetate filament
inFebruary 2002. The marketing alliance evolved out of ongoing joint venture discussions between
the parties. Both companies acknowledged that a contemplated jointventure was no longer viable due
to market conditions. The marketing alliance is the best way to meet the ongoing needs of Teijin
and Celanese acetate filament customers in the region. Celanese Acetate Textiles is the world’s
largest cellulose acetate filament producer. Its products are found in women’s and men’s apparel
fashions, linings, home furnishings and industrial end uses. Celanese acetate filament is currently
manufactured in the United States, Mexico and Belgium. Teijin Limited, established in June 1918,
was the first Japanese companyto produce rayon yarn and remained an innovator and leader in the
developmen tand commercialization of fibers. Today, the company’s operations encompassfour segments
— fibers, chemicals and plastics, pharmaceuticals and medical products, and diversified
businesses. The company has production and sales subsidiaries and affiliates in more than 10
countries. The parent company also has five overseas offices, as well as six plants and six
research institutes in Japan. Consolidated sales for the year ending March 2001 were761 billion
yen. Celanese AG is a global chemicals company with leading positions in itskey products and world
class process technology. The Celanese portfolio consists of five main businesses: Acetyl Products,
Intermediates, Acetate Products, Technical Polymers Ticona and Performance Products. The
Performance Products business consists of oriented polypropylene films (OPP), sweetenersand food
ingredients. Celanese generated sales of around euro 5.2 billion in2000 and has about 12,700
employees. The company has 30 production plants andsix research centers in 11 countries mainly in
North America, Europe and Asia.Copyright © 1996-2001 PR Newswire Association Inc. All Rights
Reserved.
Flexico Aims For Early 2002 Narrow Elastic Production
Flexico Inc., Mexico, a joint venture between The Moore Co., Westerly, R.I., and Grupo Industrial
Zaga, Mexico, is preparing for production of its narrow elastic fabrics beginning in early 2002.We
signed our agreement only one year ago, and Im pleased to say that progress at our new
manufacturing facility is on target. Well be shipping product to intimate apparel and orthopedic
soft-goods customers in just a few months, said Goran Elovsson, president, Flexicos U.S. Division
and executive vice president, George C. Moore Co., Moores narrow elastics division, Greensboro,
N.C.The 50/50 partnership initially increases George C. Moores capacity by 40 percent and expands
overall product lines, including the new Goflex®, an embossed knit product for use in intimate
apparel.
December 2001
Datacolor Introduces New Package Flow Machine
Datacolor, Lawrenceville, N.J., has introduced the Ahiba Multiprecise TC machine, representing the
latest technology in package flow machines. The machine was designed to help correlate laboratory
dye recipes to production-scale dyeings improving accuracy and repeatability for processes
requiring a flow technique.The Ahiba Multiprecise TC features programmable dyeing parameters; two
high-temperature dyeing chambers that run independently; specially designed sample holders; and a
patented pump that allows the dyebath to flow from the inside to the outside of the package,
ensuring level dyeing, according to Datacolor. Circle 261.
December 2001